www.industry-asia-pacific.com
15
'20
Written on Modified on
Chain Condition Monitoring
Maintenance 4.0 ─ Intelligent chain monitoring avoids downtimes
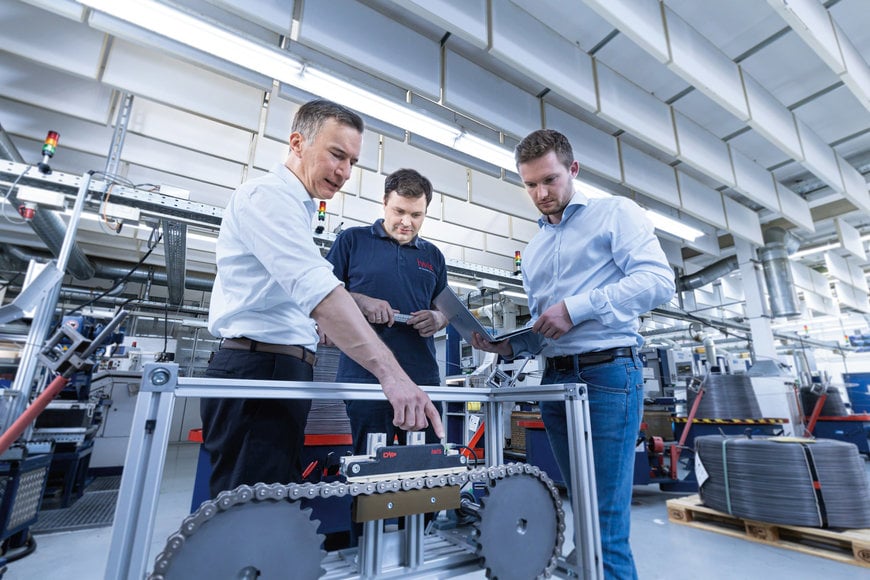
Developed in-house by iwis, the CCM-S monitoring system continuously measures the wear elongation of chains during operation and gives maintenance staff a timely warning that a chain needs to be replaced.
Predictive maintenance is a key issue in the context of Industry 4.0 when it comes to getting the most out of machines and systems. A new, intelligent system from chain vendor iwis antriebssysteme prevents production downtimes resulting from unscheduled maintenance and repairs: It permanently monitors chain elongation and provides a timely warning so that appropriate action can be taken.
If chains stretch and wear as a result of temperature and load or if chains running in parallel have different lengths, even a deviation of one percent from the nominal chain pitch can lead to problems in a machine. To take an example from chocolate production, which places very high demands on chains and chain systems, this could cause the position of the chocolate moulds to change.
This is because where chocolate bars, chocolates or biscuits are being made on a production line, the drive chains used are always subject to very strict length tolerances and tolerances across pairs of chains. The mould conveyor chains have to permanently run in parallel – exact positioning is an absolute must. Systems and machine components must therefore be monitored and checked regularly.
However, by the time the system indicates a need for maintenance or adjustment it is often already too late. Preventive maintenance allows mechanical engineers to react more flexibly and more economically.
CCM-S provides constant monitoring of the live system
This is exactly where the smart solution from the international, Munich-based chain manufacturer comes in: With the chain elongation monitoring system CCM-S (Chain Condition Monitoring ─ Smart), users can permanently monitor the elongation of chain drives on the basis of sensors without having to compromise production by interruptions.
The patented system measures the elongation of chains during live operation. It enables companies to take early measures by providing maintenance staff with timely information as to when certain measures need to be taken and whether a chain needs to be re-tensioned or replaced. The system's intelligent data analysis enables service staff to plan service activities and personnel requirements in advance.
Improved machine utilization
“Continuous chain elongation measurement offers some decisive benefits for our customers,” says Florian Wimmer, Value Engineer at iwis. “These include fewer downtimes and interruptions to production on machines and systems, which can jeopardize a company's ability to meet promised delivery dates. If maintenance can be planned, the maintenance staff can react in good time with the help of our system,” he explains.
And the time needed for maintenance is also reduced because the CCM-S tells the engineer which drive chain needs to be replaced before the system is opened up. “These benefits allow our customers to get the most out of their equipment and increase machine utilization and productivity,” Wimmer adds.
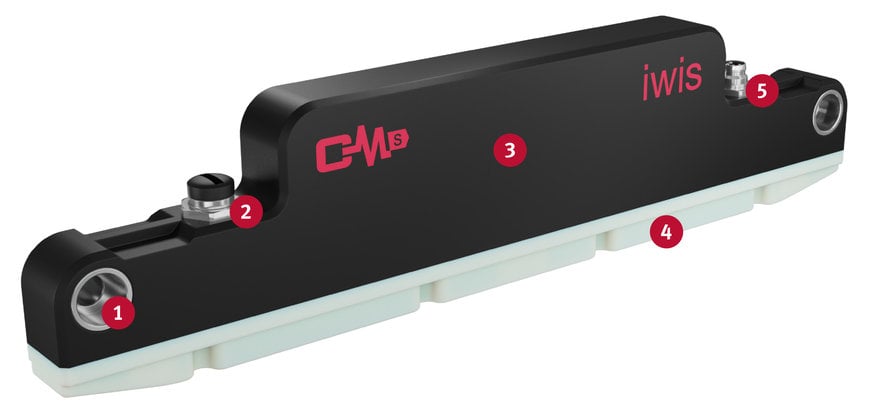
The CCM-S system measures chain elongation without any contact and does not actively intervene in the chain drive. The module can be easily retrofitted in a variety of chain applications.
1) Customer securing point (2x M6)
2) USB connector
3) Housing
4) Sliding guide
5) IO-Link connector
Simple plug and play installation
The CCM-S module is plug and play. It is very easy to install and it is no longer necessary to preset any values or perform any calibration in the application. The module is simply installed in the machine and the system is ready for use as soon as the cable is plugged in.
If the module is installed in an existing chain drive, users can immediately start evaluating the data on wear in the chain drive using either iwis software or IO-Link.
Contactless and without intervention in the chain drive
Once the monitoring system is in operation, it gets on with its job discreetly in the background: “Because it carries out precise chain length measurements without contact, the CCM system does not actively intervene in the chain drive,” Florian Madlener, Director of R&D at iwis, says of the technology behind the innovation, in the development of which he was instrumental.
The system can also take measurements irrespective of the speed. It always records two readings at two different sensor locations, with both readings being taken at the same time.
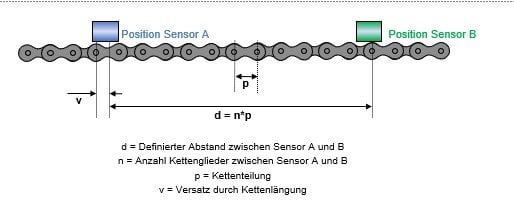
d = defined distance between sensors A and B
n = number of chain links between sensors A and B
p = pitch
v = offset resulting from chain elongation
The measured chain elongation is the difference between the defined distance between the sensors (d) and the nominal dimension of the chain (n*p). The CCM-S returns the ratio between the measured chain length and the nominal length of a new chain. This value is the chain elongation in percent.
In the CCM-S, iwis has developed a monitoring system that makes use of the physical principle of induction: The chain rollers move past the coils of the sensor and can thus be identified as a metallic unit.
Problem-free retrofitting
The developers at iwis wanted to make their smart solution as widely applicable as possible and designed the monitoring system for different chain sizes. “Since the CCM-S detects only one strand of the chain, it can also monitor duplex and triplex chains,” says Florian Madlener.
He also goes on to explain that the solution can be quickly and easily retrofitted in a variety of applications without the use of special attachments on the chains.
Thanks to an SLE function (Segment Link Elongation), the system does not only record elongation of the entire chain in the system. Using the SLE function, the entire chain can be subdivided into individual segments. These are measured individually and assessed for differences from the average chain elongation. To achieve this, magnets must be attached to both sides of the outer plates of the chain strand in order to define a start/end point. This allows the system to generate a bar chart showing the elongation of individual chain segments.
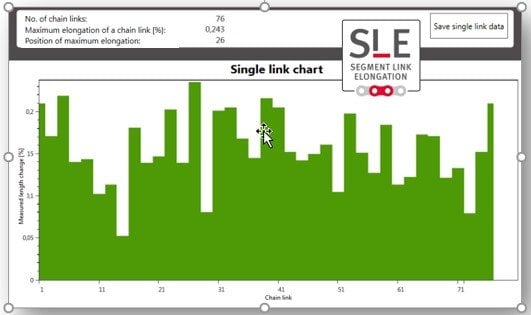
The CCM-S system can also measure the elongation of each individual chain segment and displays the results clearly.
Info box:
Technical properties
• The CCM-S system measures the elongation of the following pitch sizes:
o British Standard: Pitch sizes 08B to 32B
o ANSI Standard: Pitch sizes 40 to 160
• Ambient temperature: 0°C to 70°C
• Minimum permitted speed: << 0.1 m/s
• Maximum permitted speed: 5 m/s
• Chain material types: Carbon steel and stainless steel
• Protection class: IP67
• Interfaces: IO-Link and USB
The idea
“Increasing digitalization in mechanical engineering and the growing importance of issues such as Industry 4.0, the smart factory, predictive maintenance and condition monitoring are leading to greater expectations on the part of our customers. They want IIoT products, intelligent solutions for condition monitoring and higher plant reliability. Meeting these needs was our motivation and the driving force behind the development of a leading-edge monitoring system for chain drives”.
Florian Wimmer is a value engineer at iwis, working on the development of the CCM-S system.
Info box (optional)
What else can CCM-S do?
• Temperature monitoring
The system uses a sensor to measure the temperature at the sliding guide on the surface of the chain rollers. A lack of lubrication can be indicated by excessive chain strand temperatures. A further sensor also measures the temperature of the CPU inside the CCM-S.
• Jolt sensor
If the chain hits the sliding guide of the CCM-S, this is registered by a jolt sensor in the CCM-S. This can, for instance, be caused by stiff links, which in turn result from inadequate lubrication.
• Multi-CCM-S
Chain pitches larger than 50.8 mm can be handled by combining two CCM-S modules and mounting them one behind the other on one chain strand. Each CCM-S then works as a single sensor.
Authors:
Florian Madlener, Director Development and Testing at iwis antriebssysteme
Florian Wimmer, Value Engineer at iwis antriebssysteme
www.iwis.com