www.industry-asia-pacific.com
10
'19
Written on Modified on
IMA Digital, 24 digital projects for the Smart Factory of the future
IMA Digital, the digital development project launched at Interpack 2017, is two years old.
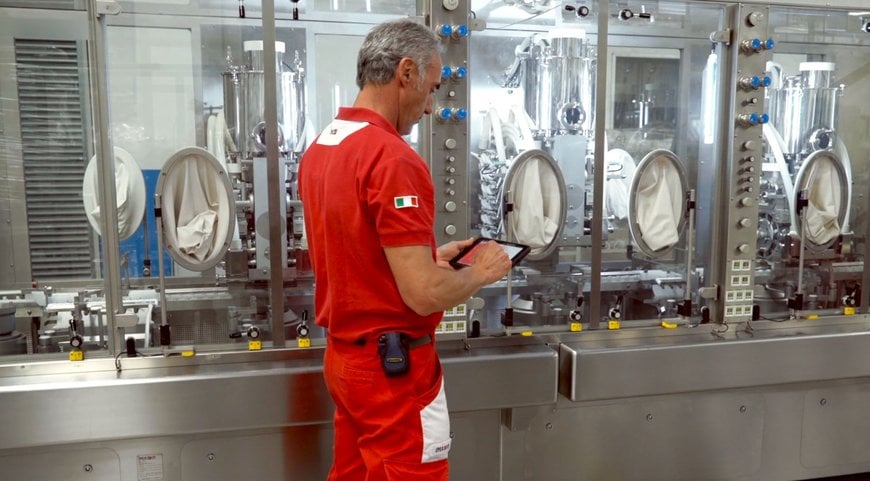
IMA Digital, the project of innovation and consolidation of the Group’s digital strategy, launched at Interpack 2017 in Düsseldorf, is two years old.
Dario Rea, Research and Innovation Group Director introduces the project: “We are happy to have reached this important milestone: two intense and fruitful years of activities aimed at innovation and the digitalization of processes and functions. Today we count on 24 digital development fronts within the IMA Digital project, each with very interesting potential. “
“The core activity behind IMA Digital has seen us involved in the creation of Smart Machines, advanced and technologically connected machines capable of providing data useful for its monitoring. And today we have the opportunity to deliver to our customers connected products and a wide range of services able to increase the effectiveness of use”.
The possibility of obtaining plants and connected machines, explains D. Rea, is only the first step aimed at an ever-increasing optimization of production performance. Through the collection of data from machines and plants it will be possible to have a deeper knowledge of their real operating conditions allowing their better use with consequent reduction of waste.
In addition to the creation of Smart Machines, continues D. Rea “we have opened several fronts related to Artificial Intelligence. The AI is used in various sectors such as quality control and analysis of data from machines.
Another application we have supported is in the Additive Manufacturing through Inkbit, a startup born from the Computer Science and Artificial Intelligence Laboratory of the Cambridge MIT. The company works on a 3D printer that using Machine Learning techniques is able to correct printing errors in real time, guaranteeing the geometry of the finished product”.
Additive manufacturing is not the only area in which AI has found employment in the Group’s plants. In the IMA Digital Project preventive and predictive maintenance relating to the plants find concrete application, explains Pier Luigi Vanti, ICT Group Director: “We are in full rush to realize the codes to combine the connectivity of the systems to predictive and preventive maintenance.
One of the challenges to face and to win is to reach the possibility of foreseeing faults and malfunctions of the systems. Thanks to increasingly precise control logics, the Group has created various actions aimed at achieving results of this type. The potential that opens up is enormous” continues to explain P.L. Vanti.
“Thanks to predictive analysis we are able to reduce machine downtime, proceed with component replacements when necessary, without incurring unexpected problems. This turns into a better product delivery and an increase in production performance”.
Furthermore, the Group has given life to tools that can be supplied to customers and partners, continues to explain Pier Luigi Vanti: “We have created protected Digital Rooms, within which the customer has the possibility to host his own production data to share them with us and get a more in-depth analysis of performance”, with the ultimate goal of improving production flows.
The Digital Rooms are a type of customer support that accompanies other tools on which the Group has paid great attention. Augmented and Virtual Reality, highly functional tools in production, have found space in activities related to training, plant maintenance and flow management.
The Dashboards, platforms where you can view the production data according to aggregate logics and from the customizable structure, are the other great ally that the Group wants to offer to its partners “to make them more and more aware and autonomous in the management of the plants. Obviously these dashboards can be used from a PC, smartphone or tablet. Their versatility and wide range of customization make them the ideal tools to support the customer by guaranteeing the data they really need”.
Ample space within IMA Digital was found in activities aimed at organizing the structure of the Group with a particular focus on the growth of employees’ skills and on the management of projects and programs: “IMA is a real Smart Factory” explains Monica Cervellati, IMA Digital Communication Manager, “within which infrastructures and employees collaborate and work in synergic balance.
But it is the employee who always has priority. Within the IMA Digital Project, under the supervision of Massimo Ferioli, Group Organization Director and IMA Digital coordinator, platforms such as the Human Capital Management (HCM), the platform for monitoring the progress of each individual employee within of the Group” explains M. Ferioli. “The goal is to accompany the employee on his growth path, from entry to exit from the company, and provide him with the skills necessary to contribute to the Group’s success.”
Another platform, says M. Cervellati, created within IMA Digital is the starring of the new Global Intranet, conceived with the aim of facilitating communication between individuals and departments, and equipped with collaboration areas where it is possible to share digital work material.
The implementation of the Digital Business Dashboards, another digital development initiative within the Project, provide managers with a platform to better manage projects and business opportunities.
www.ima.com