www.industry-asia-pacific.com
17
'20
Written on Modified on
Specifying geared motors to reduce HACCP risk factors
Geared motors are found throughout food and beverage production sites, used to drive conveyor belts, stirrers & agitators, packaging machinery and other equipment along the production line. The geared motor design lends itself to energy efficiency and reliability, a must for any modern production facility. However, the food & beverage industry also requires strict hygiene compliance, meaning that specialised geared motors are a wise choice for such facilities.
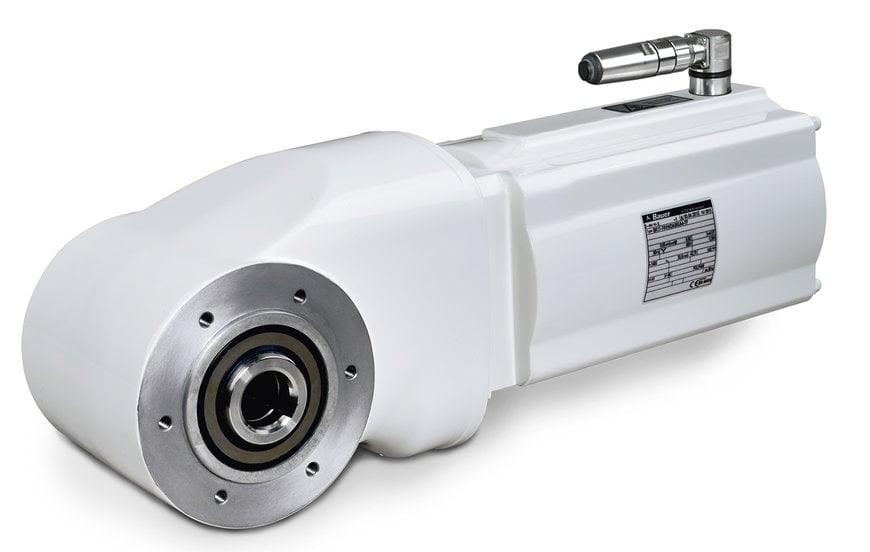
Markus Kutny, Director of Sales Vertical Markets for Bauer Gear Motor, a premier brand of Altra Industrial Motion Corp., examines how specifying geared motors in stainless steel design or specialised finishes can help reduce HACCP risk factors.
The Hazard Analysis and Critical Control Points (HACCP) system is an internationally recognised method for reducing risk factors in the production or processing of food. It works on the principle of on-going improvements, encouraging manufacturers to continuously re-evaluate each of the processes in its production line to identify possible hazards and minimise risk. The primary purpose of the system is to protect people from food-borne illness, though it is also recognised as a ‘best practice’ approach to improve quality and consistency in the final product.
Understanding the importance of the processes surrounding the analysis of risk in the production line helps to explain the evolution of geared motor technology used within the industry. Specifically, it explains why the industry requires that geared motor manufacturers invest in R&D for aseptic solutions – developing specialist coatings and even stainless steel variants of their latest products.
Aseptic drives are designed to deliver all the performance benefits of a standard geared motor, while also protecting the drive from harsh washdown cycles and preventing the build-up of microorganisms. Drives are typically painted using acid- and alkali-resistant coatings that can withstand chemicals with a pH range of 2 – 12. These drives will also usually offer high levels of ingress protection and be designed with a smooth exterior to prevent dirt build-up.
The HiflexDRIVE range from Bauer Gear Motor is an example of geared motors with design evolutions specifically aimed at improving performance in hygiene-critical applications. The range is carefully designed so that fans and cooling ribs are not required, thereby allowing for completely smooth outer casings with non-drive ends that are sealed. This allows the IE4 super-premium-efficiency motor to be offered with up to IP69K rating – which protects against high-pressure washers and steam cleaning. The elimination of venting elements creates a smooth outer surface, which provides a higher cleanability of the motor casing and prevents re-infection of the local environment caused by air movement from a cooling fan.
While specialist coatings perform exceptionally well when correctly applied and maintained, there is always a risk that the coating could become damaged while the motor is in operation. Should this happen, then the contamination resistance of the geared motor would be reduced. Adopting the principles of HACCP, many manufacturers are choosing to specify stainless steel geared motors where they are likely to be operating in an area with risk of mechanical damage.
Stainless steel geared motors – as found within the HiflexDRIVE range – meet all the regulations set out by organisations such as the FDA and NSF without the need for specialist coatings. As a base material, stainless steel is inherently resistant to corrosion and chemicals, even if it has been scratched or dented after suffering an impact.
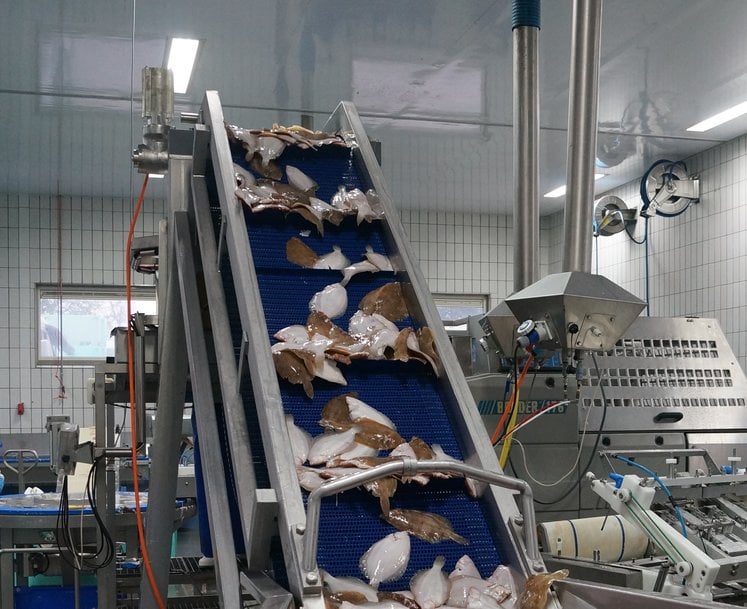
Many manufacturers are choosing to specify stainless steel geared motors in areas where increased mechanical resilience is required.
For manufacturers or packaging specialists looking to minimise HACCP risk factors when specifying geared motors, there is no question that it pays to choose a specialist solution. The HiflexDRIVE range is available in three sizes ranging from 80 Nm to 330 Nm in standard, aseptic and stainless steel designs; with power ratings up to 6.3 kW depending on the size selected. A two-stage gearbox design allows ratios of up to 109:1, depending on gear type, and allows a wide range of applications to be covered.
Whether the application would benefit most from a stainless steel design or an aseptic coating depends on the sort of working life it will be exposed to. Our engineers help customers to assess their environments and provide expert guidance on the most appropriate choice with consideration to efficiency, reliability, risk and long-term cost saving.
www.bauergears.com