www.industry-asia-pacific.com
21
'21
Written on Modified on
NEW CELL FOR FRICTION STIR WELDING EXPANDS CONTRACT MANUFACTURING AT KUKA
A new friction stir welding cell from KUKA – the cell4_FSW – welds even large components with high seam strength and minimal weld distortion. At the same time, the cell offers maximum flexibility – which companies can also benefit from in the context of contract manufacturing.
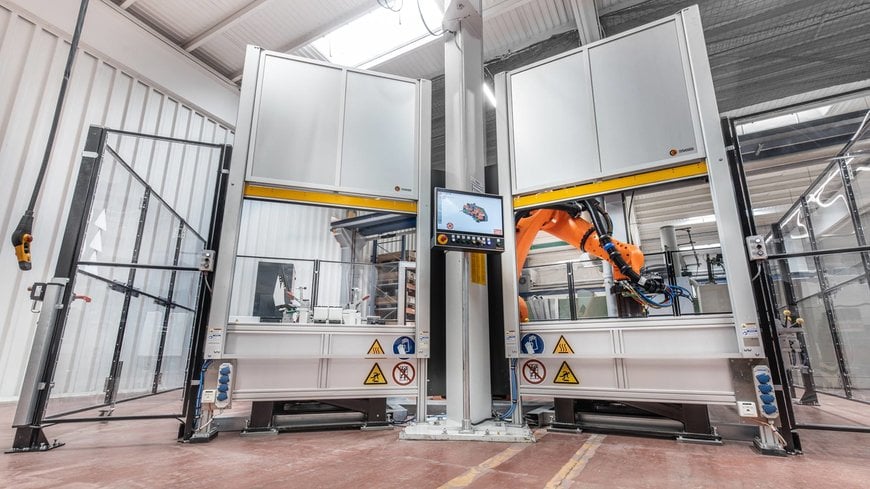
In addition to robots, software and systems, KUKA also offers contract manufacturing for special welding processes and components in any batch size. This is why the automation specialist has now expanded its own machine pool with an innovative welding cell for friction stir welding: the cell4_FSW (Friction Stir Welding). Friction stir welding primarily opens up new possibilities for joining materials that were previously only considered weldable to a limited extent: for example, high-strength aluminum and copper alloys.
Always in motion: friction stir welding as a process for contract manufacturing
The process is in demand wherever weld seams need to be really tight and, at the same time, require high strength. For example, for structural components in the automotive or aerospace industry. Thanks to the modular design of the cell, KUKA is able to meet almost every customer requirement. The cell4_FSW offers maximum flexibility for contract manufacturing – and can also be individually configured for companies investing in a cell of their own. Another plus point: compared to the gantry-based equivalent, robotic friction stir welding is more flexible and less expensive.
Compact cell delivers big performance
“There are many who can weld small components. But only a few that can weld large ones,” says Rainer Simanowski, Head of Technology Services at KUKA. “Our manufacturing cell is ideally equipped for large components thanks to two worktables, each measuring three by one and a half meters. We also have two options for loading the cell: via lift gates for small parts as well as folding doors that open across the full width of the worktable.”
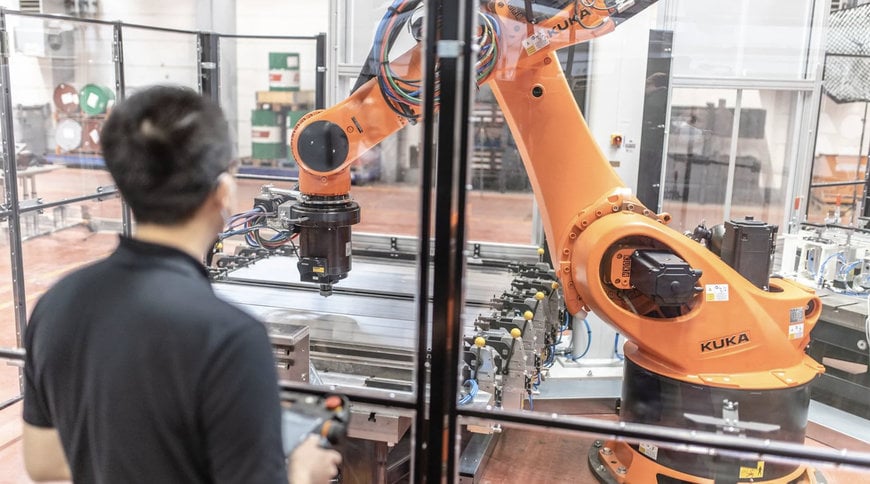
KUKA support right from the start
Size matters, but so does expertise in component and product development. As part of contract manufacturing, KUKA provides support right from the start, assists interested parties in selecting the right welding process and accomplishes orders regardless of production volume. The cell4_FSW is now expanding the KUKA portfolio in this area, which already encompassed an extensive machine pool for Magnetarc welding and rotational friction welding – for use in prototype and series production in any batch size.
KUKA facilitates entry into robotic friction stir welding
Friction stir welding is an ideal joining process for aluminum and copper materials: it can be used to weld a butt joint or a lap joint. A rotating tool (pin) is guided along the contact surfaces of the workpieces to be joined. The heat required for welding is generated by friction. Here, the material along the weld seam is only plasticized and not liquefied. An enormous advantage when used with aluminum materials: the seams are free of pores and cracks and are thus pressure-tight and vacuum-tight. “With our cell, we’re making it easier for manufacturing companies to enter into this technology,” Simanowski says. “Cost-effective, with a flexible system that makes friction stir welding attractive for any batch size.”
www.kuka.com