www.industry-asia-pacific.com
09
'20
Written on Modified on
COMAU APPLIES ARTIFICIAL INTELLIGENCE TO ENHANCE ELECTRIC VEHICLE MANUFACTURING
MI.RA/Thermography verifies the electrical and mechanical performance of joints, prevents waste and optimizes processes.
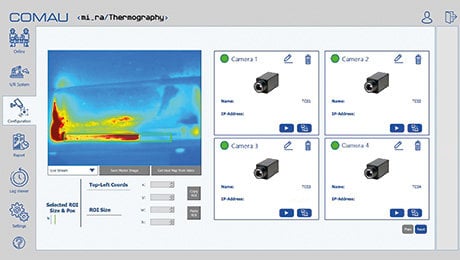
Comau has created an innovative, in-line testing and quality control paradigm that optimizes the construction and assembly of batteries. MI.RA/Thermography is one of the newest solutions within Comau’s cutting-edge vision systems family of Machine Inspection Recognition Archetypes, named MI.RA.
Designed for industrial-scale battery manufacturing, MI.RA/Thermography uses thermal imaging and artificial intelligence to perform non-invasive automated assessment and control of welded joints, to ensure battery integrity and prevent waste. Its non-destructive testing methodology protects cycle times without changing the existing manufacturing layout. Battery packs are composed of a large number of individual battery cells that are structurally held and electrically connected by numerous welded joints. High electrical resistance, due to poor joint quality, can create high energy loss and heat generation, thus increasing the joint temperature, provoking potential safety issues and reducing efficiency.
By automatically assessing surface defects and the electrical resistance of each joint before final assembly, MI.RA/Thermography can save manufacturers time and costs. Furthermore, the system doesn’t require an additional power source, as it is based on the in-line acquisition of thermal images that are immediately pre-processed, cropped and analyzed via a previously-acquired knowledge-base. After receiving a trigger from the laser welding robot, the system records the cooling phase and performs features-based analysis to fully assess the joint quality.
Benefits
- In-line process monitoring and post-process quality check
- Test, measure and control welded joints quality without affecting cycle times or line layouts
- The fully-integrated solution uses IR cameras and artificial intelligence to assess each welded joint before the final assembly
- Improved accuracy of aesthetic defect detection, often exceeds that of visual inspection
- Real-time results are collected and used for analysis and re-training
“High-precision joining is vital in the assembly and integrity of a battery and the combined use of infrared vision and artificial intelligence enables Comau to non-invasively identify esthetic, structural and electrical defects directly within the manufacturing process,” explains Giovanni Di Stefano, Chief Technology Officer – Electrification, at Comau. “In this way, we help our customers better meet the evolving requirements of the electrification market.”
www.comau.com
www.comau.com