www.industry-asia-pacific.com
14
'20
Written on Modified on
Doosan Precision Engineering uses hyperMILL®
OPEN MIND Does a Good Turn for Subcontractor.
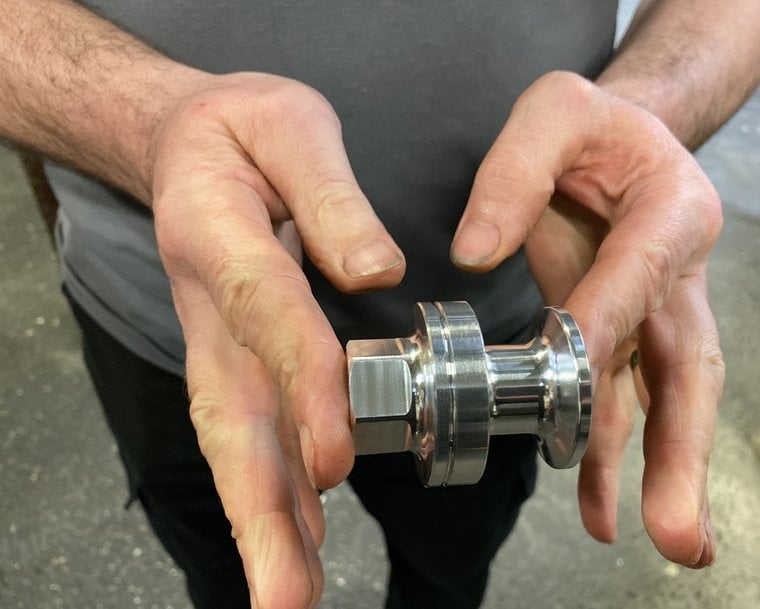
Located near Nottingham City centre, Doosan Precision Engineering specialise in CNC turning and milling; producing parts for industry sectors so diverse that the small business covers everything from motorsport to the food industry.
Founded in 2010, the small business has grown rapidly by investing in a diverse range of machine tools with multi-axis capabilities to produce parts in one-hit.
Although no relation to the Doosan machine tool brand, the company has invested heavily in the Doosan machines from Mills CNC. The company name is actually a culmination of Directors family names. The ISO: 9001 certified company has a plant list that includes a Doosan DNM 500 machining centre with a 4th-axis, plus five turning centres that includes the Doosan Lynx 300M, Doosan LYNX 220LM, two Doosan LYNX 220 LSYC machines and the newest arrival, a 9-axis Doosan MX2100ST. As a machine shop primarily conducting turning activities, Doosan Precision Engineering isn’t typically a facility where you would expect to find hyperMILL®, the industry’s leading 5-axis CAM software from OPEN MIND Technologies.

The Doosan Lynx has improved cycle times drastically since the introduction of hyperMILL®
David Booth from Doosan Precision Engineering Ltd says: “We were spending a long time setting-up some quite difficult parts with some very intricate setups to cater for difficult features that we are machining. This was the reason we initially looked at hyperMILL® from OPEN MIND. The prolonged setup times were increasing our costs and we were losing work, some of this was going overseas. Since we invested in hyperMILL®, we have managed to win this business back.”
Referring to how hyperMILL® has revolutionised the business, Mr Booth continued: “hyperMILL® has reduced the setup times massively. Some parts were taking 4 to 5 hours to program and set, the new CAM system has now reduced this to as little as 30 minutes in many cases. OPEN MIND is well respected as an industry leader in 5-axis milling technology, but we specifically bought it with turning in mind. We have one part that was originally manufactured using grooving tools to machine the scallop at the back as well as other features. Unfortunately, the challenging material demonstrates poor swarf control, now we use hyperMILL®, we can use a single button tool and the job comes off the machine completely finished.”
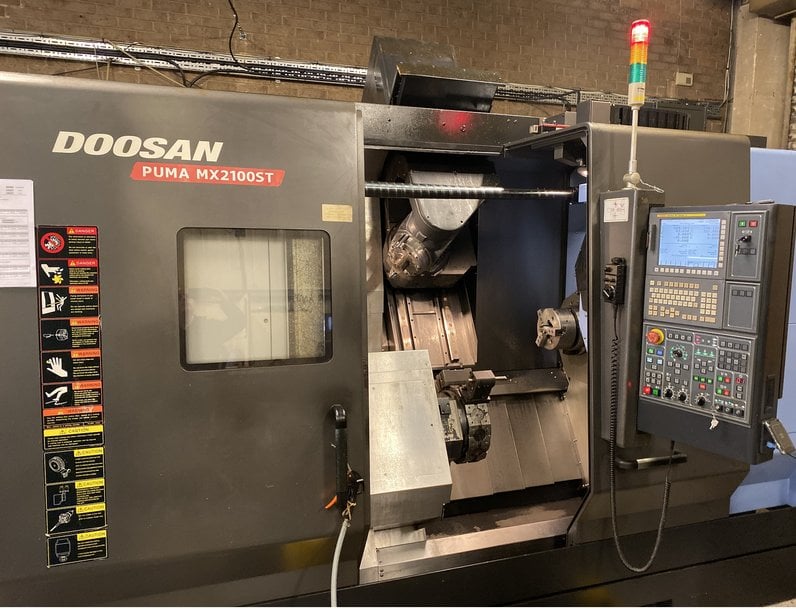
hyperMILL® efficiently controls the tool paths of the Doosan Puma turning centre
“The decision to use this single tool configuration was decided by hyperMILL® CAM software. The software selected the best strategy to control swarf and reduce the cycle time, which reduced massively when compared to the previous value.”
With regard to the programming and the cycles, Mr Booth continues: “Essentially, our customers provide us with drawings from the most of the common file types and we feed this into the CAM software. Providing we know and understand the cycles, hyperMILL® spits out a finished program. That really is about as difficult as it gets. The code generation is straight off the CAM model and is straightforward.”
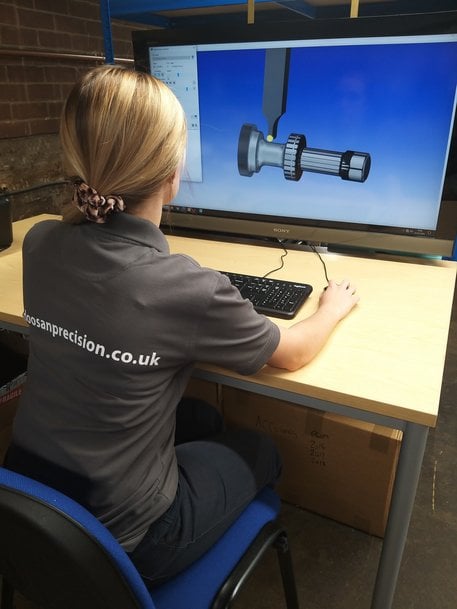
Doosan Precision has slashed turning cycle times with hyperMILL®
“We did the three-day training course at the OPEN MIND UK facility in Bicester, which was primarily focussed upon milling with some turning aspects. However, the system is intuitive and easy to pick up from scratch. We have now won back all of the work that we initially lost. hyperMILL® will certainly pay for itself in a short period of time. Of course, we also use it for all of our milling machines. The reduction in setup times has been a huge benefit to us. The ability to sit down for 20 to 30 minutes and have a finished program is a foreign concept when we compare it to what we used to have. Previously, programming was taking hours and this was a real bottleneck.”
www.openmind-tech.com