www.industry-asia-pacific.com
07
'19
Written on Modified on
Milestone in the development of new material systems
Thanks to their wide range of possible applications, traditional fiber composites are popular materials in manufacturing – despite their relatively high production and disposal costs.
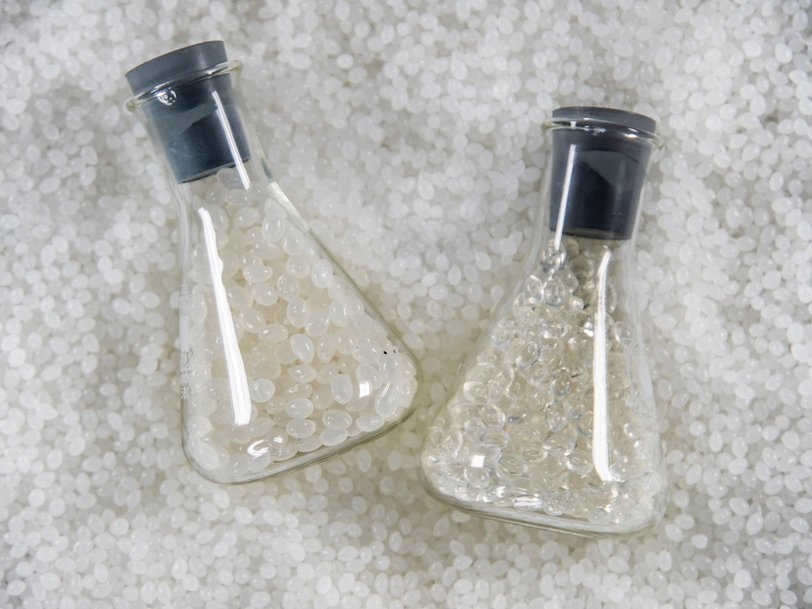
A thermoplastic biopolyester, PLA is based on lactic acids, renewable resources from agricultural waste, or specially cultivated raw materials such as sugarcane. »In this project, we’ve now brought the benefits of PLA to the next application level by fusing two types of PLA to create so-called self-reinforced PLA composites,« says Kevin Moser, project manager at Fraunhofer ICT.
This combines the advantages of PLA and of composite materials. The newly developed PLA composites have high mechanical strength and rigidity while also exhibiting good hydrolysis resistance. Like pure PLA, they are fully bio-based, easy to recycle, ductile and even industrially biodegradable.
It was possible to substantially reduce the manufacturing costs, and the energy demands of PLA production are now approximately half those needed to manufacture petroleum-based plastics such as polypropylene and polycarbonate.
And the energy savings are not the only progress made in the increasingly important area of sustainability. In PLA, the CO2 equivalent per kilogram of material used is half that of products based on fossil fuels, such as polypropylene and polyester. Further-more, recycling PLA composites is very easy, as they are made up of just one material type and the fibers do not have to be separated from the matrix – an issue that makes the recycling of conventional fiber composite materials much trickier.
»Accordingly, these composite materials, which can be manufactured on an industrial scale, represent a milestone in the development of functionalized bio-based material systems with high mechanical strength,« explains Moser. »And they make a substantial contribution to the closed-loop economy, because the composite can also be melted and, using existing manufacturing equipment, reprocessed into a new product for high-quality applications.«
In the manufacture of the composite, two different PLA types with different melting points are combined into a self-reinforced PLA composite material. The higher-melting-point PLA is embedded as a reinforcing fiber in the lower-melting-point matrix. The resulting material rigidity can compete with commercially available self-reinforced polypropylene composites. It is planned to manufacture initial prototypes already later this year.
Aside from Fraunhofer ICT, other partners of the »Bio4self« project, which is funded by the EU’s »H2020« funding program (funding code: 745762), include the Technical University of Denmark, the Belgian textile research institute CENTEXBEL and the Danish firm Comfil. The resource-conserving concept with great application potential also impressed the jury at JEC 2019, Europe’s largest trade fair for composite materials, winning first prize in the Sustainability category.
The material can also be seen at the world's leading industry trade fair for the plastic industry "K" in Düsseldorf - from 16 to 23 October at the Fraunhofer booth SC01 in hall 7.
www.fraunhofer.com