www.industry-asia-pacific.com
12
'20
Written on Modified on
New controller delivers high precision for time-pressure microlitre dosing
A new time-pressure controller has been developed for precision dosing of microlitre volumes for medical and pharmaceutical applications. Bürkert’s Type 8763 Pressure Controller achieves high precision control of low flow from approximately 1.2 ml/minute and a response time in milliseconds.
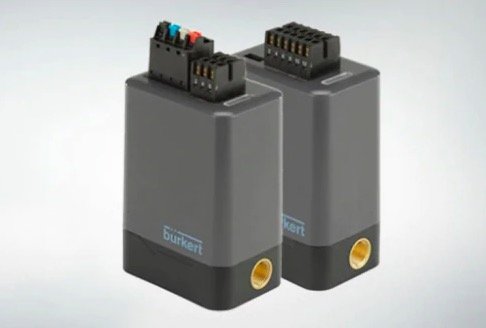
Combined with its existing range of dosing valves and pumps, release of the Type 8763 controller means that Bürkert now provides a full-service offering for micro volume time-pressure dosing. The complete portfolio from a single source is aimed at decreasing OEMs’ time to market.
High accuracy dosing
The Bürkert fluidic pressure controller is designed for in-vitro applications as well as genetic research, including DNA synthesis and sequencing. The controller is intended for process filling applications where a propellant gas is used to dose liquids as part of a time-pressure dosing system.
Bürkert’s Type 8763 closed-loop controller ensures that stable dosing of microlitre volumes are provided even with minimal pressure difference between dosing cycles. High accuracy repeatable dosing is supported with active pressure relief for precise regulation, while bidirectional control can increase or decrease pressure. Meanwhile, short response times ensure immediate and reliable pressure control. Functionality such as an additional pump or pressure sensor can also be extended through a further sensor input and actuator output.
Providing continuous dosing, saving time compared to refilling a syringe pump, Bürkert’s Type 8763 pressure controller is also free from downtime or rejects at the beginning of dosing cycles, reducing overall production time and wastage. The active vent valve also reduces operating costs by minimising consumption of expensive carrier gas.
Digital control flexibility
The Type 8763 pressure controller is available in three pressure ranges and both analogue and digital variants, with the digital alternative also incorporating analogue control. Digital communication achieves optimum process parameters by running defined pressure cycles to specific programs, which can be set according to application requirements. Predeveloped, bespoke programs with features including pressure curves and warning thresholds can also be developed by Bürkert on request.
The digital interface also enables parameters to be changed while the system is running for improved control flexibility. Automated process documentation increases process safety and access to data is also possible during system operation.
The digital variant of the Type 8763 pressure controller communicates over Bürkert Systembus (büS), based on the CANopen protocol with additional functions. The pressure controller joins Bürkert’s Efficient Device Integration Platform (EDIP), which enables intelligent networking down to sensor and actuator level over büS connectivity. Industrial communication standards including PROFINET, PROFIbus, Ethernet and Modbus/TCP are supported to enable flexible integration of system components.
The pressure controller is simple and quick to set up with plug-and-play functionality and no calibration required. Configuration, parameter setting and diagnostic management takes place with Bürkert’s free-of-charge Type 8920 Communicator software. Downloadable from the Bürkert website, the Communicator software provides an intuitive, standardised interface for büS-compatible components.
www.burkert.com