Flexible production over several levels using Siemens technology
Within a record time of 4.5 months, Siemens has installed all conveyor technology components for the final assembly of the first fully electric Porsche, the "Taycan".
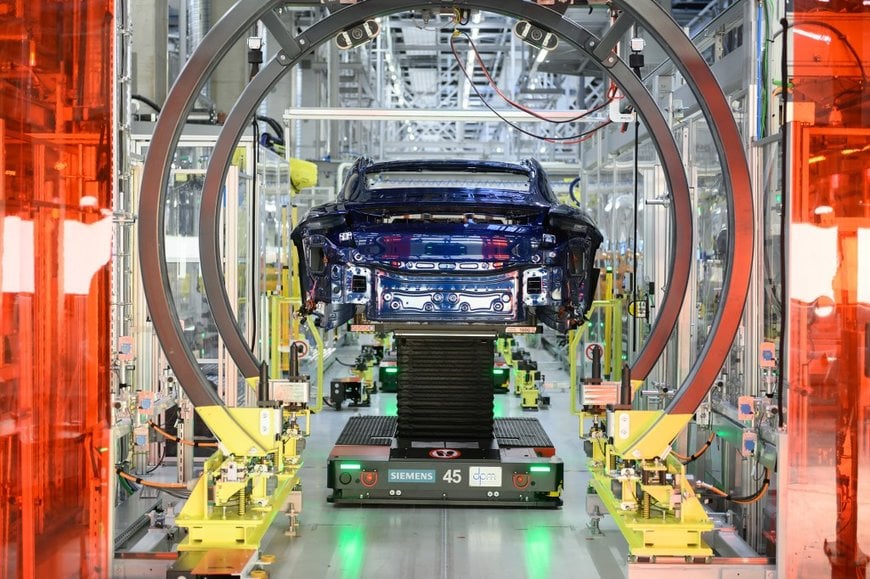
To ensure maximum flexibility in production, automated guided vehicles take the car bodies from one production station to the next.
- Top flexibility thanks to automated guided vehicles (AGVs)
- Conveyor technology solutions enable space-optimized construction
- All conveyor technology components were installed within a record time of 4.5 months only
As a result, the time from installation to production of the first vehicle was halved compared to similar projects. As, due to several building restrictions, the final assembly production line had to be built up vertically, a manufacturing concept has been developed in which each level is used for production purposes. The Taycan facility at the parent plant in Stuttgart-Zuffenhausen was put into operation in September last year.
In addition to the automated guided vehicles and the door conveyor system, tilt EMS hangers are used to ensure ergonomic working conditions.
To ensure maximum flexibility, the sports car maker left the traditional conveyor belt behind. At the so-called “Flexi-Line”, automated guided vehicles (AGVs), which are equipped with Siemens technology components, take the car bodies from one production station to the next. Operating cycles can be adapted to the actual needs and, for example, stop an AGV to perform automated tasks and then speed it up to move on to the next processing station. The conveyor technology solutions from Siemens connect the individual workstations and transport the car bodies. In addition to the automated guided vehicles and the door conveyor system, heavy and tilt EMS hangers are used. These enable ergonomic working, as the car bodies can be rotated 110 degrees in both directions so employees can access all vehicle areas without difficulty.
As, due to several building restrictions, the final assembly production line had to be built up vertically, a manufacturing concept has been developed in which each level is used for production purposes.
Due to the efficient project management, the line could be erected in parallel with the other works and the ongoing operation of sports car production. The complete final assembly process was implemented on the basis of the engineering framework Totally Integrated Automation (TIA) Portal, fully automated with Simatic controllers, and equipped with drive technology components from Siemens.
www.new.siemens.com