www.industry-asia-pacific.com
16
'19
Written on Modified on
Sustainability and efficiency: the new trends driving the plastics industry
With a combined workforce of almost 300,000 employees, plastics is one of Germany’s major industrial sectors.
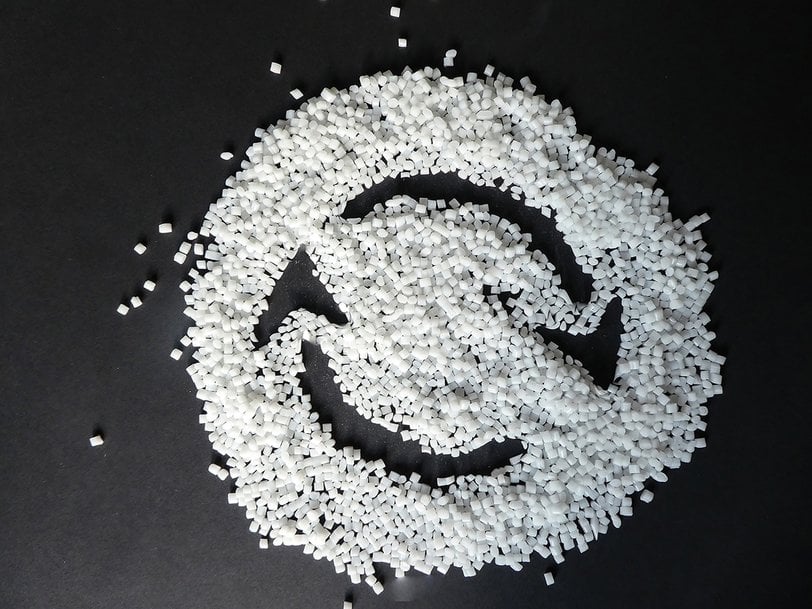
Sustainability, efficiency and the conservation of resources are some of the key topics driving social and political debate right now – and justifiably so. In this context, the spotlight has increasingly turned toward plastics. Yet daily life would be unthinkable without plastics. Likewise, it is a material that is set to play a key role in future manufacturing and industry.
At this year’s “K” trade fair – which is running under the slogan “Plastics for Future” – institutes from the Fraunhofer-Gesellschaft will be showcasing their latest technological innovations, which are designed to help make tomorrow’s plastics industry more sustainable and more efficient in terms of both energy and resources. Among the topics addressed on the Fraunhofer booth are plastics with new properties; new approaches to the production, recycling and reuse of plastics; and optimizing processes.
Reducing the use of resources in production
The aim of modern production methods should be to reduce consumption of resources while preserving a high level of product functionality. This not only increases the profitability of the product in question; it also makes a decisive contribution toward boosting the sustainability of industrial production and thereby increasing its acceptance.
This is the path followed by the Fraunhofer Institute for Microstructure of Materials and Systems IMWS with its development of lightweight structures made of organo-sandwich semifinished products. Fraunhofer IMWS has shown that it is possible to produce lightweight, ready-for-use thermoplastic sandwich structures both cheaply and efficiently in an innovative process that is suitable for mass production.
Lightweight design is likewise the field in which the Fraunhofer Institute for Applied Polymer Research IAP is presenting a new development. Using a new type of furnace that generates temperatures of up to 2850 °C, researchers from Fraunhofer IAP have succeeding in producing biobased carbon fibers from renewable materials, the properties of which partially surpass those of conventional carbon fibers. In addition, this new process yields a substantial reduction in production costs.
The Fraunhofer Institute for Wood Research, Wilhelm-Klauditz-Institut, WKI is also showcasing an innovation that conserves resources: an ecological and sustainable plastic tray for transporting small items. Polypropylene trays are used for transporting and storing millions of items every day in wholesale, retail and industry.
Fraunhofer researchers have now succeeded in replacing up to 25 percent of the polypropylene used in the manufacture of such trays with wood fibers. In addition, the new trays are not only more sustainable but also stronger and lighter – for the same production costs.
New materials developed by the Fraunhofer Institute for Chemical Technology ICT are set to give recycling a significant boost. The new self-reinforced PLA composites from Fraunhofer ICT have a high mechanical strength and rigidity, even at elevated temperatures. And, like pure PLA, they are fully biobased as well as being ductile, easy to recycle and industrially biodegradable.
Furthermore, the energy consumed during PLA production – and thereby also its CO2 equivalent – is around half that involved in the production of conventional carbon fiber-reinforced polymers such as those containing polypropylene. In addition, the new process substantially reduces production costs.
From recycling to upcycling
Of all materials, there is perhaps none better suited for recycling and reuse than plastic. The options here are highly varied and range from a simple recycling of plastic as a material, to its reuse in some form of upcycling, to a thermal recovery of energy by means of combustion.
The Fraunhofer Cluster of Excellence Circular Plastics Economy is demonstrating how to design, for plastics, a chain for recycling energy and materials in line with circular principles. The consortium behind the cluster develops special services for, and in partnership with, the plastics industry, including associated consumer goods and trading companies as well as the recycling industry.
One of the key challenges facing the industry is how to deal with certain types of plastic waste such as foil wrapping. The Fraunhofer Institute for Structural Durability and System Reliability LBF is currently investigating this problem.
In a project entitled Up-cyclePET, Fraunhofer researchers have joined forces with the company EASICOMP GmbH to develop high-grade materials from short-lived plastic waste for further use in long-lived applications such as lightweight automotive parts. Providing the base material are used beverage bottles made of polyethylene terephthalate (PET).
The Fraunhofer Institute for Interfacial Engineering and Biotechnology IGB is also investigating the use of waste as a source of manufacturing feedstock. Such sources include the natural substance 3-carene, which is a constituent of turpentine and occurs in this form as a byproduct in the production of cellulose pulp from wood.
Common practice to date has been to dispose of it by incineration. However, using new catalytic processes, researchers from Fraunhofer IGB have now succeeded in converting 3-carene into substances that can be used as components for biobased plastics. These new organic polyamides are not only transparent but also have a high thermal stability, which makes them suitable for a wide range of applications.
Increased efficiency from innovative processes
In order to make the plastics industry more sustainable and efficient in terms of energy and resources, various other key issues must be addressed. These include an enhancement of existing processing methods and the development of new ones.
The Fraunhofer Institute for Process Engineering and Packaging IVV is exhibiting an intelligent device for testing peelable packaging. The Pack Peel Scan is used to measure the force required to open plastic trays and plastic film packages.
The recorded data can then be directly used for evaluating the quality of the seal. In addition, specific data on the variation in the force required during the opening of packaging can also be applied in conjunction with machine-learning methods (AI) in order to predict process errors.
Microfluidic systems are used to transport, filter and mix minuscule quantities of liquid in the microliter and picoliter range. Medicine and biotech are classic areas of application for this technology. The Fraunhofer Institute for Laser Technology ILT has perfected the production of customized microfluidic chips by means of a laser-based process that offers a range of advantages.
For example, there is no need for the use of absorbents. Moreover, a laser beam can be used to individually polish selected areas, thereby achieving a high degree of transparency for applications such as spectroscopy.
The Fraunhofer Institute for Applied Optics and Precision Engineering IOF is demonstrating an enhanced technique for atomic layer deposition (ALD). This a key coating process, used, for example, to achieve uniform optical properties across the entire inner and outer surface of plastic optics.
The Fraunhofer Institute for Manufacturing Technology and Advanced Materials IFAM is presenting a new development in the field of sensor technology. This new gesture-recognition sensor from Fraunhofer IFAM is made of a polymer-based material and used to control Industrie 4.0 applications. The sensor is cost-effective and well suited to a wide range of applications.
SAMMI is a new system developed at the Fraunhofer Institute for High Frequency Physics and Radar Techniques FHR. It is designed to scan items on a conveyor belt or production line and uses high-frequency technology to detect minuscule foreign bodies or damage. This enables the fast and reliable identification of contamination in packaged food items, for example.
These and other innovations from Fraunhofer are providing efficient and sustainable applications and developments for the plastics industry and thereby helping to secure its future. Come and experience them at booth SC01, in hall 7.
www.fraunhofer.com