www.industry-asia-pacific.com
26
'14
Written on Modified on
Grinding with half of the axes
At Bottero Group, KOLLMORGEN’s AKD series drives perform multiple functions With the “Titan” series, Bottero Group developed a fully automated plant for glass processing that performs bilateral grinding of pane edges. The grinder is composed of a large frame that allows the standard processing of sheets with different sizes and shapes without any operation modifications. The main objective during the design process was to create the simplest, most fully automated driving system without jeopardizing its efficiency. To achieve this aim, Bottero developed in co-operation with KOLLMORGEN a solution that is based on a single AKD servo-converter for driving two servo-motors that are not simultaneously operating.
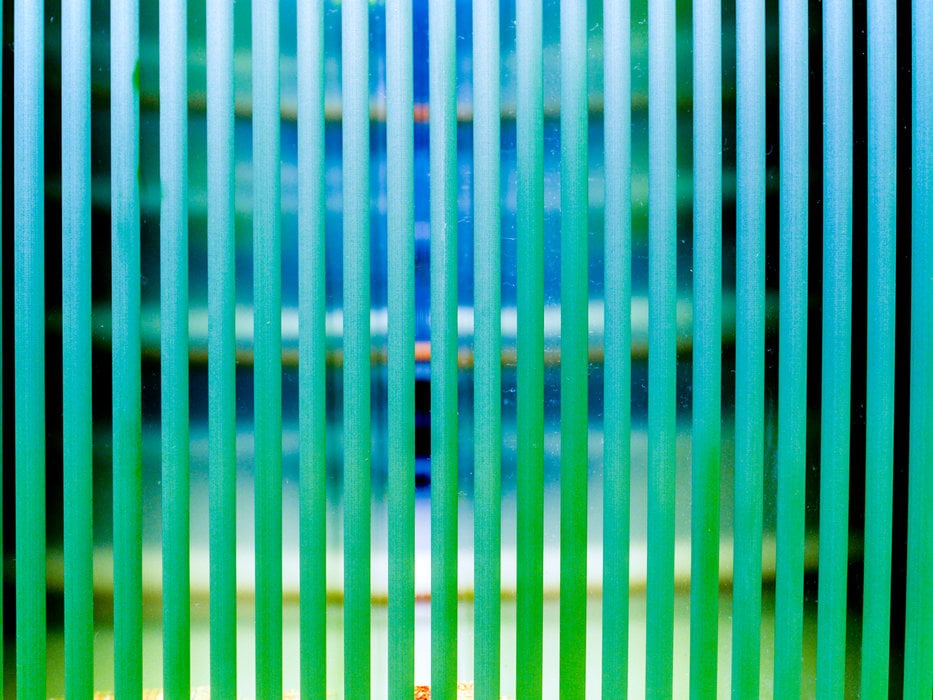
In the highly specialized market of glass processing machines, more and more automated solutions are being required. This trend is not determined so much by the need to achieve higher speeds, but rather by the need to ensure maximum machining precision. In fact, it is important to ensure both a dimensional precision and a processing quality that are optimized for every sheet of glass. This need is determined also by the development of increasingly small lots and custom sizes. For its new "Titan" models, the Italian Bottero Group, a leader in cutting and grinding glass, chose a highly efficient automation solution. The drives of the KOLLMORGEN’s AKD series operate two motors in a non-simultaneous way for widely different fields of application. The whole system is controlled by an intelligent AKD PDMM system with integrated PLC and motion control functionalities, which combine the qualities of the actuators with the most advanced functions for sequential and movement control. In Bottero plants, the AKD PDMM performs two main drive tasks: the positioning of the glass sheets and the drive of a grinding wheel. In addition, the device is also used to control the drive system with 9 AKD series drives. Thanks to its rapid regulation circuits and to the powerful control unit, the KOLLMORGEN automation platform provides ideal conditions to ensure the maximum bandwidth and to improve the efficiency. These intelligent devices with integrated motion control, cuts in half the number of drives in the glass processing machine. This breakthrough, which led to a drastic reduction of costs in terms of hardware and installation was made possible thanks to the collaboration of KOLLMORGEN, as design partner from the early stages of the project.
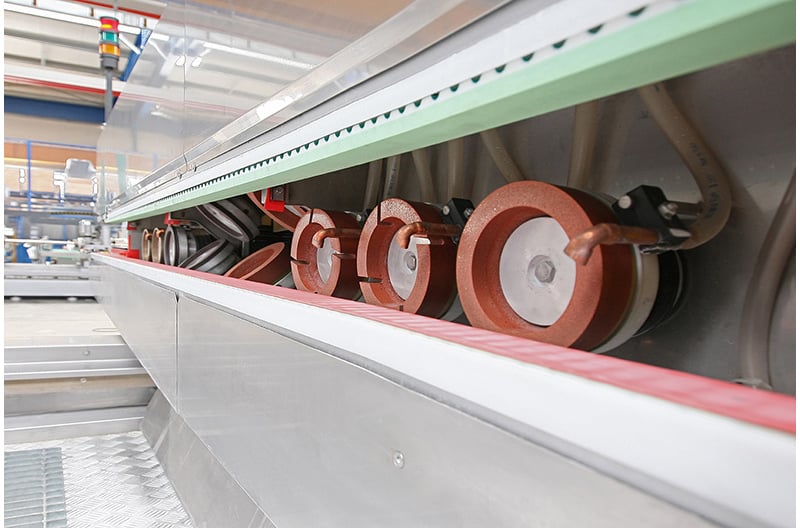
Picture: KOLLMORGEN drives allow the precise positioning of the glass sheets and the drive of grinding wheels.
A single drive for two functions
In the Titan series, the glass is transported through four toothed belts - two upper belts and two lower belts. Each belt has its own drive with synchronized axes. KOLLMORGEN’s synchronous servomotors of the AKM series use the Hiperface feedback system. Once the positioning of the plate is completed, the drives act as simple threephase speed controllers for the induction motors that operate the wheels. The tasks of the other 6 AKD drives are structured in a similar way to distribute the 16 control operations to half of the drives. The operation of induction motors is performed through incremental transducers, with either U/F characteristic curve or open regulation circuit (open loop). This rather unusual choice has come from intensive development, in which the experts at KOLLMORGEN drive systems have actively collaborated in. During the project it became clear that the motors integrated in the "Titan" models are never operated at the same time. This gave rise to the idea to connect two motors with a single servo drive. The technical implementation of this project was possible only because the KOLLMORGEN’s AKD drives have two separate X9 and X10 interfaces, which permit two different feedback systems to be connected which in turn are connected with two programmatic function blocks based on the application.
Collecting plant data
As soon as the task was completed, the respective parameters of the motor are transmitted by the central AKD PDMM through the EtherCAT Ethernet bus in real-time. The drives support communication through I/O connections on the device. In the configuration developed in collaboration with KOLLMORGEN, the drives feature 75 digital inputs, 22 digital outputs and 10 analog inputs and outputs, respectively. With this "on board" technology, Bottero saves 30% of decentralized I/O systems, reducing the hardware and installation costs, as well as space in the control cabinet.
The communication with the upper level control unit with a touch panel display system is realized through Modbus TCP.
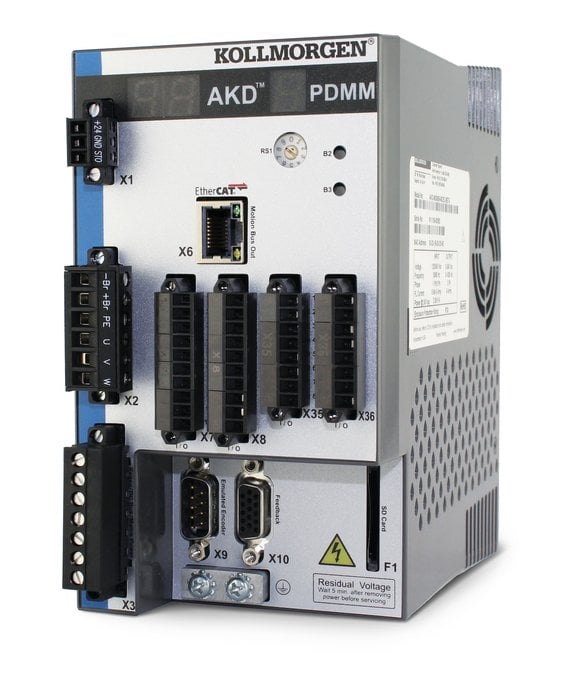
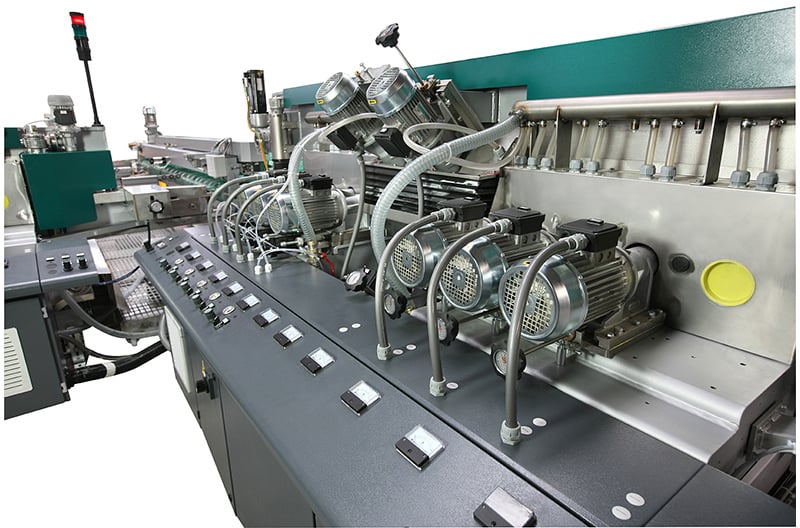
Picture: Bottero plants follow the current market trend that prefers small batch sizes.
Increasing automation
With the Titan series, Bottero has managed to meet the needs of mass production, allowing the use of the production lines both in major industries and in medium-sized enterprises. This plant is a concrete example of the increase of the automation level in the glass processing industry, oriented to a mixed production in order to provide, in a single order, a wide range of thicknesses and sizes of the product. "The companies that work the glass must be able to respond to these requests with the appropriate facilities," says Andreas Dürrstein, Bottero Sales Manager in Germany. He foresees that, in the future, the detection of the plates in the plants will take place automatically. In this case, the reading of the information occurs, for example, by means of bar codes, and allows to automatically launch the following work steps. In a highly competitive international market, dominated by mediocre products, the choice of special products, with a customized finish, offers German companies "an excellent opportunity to gain a foothold in the market," Dürrstein stresses during an interview with the Glaswelt magazine. The unique selling point of the company, based in Cuneo (Italy), is to provide high-tech and extensive know-how in all areas of the construction of machines for glass processing. Bottero builds full plants for processing of laminated and monolithic flat glass, as well as for the production of glass containers.
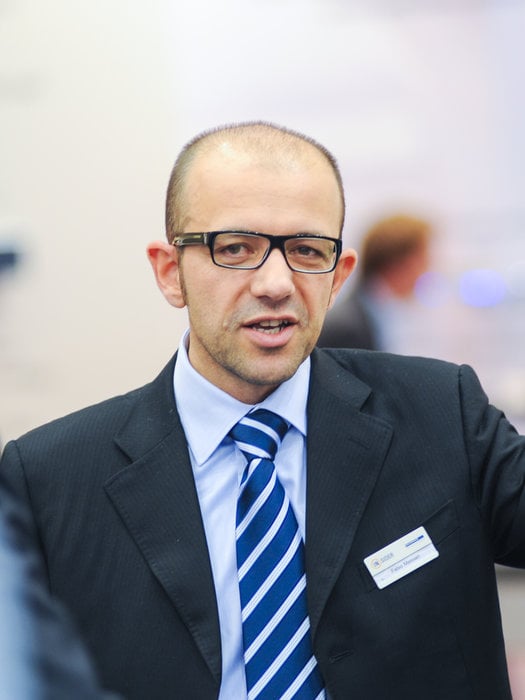
Author:
Fabio Massari,
KOLLMORGEN Italy