www.industry-asia-pacific.com
10
'21
Written on Modified on
Process optimization and flexibility
The weaving mill “Tessitura Nesi Fausto & Nesi Silvano,” in Montale, Italy mill invested in a fully equipped SAFIR S60 drawing-in machine with all Active Warp Control options, including the yarn sorting feature.
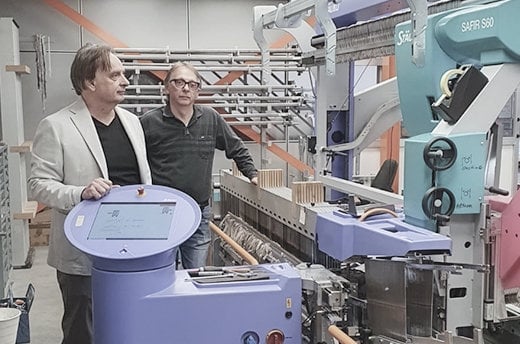
With impeccable drawing in for a high-quality weaving process, this mill enjoys excellent agility in the organization of its weaving hall and supports its position as leading supplier to premium brands that market four or more seasonal collections per year.
Tessitura Nesi Fausto & Nesi Silvano is a success story of two brothers who started producing fabrics with four Cromptom looms back in 1977. In the 1980s their goal was high productivity.
They invested in new machinery and moved the company to its current location in Montale, Tuscany. This area has been significant in the textile industry since 1950. It is particularly known for wool processing and weaving clothing fabrics under contract.
Challenges of contract weaving mills
Fausto and Silvano Nesi’s credo is to respond to customer requirements immediately. Handling a great many application types, the mill requires great flexibility in processing a wide range of yarns: unbleached or yarn-dyed (mainly medium-fine for apparel fabrics), both plain and colored, and – due to the latest trends – fancy yarns of varying thickness. The product range includes shirting fabrics, upholstery fabrics, clothing materials, technical fabrics, and more.
The company produces daily and successfully supplies a global market. The required flexibility has been achieved because the owners are passionate about meeting challenges. Over the years, they have adapted their operations to suit the market and steadily modernized their mills.
Handling numerous materials and applications involves a great number of style changes. This means that the warp beams being processed during weaving must be ready on time and in the required quantity and quality. In a perfectly organized weaving preparation department, this is standard operating procedure.
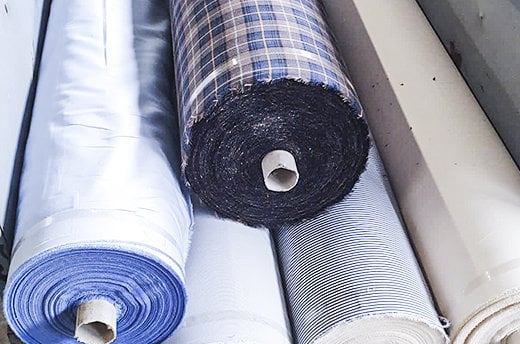
Tessitura Nesi & Nesi weaves about 80 different articles per month
Standard-setting solutions for the highest flexibility
To keep up in today’s challenging market environment, Tessitura Nesi meets every customer’s requirements and conducts numerous quality checks during weaving. The company produces premium fabrics and operates at a very high level of productivity. The managers realized that it is critical to meet high quality standards in the steps before weaving, especially in warp beam preparation, to ensure quick style changes.
Therefore, they recently invested in a SAFIR S60 automatic drawing-in machine featuring the latest Active Warp Control features (after having long used a Stäubli DELTA 110). The state-of-the art technology is unique to Stäubli. Double-end detection is a standard feature. Optional features for warps with or without a 1:1 lease – like repeat detection or the ultimate yarn sorting feature for warps without a 1:1 lease – allow automatic processing of the harness.
The machine reliably draws even fancy yarns into all elements (reed, drop wires and healds) necessary to constitute a complete weaving harness ready for the weaving machine. During drawing in, the machine manages each and every yarn according to the programmed style repeat. Faultless drawing in with no operator intervention for optimized style changes enhances the overall efficiency of the mill.
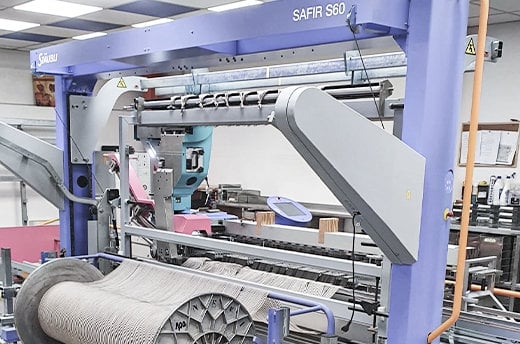
SAFIR S60 draws in directly from the warp
Ready for future challenges
With over 40 years of experience in the industry, the Nesi brothers have amassed substantial know-how. They have steadily invested in upgradable machinery like the SAFIR S60, which can be equipped with further technologies. This positions the company to guarantee quality workmanship, constantly improve, and master any new challenges the future may bring.
The second generation of the Nesi family began working in the company a few years ago and intends to continue the success story of the company. A key will remain the passion for serving customers coupled with advanced equipment from reliable providers who share the same passion for standard-setting service.
Stäubli teams in the field are always ready to provide support and advice anywhere, and spare parts are kept available even decades after the initial sale. Partners like Stäubli are very valuable to companies that aim to successfully compete in the global fabric production industry.
www.staubli.com