Schaeffler is in remote control with its virtual fitter service
Schaeffler, a global supplier of motion and mobility solutions to the automotive and industrial sectors, has launched "Virtual Fitter" – a quick and efficient rolling bearings mounting support service that operates remotely through the use of augmented reality. Available on a 24/7 basis, Virtual Fitter is available more quickly than an on-site Schaeffler expert would be, as it avoids them having to visit a location in person.
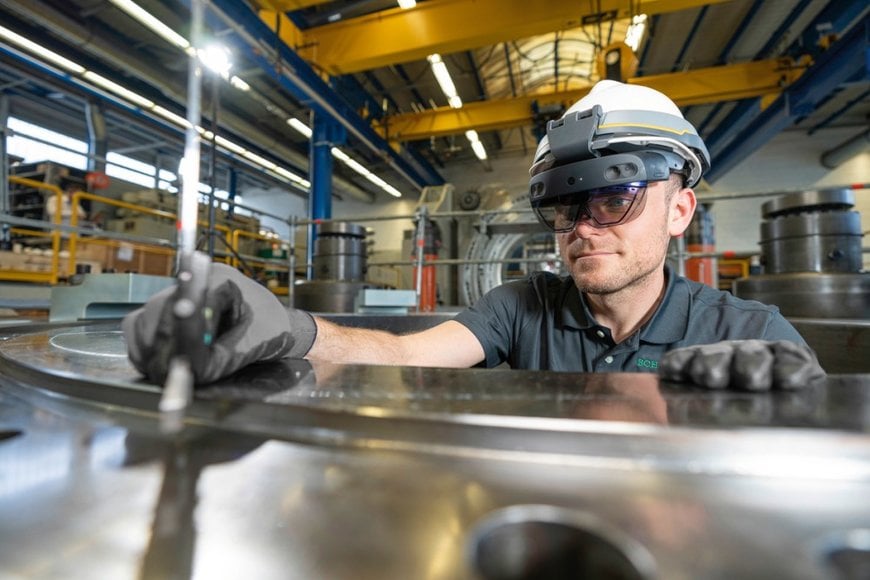
- Remote support service using augmented reality
- Reduces travel and machine downtime
- Cost savings of up to 50 per cent for users
‘We have designed Virtual Fitter to offer our customers the time and cost saving benefits of a remote service, whilst benefitting from our expert advice as soon as they need it,’ explained Sally Sillis, Schaeffler Technology Centre Manager at Schaeffler (UK). ‘They can simply rent a pair of augmented reality glasses from us, which are then worn during a machine check. At the same time, a Schaeffler fitter is connected via a secure data connection. The live transmission of photos and videos provides a comprehensive picture of a machine’s status. Any work agreed upon in advance is carried out with our guidance, with all steps documented and transmitted afterwards.’
At the heart of the Virtual Fitter service is the Microsoft HoloLens augmented reality vision system, which allows the wearer and any remote colleagues to see real life environments. It also offers an overlay of these with different sensory techniques – for example, the wearer can use the display as a white board by writing notes, or draw on it to better demonstrate ideas or workflows. The Schaeffler team has used this technology during the coronavirus pandemic to circumvent travel restrictions and ensure that the company’s future automation projects did not suffer any delays.
Virtual Fitter not only saves time but is also highly cost effective because travel and personnel expenses are reduced. In many cases, the costs associated with machine downtime are lower too. Schaeffler estimates that, when compared to its on-site service, customers save up to half in overall expenditure by using Virtual Fitter. In addition, the expert instructions also transfer know-how to the customer for future reference.
Customers that request a rolling bearings mounting service from Schaeffler will now receive two quotes to allow them to compare the costs of a personal service call on-site with the remote Virtual Fitter service. If the latter is selected, before the actual service takes place all aspects of the project will be discussed in advance to ensure the smooth and successful implementation of the work to be performed. Schaeffler will clarify whether special tools are required, which can usually be provided on loan if necessary.
Schaeffler’s Sally Sillis concluded, ‘Virtual Fitter offers a highly effective way to resolve issues quickly and with possible savings of up to 50 percent, it is already proving to be a popular option. It complements our comprehensive rolling bearings mounting service portfolio and, in a world where digitalisation and Industry 4.0 are on the rise, we see many areas where we can utilise it moving forward. In a post-pandemic environment, it has the potential to really become the new normal.'
www.schaeffler.com