www.industry-asia-pacific.com
05
'21
Written on Modified on
Renishaw process automation technologies for productivity and sustainability at EMO Milano 2021
Global engineering technologies company, Renishaw, is showcasing its latest industrial metrology process automation technologies at EMO Milano 2021.
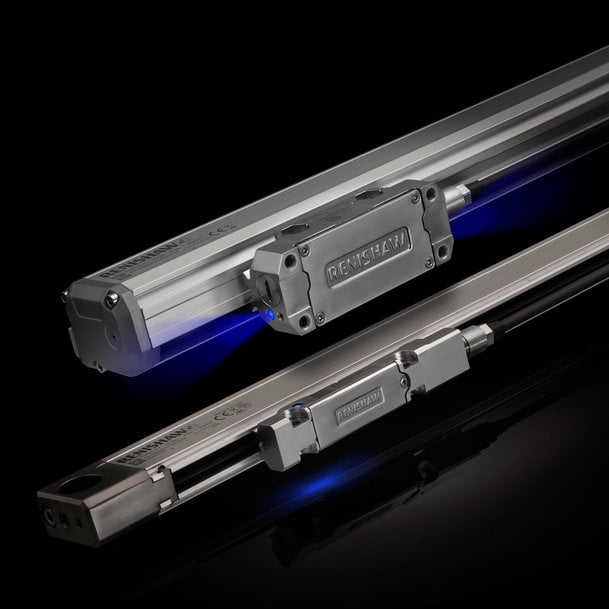
Renishaw's solutions for process automation deliver improved productivity and enhanced sustainability, ensuring manufacturers get more from their existing plant and equipment, while reducing energy consumption.
Today's manufacturers are increasingly looking to automation to drive operational efficiency and overcome skill shortages on the shop floor. However, only with process automation technologies in place can you implement the physical automation of your operations. Physical automation in turn leads to increased productivity, and productivity to sustainability through reduced waste and energy consumption.
Renishaw's industrial metrology technologies are a critical enabler for factory automation and addressing skills shortages in manufacturing. Renishaw uses high levels of automation and connectivity to master consistent, automated and productive metal cutting in its own production facilities. It now helps its partners to apply these technologies and integrate smart factory automation into their own production processes.
By implementing Renishaw process automation technologies manufacturers can extend the life of their plant and equipment, increasing machine uptime and output without adding any extra machines. With businesses increasingly focused on their environmental impact and the need to reduce costs, Renishaw's products also help customers to reduce energy consumption and minimise waste. For example, by reducing unproductive machine time, eliminating scrap components and reducing the total energy consumption required to produce the same level of machined components.
Capture more data for greater control with Renishaw's next-generation radio transmission probing system for machine tools
Machine tool spindle probing technologies are key to process automation. Data relating to the condition of parts and tools, the performance of machines, process trends, interventions and environmental effects all reflect what is happening at critical points in a manufacturing process. Data can be analysed and automatically adjusted for tool wear and drift, before a bad part is produced – all in the pursuit of zero waste, re-work and manual intervention.
New for EMO Milano 2021, Renishaw is previewing its RMI-QE next-generation radio transmission system for probing on machine tools. RMI-QE enables reliable, automated, on-machine tool setting, tool breakage detection, part set up and part verification capability. Integrating probing for process control into manufacturing processes can provide the data manufacturers need to significantly improve productivity, machine utilisation and reduce reliance on operators and human intervention.
RMI-QE offers an increase in sensor battery life of up to 400% as well as increased bandwidth, supporting a connected future in which manufacturers can capture more data, from a wider variety of sensors and probes on the machine tool. Faster data speeds also improve energy efficiency.
Situated inside the machining environment, the RMI-QE interface features an updated communication protocol and is future-proofed to support a new generation of Renishaw sensors and smart devices. Robust and reliable in busy radio environments, RMI-QE utilises an updated version of Renishaw's industry-proven 2.4 GHz frequency hopping spread spectrum (FHSS) radio transmission technology and remains compliant with radio regulations worldwide. The system is suitable for applications that cannot guarantee line-of-sight between probe and receiver – such as in 5-axis, multi-tasking and mill-turn machines. It also allows up to four separate tool setting probes or spindle probes to be operated on the same CNC machine – ideal for machining centres with rotary tables or twin pallets.
“While we are immensely proud of the technological advancements this next generation system delivers, we are equally proud of our on-going project to increase the environmental efficiency of our products,” says James Hartley, Applications and Marketing Manager for Renishaw's Machine Tool Products Division. He continues, “With the battery life improvements demonstrated here and with recent improvements to our OMP40 and OSP60 optical transmission probes, we are committed to minimising the environmental impact of our products.”
New ultrasonic probe increases the REVO® system's multi-sensor capability
Also new from Renishaw for EMO Milano 2021, is the RUP1 ultrasonic probe for use with the REVO 5-axis measurement system on co-ordinate measuring machines (CMMs).
The RUP1 probe adds ultrasonic thickness inspection to the REVO system's existing product range. Unlike many other ultrasonic systems, RUP1 does not require the use of water tanks or coupling gel to enable a good transmission of the signal. Instead, it uses an innovative elastomer tip ball to provide excellent coupling between the probe and the material. As a result, the RUP1 probe removes the need for skilled operators to interpret oscilloscope screens, and it releases shop floor real estate as immersion tanks and deep bore CMMs are not required.
The addition of extra sensors on the same CMM, enables manufacturers to significantly increase productivity. All REVO system probes can be changed automatically and include tactile scanning, touch-trigger, surface finish, ultrasonic, non-contact structured light and vision probes. They are all used within a common co-ordinate reference frame, providing the choice of an optimum tool to measure multiple features, all on a single CMM platform. Visitors to the show can see a demonstration of the RUP1 probe measuring wall thickness on a large tubular aircraft component.
Renishaw's multi-sensor technologies are also used to help manufacturing plants throughout the automotive supply chain transform their production capabilities for a more sustainable, electric future. At EMO Milano 2021, Renishaw will showcase its REVO Vision Probe (RVP) inspecting electric vehicle motor stators.
Reduce energy costs with Renishaw's new FORTiS encoder series
Visitors to EMO Milano 2021 can see a demonstration of Renishaw's new FORTiS enclosed linear absolute encoder series installed on a machine bed casting. Specialists from Renishaw will be on hand to demonstrate how easy the FORTiS scale and readhead are to install and set up inside a machine tool.
The FORTiS system has been designed to improve machine tool performance, increase uptime and reliability, and improve the efficiency of assembly, maintenance and servicing, all of which can affect productivity, sustainability and energy consumption.
Thanks to its advanced sealing system, the FORTiS enclosure offers dramatically reduced air consumption and reduced air leakage from the air purge system, resulting in lower operating costs and greater system longevity. The FORTiS system offers a reduction of up to 70 per cent in air purge requirements compared to other optical enclosed encoders, which can drastically cut the cost of operation while also reducing a machine's lifetime carbon footprint.
Ian Eldred, Principal Mechanical Engineer at Renishaw, says: “Five years of accelerated life testing, under the harshest conditions, has enabled Renishaw to develop and refine the new advanced DuraSeal lip seals. These offer excellent resistance to wear and machine tool lubricants, superior sealing and ingress protection up to IP64 when combined with air purge.”
For further information on Renishaw's latest process automation solutions for improved productivity and sustainability, visit hall 5, stand C14 at EMO Milano 2021 (4-9 October 2021).
www.renishaw.com