www.industry-asia-pacific.com
08
'19
Written on Modified on
Eaton announces new Synflex Optimum thermoplastic hydraulic hoses and fittings designed to work together, enabling safe and effective fluid conveyance
Power management company Eaton announced the launch of the Synflex Optimum family of thermoplastic hydraulic hoses and fittings, designed to work together to improve hydraulic system performance, simplify assembly and optimize inventory.
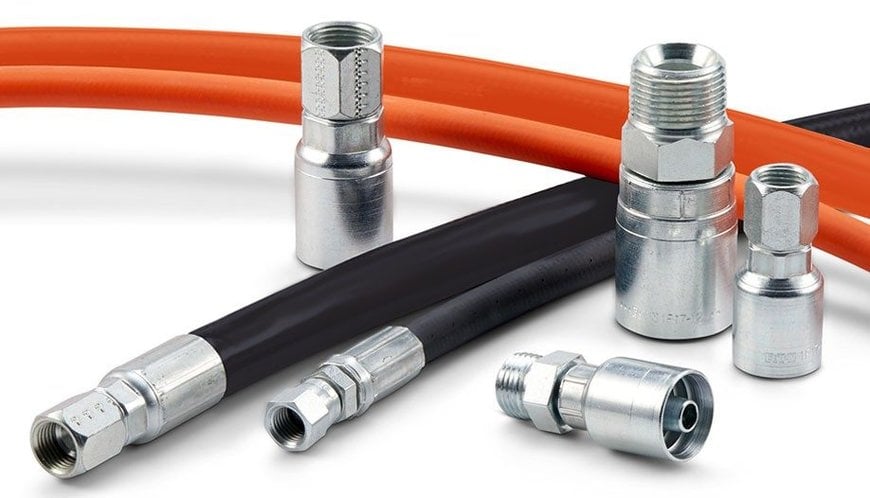
“Many manufacturers provide either hoses or fittings, leading to frustration for machine builders and end users,” said Eric Stager, product manager, Fluid Conveyance, Eaton. “Optimizing the hose and fitting to work together can result in longer hose assembly life and less equipment downtime. And because one fitting can be used across multiple hose styles, it is easier to both streamline inventory and assemble the system.”
Eaton’s Synflex Optimum hoses are built to withstand extreme environmental conditions and high abrasion applications. Constructed with a new, innovative thermoplastic material, the hoses offer the low temperature and flexibility of polyester lined hoses, along with the chemical compatibility of nylon lined hoses. Available with pressure ratings from 70 bar to 350 bar, the hoses are powerful for heavy lifting and handling equipment. Eaton’s custom thermoforming process allows for hoses to be molded into configurations that match system design, resulting in tighter routing, faster machine building and optimized performance.
The Synflex Optimum fittings, specifically designed to complement Synflex Optimum thermoplastic hydraulic hoses, feature a compact design and smaller profile for easier routing and assembly. The fittings follow a simple one-piece design to reduce matching errors and assembly time while eliminating brazing failure risks. Eaton’s captive nut helps eliminate weak spots found in other fittings and can increase safety in applications with high levels of vibration, as well as prevent cracks and leaks that lead to unplanned downtime. Dura-Kote plating, which delivers up to 1,000 hours of corrosion resistance, comes standard on the new fittings.
www.eaton.com