GE Researchers Aiming to RAISE Combined Cycle Gas Turbine Efficiency
Aiming to set new records in gas turbine efficiency and accelerate efforts to decarbonize the energy sector, GE Research has been awarded a $1.6 million project through ARPA-E’s ULtrahigh Temperature Impervious Materials Advancing Turbine Efficiency (ULTIMATE) program to develop transformational material solutions that enable new thresholds in turbine efficiency.
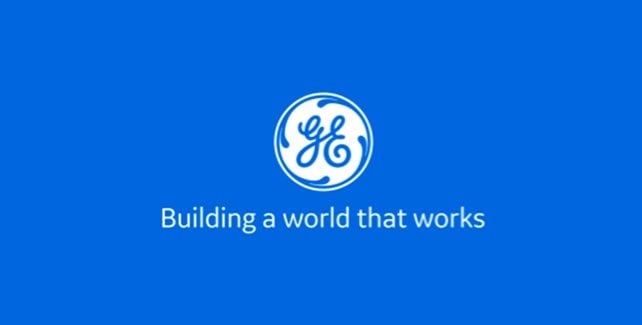
- Developing Refractory Alloy Innovations for Superior Efficiency (RAISE) – an ultra-high temperature material system that would enable gas turbine blades to operate at 1,700 °C (3,092°F)
- Will help drive efforts to push turbine efficiency beyond 65% and accelerate decarbonization of the energy sector
- $1.6 million project to be driven by world-class, multi-disciplinary team with decades of experience and a dedicated High Bay lab facility in alloy, coating and process development
Advanced materials research has long been a critical piece of GE Research’s technology portfolio, responsible for countless innovation breakthroughs over many decades to improve turbomachinery efficiency and performance in both the power generation and aviation industries.
Steady improvements have been made in both the temperature tolerance and durability of superalloys that in turn have enabled advances in power generation turbine and jet engine technologies. However, Akane Suzuki, a Principal Engineer at GE Research and project lead, says the material solutions being developed as part of this project could be a key enabler toward combined cycle gas turbine efficiency beyond 65%.
Suzuki noted that GE Research’s approach doesn’t rely on a single innovation, but several significant advances in the thermal coatings used to protect parts from heat and improve durability, the development of a new niobium (Nb)- based alloy for gas turbine blades that can withstand higher degrees of heat, and a scalable manufacturing process for producing internally cooled gas turbine blades.
Suzuki said, “Fortunately for us, we have a dedicated lab facility where we can develop and test the new materials and processes as part of our RAISE project. Materials innovation has at the core of past advances in gas turbine energy efficiency, and it’s programs like ARPA-E’s ULTIMATE that will allow the gas power sector to continue to make meaningful advances for the future.”
GE already has set world records in gas turbine efficiency. It’s HA gas turbine technology, which includes some of the most highly advanced parts and components, has helped to deliver two world records - one for powering the world’s most efficient combined cycle power plant, based on achieving 63.08 percent gross efficiency at Chubu Electric Nishi-Nagoya Power Plant Block-1 in Japan and another for helping EDF’s Bouchain Power Plant achieve 62.22 percent net combined cycle efficiency in France.
As part of this project, GE researchers will demonstrate proof of concept for its alloy composition, coatings, and manufacturing processes through modeling and lab scale testing. If successful, the team could receive additional funding to continue develop and further scale the development of their technology platform.
www.ge.com