www.industry-asia-pacific.com
18
'21
Written on Modified on
Revamping Canada’s packaging production
With the Canadian packaging industry estimated to grow to approximately 50,000 million units by 2021, the sector has huge impact on Canada’s economic future.
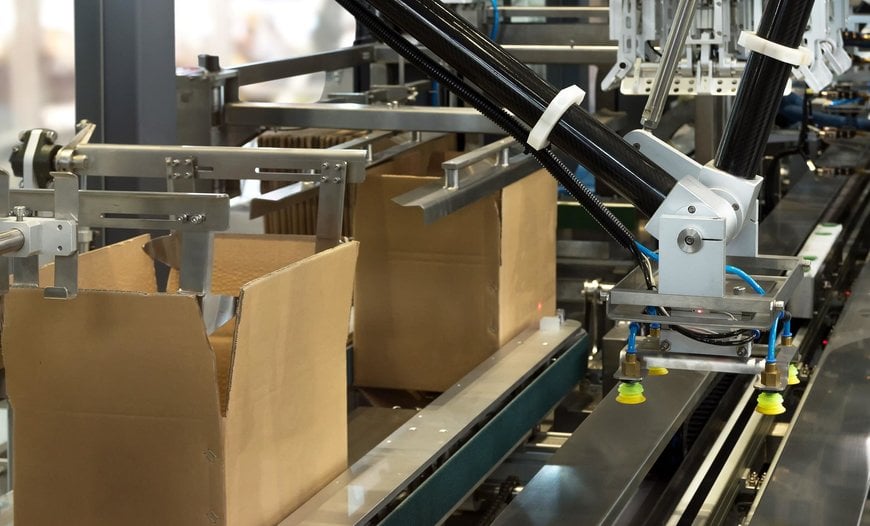
With new competitors emerging and turning to advanced technologies to gain a competitive edge, Claudia Jarrett, US country manager at automation parts supplier EU Automation, discusses how small, incremental investments can make all the difference in packaging’s industrial landscape.
Recent developments in technology have made digitalization in plants more affordable, user-friendly and robust than ever before. This has made it easier and cheaper for businesses of all sizes to invest in technology. What’s more, research from the Business Development Bank of Canada (BDC) shows that the productivity gains brought by these investments will create such an advantage that businesses will find it increasingly difficult to compete if they are not using this technology.
But what if you can’t afford it? Many small and medium sized manufacturing businesses think investing in automating machinery means overhauling their entire systems — a costly and lengthy investment. However, that’s not necessarily the case. Investing in automated machinery can be applied to any aspect of the packaging process, large or small and could still make a significant change to the productivity of the facility.
Consider this as an example. By investing in smart manufacturing initiatives, such as predictive maintenance, facilities managers can reap the rewards of improved asset uptime. This is possible by making the most of maintenance scheduling, adding integrated shop floor planning to improve asset usage and product throughput and scheduling that combined enterprise data with information from horizontal value chain partners about inventory levels, customer demands and more.
In a fast-moving consumer goods (FMCG) distribution facility, the site may have separate packaging areas for both incoming and outgoing foods. Incoming goods must be opened and unpacked before any of the materials can be sorted for distribution. For line workers, this runs the risk of severe hand strains and the potential of knife-related injuries, if box cutting is manual. However, by using an intelligent box-opening device, an encased robot which can automatically cut boxes, this small investment can eliminate any risk of injury to humans, as well as being able to increase throughput.
On the other end of the FMCG process, automation could be used to accomplish end-of-line tasks. Investing in an Automated Guided Vehicle (AGV), can be used to transport materials or accomplish specific tasks spanning the length of the shop floor. In the warehouse, they can interface with racking, perform block stacks and pick and drop from conveyors and stands. AGVs are programmed with safety in mind and as such, are fitted with cameras, lasers and other sensors that allow them to safely operate around personnel and structures. The increase in safety can also lead to reduced cost and reduced operational downtime.
Another example is flexographic printing, a popular method for printing large orders of custom labels at rapid speeds. By transferring ink onto the paper or film material using flexible printing plates, this method can increase print speeds with just a small investment. Traditionally, as these labels are being printed, a worker uses a microscope to check the labels for any discrepancies while printing. Considering the high speed that is used, a human eye is far less likely to spot any issues than when using machine vision technology. Put simply, humans make mistakes. Machines don’t.
Integrated inspection systems or cameras that use machine vision technology can also be used. By automating critical quality checks, these devices improve the speed of which detailed, quality decisions can be made. Considering any influencing factors, including plates and rollers, a line-camera based HD analysis of the printed image will provide an exact proof, as well as consistently checking and verifying the quality while printing. Quality parameters such as solids density, color location and dot gain can be automatically monitored and represented in a graph to recognize trends. This means that any deviations from the set point or target value can be quickly corrected, decreasing the amount of waste packaging created.
A growing concern in most of today’s factories is limited space availability. While the AGV is a fantastic step into automation, some factory floors simply do not have the space to implement this safely, or efficiently. With the footprint of factory machines shrinking to make more efficient use of expensive production real estate, new smaller automation components are being designed.
Another option is remote vision sensors. This technology can be used for packaging facilities that do not have the space to invest in the bigger styles of automation machinery. Traditionally, sensors are connected to their vision processor, however remote sensors can be placed in the inspection area, separated in order to conserve space. The components in these remote sensors have improved exponentially since their inception. For example, if the remote sensor is placed far from the target to be inspected, then the resolution of the sensor also increases to correctly image the targets featured.
Clearly, there’s no need to overhaul entire facilities. Just investing in one of these technologies can reap significant productivity rewards.
Digital transformation provides Canadian companies with their best chance to stay competitive in the years to come. The bottom line? Investment isn’t optional. Whether it be a full automated system or incremental investments the packaging industry will be transformed.
www.euautomation.com