www.industry-asia-pacific.com
02
'20
Written on Modified on
"The factory of the future can constantly reinvent itself"
An interview of Dr Stefan Assmann, Business chief digital officer, Industrial Technology business sector, Bosch Connected Industry. By Milton D'Silva.
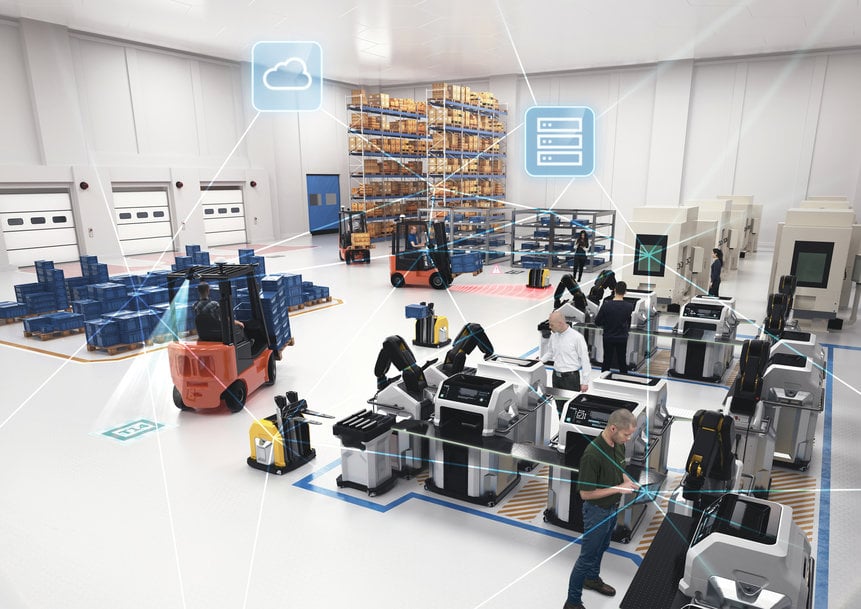
Transparency, connectivity, networking, collaboration – how easy is it for the Smart Factory to manage the contradictions?
We see no contradiction here. Instead, we believe that connectivity, networking, and transparency combine to form the basis for the ‘smart factory’. Without digitally connected machines that transmit information, production machinery cannot be connected in a network. And if our machines are not part of a network, we cannot obtain real-time transparency about what is going on. Thanks to the smart factory, processes can be continuously improved, errors detected early on, and productivity systematically increased. At the centre of all this is the human operative, who is given tools to reduce complexity and make work easier. In the Bosch vision of the factory of the future, only the floor, walls and ceiling are static and fixed, everything else is variable and flexible. Depending on requirements, the factory of the future can constantly reinvent itself. The idea is to manufacture thousands of different products and variants down to batch size one, without costly retooling. To achieve this, Bosch is relying on Industry 4.0. Our projects in this field deliver a clear benefit: Industry 4.0 allows us to increase productivity at individual locations by up to 25 per cent.
What are the impediments organisations typically face when it comes to implementation of digital initiatives in general, Smart Factory in particular?
Digitalisation projects often fail due to a lack of expertise, qualified personnel, and persistence. A smart factory cannot be built overnight. Especially when production facilities already exist, improvements have to be made gradually and methodically. Urgent problems that can be solved quickly must be prioritised and moved up the agenda. Any other things can come later.
The productivity gains of Smart Factory are well documented by now, so what explains the low adoption? What are the pre-requisites for smoother adoption?
The lack of industry 4.0 specialists and concerns about excessive capital outlay are among the biggest obstacles to implementation. But the challenges can be overcome: companies like Bosch offer a wide range of training courses. Bosch can offer over 100 training courses and seminars for Industry 4.0. In addition, Bosch experts advise customers individually and according to their needs as they move toward an intelligent factory. In the case of the expenditure involved, it’s good to have a clear plan and take things one step at a time. Once potential improvements have been identified, even small sums of money can often have a big impact. The Bosch Rexroth plant in Erbach (Germany), for example, spent 25,000 euros on sensors and photoelectric switches on production lines. This saves it around 200,000 euros a year.
How significant is the rollout of 5G and the obstacles in the rollout to enable the Smart Factory?
5G will be the central nervous system of the factory of the future. The new cellular network standard will make manufacturing more flexible, mobile, and productive. Mobile robots, autonomous transport vehicles, and new assistance systems such as data glasses that provide workers with optimum support require a high-performance wireless infrastructure. It’s all about reliable, secure, and fast data transmission with short reaction times – all this is possible with 5G. To this end, Bosch is setting up local 5G campus networks at selected plants to exploit the full potential of 5G.
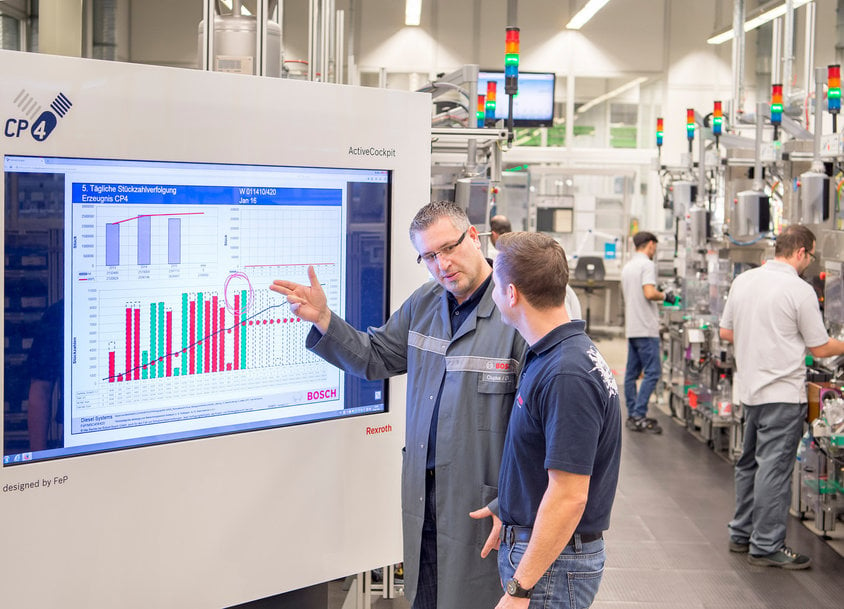
What is the extent of adoption of the Smart Factory concept in global operations of Bosch?
Bosch is an Industry 4.0 pioneer. The company has been working on bringing connectivity to its manufacturing and logistics operations since 2012. Industrial 4.0 solutions are in use at nearly all Bosch plants. These include, for example, the Nexeed software that we developed to control, monitor and check manufacturing operations in real time. More than 120 Bosch plants already rely on this Industry 4.0 solution. Bosch also offers its portfolio to third parties. While the Bosch Connected Industry business unit develops intelligent software, Bosch Rexroth focuses on smart hardware and automation technology for the factory of the future. The portfolio is rounded out by the products of our special-purpose machinery unit, which supplies customised production systems for tasks ranging from assembly to process control and test engineering.
How does Bosch as a vendor support customers in Smart Factory implementation?
Bosch experts help customers digitalise and digitally connect their manufacturing and logistics operations: from strategic orientation, to planning the right solutions, to implementation. In the shape of Bosch Industry Consulting, the company has set up a separate unit for this purpose, in which experienced Industry 4.0 experts with in-depth technology knowledge and comprehensive expertise in lean management provide customers with advice. As a leading user and leading provider of Industry 4.0, Bosch has excellent expertise. Customers thus benefit from the experience gained at around 250 Bosch plants and more than 700 logistics centres worldwide. Bosch’s Industry 4.0 portfolio ranges from software packages to robotics for manufacturing and transportation to assistance systems for workers.
Is there a need for the evolution of a vendor agnostic platform or are the various platforms already compatible?
Connectivity does not stop at factory gates or national borders. Collaboration is decisive. That’s why Bosch has signed up to “cross-industry” cloud and infrastructure projects such as the Open Manufacturing Platform (OMP). The OMP Alliance helps manufacturing companies accelerate innovations in their operations through cross-industry collaboration, knowledge and data exchange, and access to new technologies. As a founding member, Bosch is also actively involved in the development of the European GAIA-X data infrastructure. The initiative has the potential to evolve into an open, digital ecosystem that helps companies share data and scale business models worldwide. In other words, there will not be one single platform for all applications and users. This makes it important to set standards across companies and to develop products and software openly.
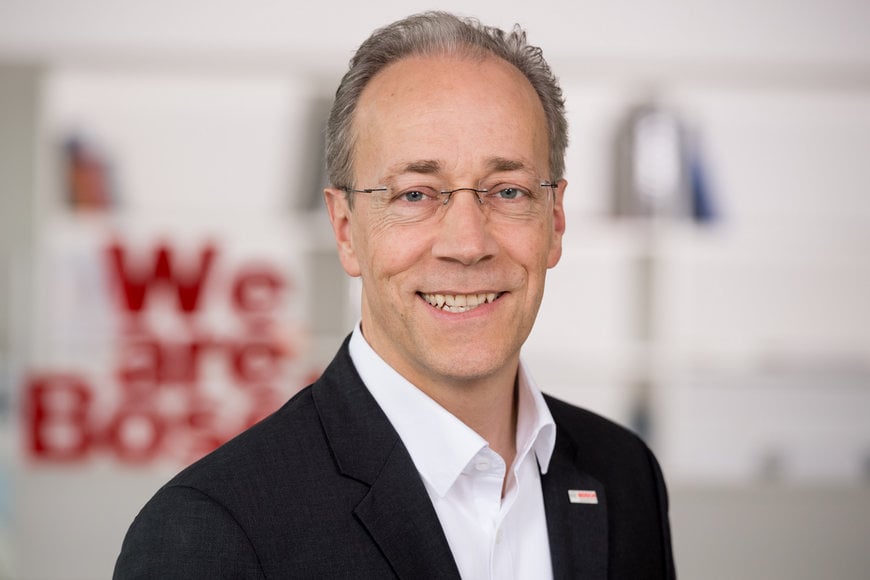
Dr Stefan Assmann, Business chief digital officer, Industrial Technology business sector, Bosch Connected Industry.
www.bosch-connected-industry.com