www.industry-asia-pacific.com
22
'20
Written on Modified on
Perfection in automation
22 YEARS AGO, HERMLE STARTED DEVELOPING ITS OWN AUTOMATION SOLUTIONS FOR ITS 5-AXIS MACHINING CENTRES. MUCH HAS CHANGED SINCE THEN: THE FOCUS IS NO LONGER ON REDUCING SETTING UP TIMES, BUT RATHER ON EVEN LONGER AUTOMATED PRODUCTION RUNS. AND DIGITALIZATION IS GENERATING FURTHER IMPULSES OF ITS OWN. HERMLE'S BASIC PHILOSOPHY, HOWEVER, REMAINS THE SAME: ONE PROVIDER FOR A COMPLETE PACKAGE – FROM THE INITIAL DRAFT FOR A PLANT THROUGH TO SERVICING BEYOND THE GUARANTEE PERIOD.
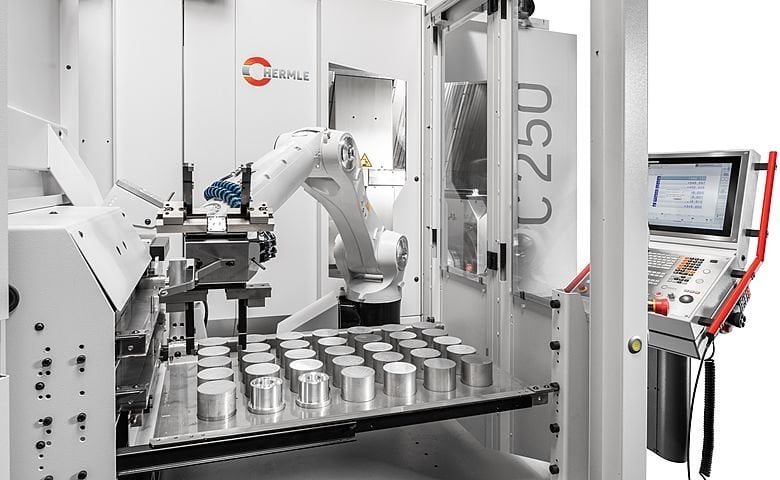
In 1998, the present Chairman of the Supervisory Board of Maschinenfabrik Berthold Hermle AG, Dietmar Hermle, laid down the basic plan for what has become a wide-ranging automation programme for 5-axis machining centres from Gosheim: He called for a proprietary solution that would enable Hermle to satisfy all customer requirements from the initial design to service provision beyond the guarantee period. Gerd Schorpp, CEO of HLS Hermle Systemtechnik GmbH, recalls the remit he received from the Chairman of the Board at the time: "A one-stop shop, no third-party interfaces." On this basis, Schorpp set up a subsidiary for designing and providing individual solutions as well as integrated robotic plant for fully automated component manufacturing. Today, it is clear how successful that venture was: "We started with 6 employees – now we have nearly 100," as the CEO points out.
At first, the aim was to reduce setting-up times. "To allow for setting up in parallel with main production runs, we at Hermle developed the first pallet changer," says Schorpp. While one component is being machined, the user can set up and mount another one. As soon as the first component is finished, the system switches the pallets, so the machine can commence the next machining cycle in a very short space of time. "Users saw that the principle worked, so we went on to the next step. If it works with two pallets, why not with several? So we enhanced our pallet changers by adding storage modules," relates Gerd Schorpp. Instead of just two, it is now possible to process up to 18 pallets in sequence. This significantly increased the running times for these precision machines.
www.hermle.de