Mitsubishi Electric helps Oliver upgrade existing slicing machine
Better HMI and evolution from PCBs to PLCs pave the way for new market opportunities.
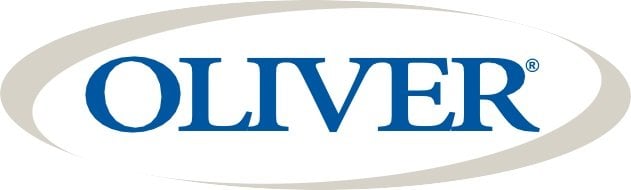
“Mitsubishi Electric HMIs are very responsive… others we tried were so much slower that you would press a button and it would take so long to work you'd be ready to press again. With Mitsubishi, you'd already be cutting.” – Vance Matz, Project Engineer, Oliver Packaging & Equipment Company
Solution
- GT1055-QSBD Operator Interface Screen
- FX3G-14MT/ESS Programmable Logic Controller
OLIVER Product Benefits
- Fast action
- Clear user instructions
- Detailed troubleshooting
Mitsubishi Electric Value-added Advantages
- Responsive HMI screen
- High quality PLCs
- Trusted partner
BACKGROUND
Oliver Packaging & Equipment Company of Grand Rapids, Michigan was founded in 1890 as a wood working equipment manufacturing company specializing in furniture production. During the Depression, the company’s expertise in blade technology prompted them to help create an entirely new industry – and, perhaps, contribute to the coining of the phrase “best thing since sliced bread” – with the introduction of the first retail bread slicing machine in 1932. More than eight decades of innovation later, Oliver offers a diverse line of high quality bread, bagel and bun slicers to retail bakeries, delis, supermarkets, restaurants, and similar establishments, primarily in the U.S. and Canada.
CHALLENGE
Oliver’s Varislicer® 2005 bread slicing machine had been in the company’s product line since about 1990. Relying upon a proprietary printed circuit board (PCB) for control and a scrolling 2x20 character display for user communication, the product, although a common seller in some markets, had some limitations, according to Oliver project engineer Vance Matz. For example, with so little display space and capability for output, stores would often have to put up paper signs that would explain how to use the machines to cut loaves to preferred thicknesses, especially at the self-service bakeries and delis popular in Canada. And, although the machine could theoretically provide on-screen troubleshooting information to repair technicians, the details that were offered could be terse and “kind of cryptic,” leading technicians to opt for diagnostic testing when performing maintenance. So, when in early 2015, Oliver’s PCB supplier discontinued the model of board they were using, the innovative company quickly used the situation as an opportunity to rethink the design of the Varislicer 2005. “We realized that this would be a good application for a programmable logic controller – it could offer our customers so much more functionality,” said Matz.
SOLUTION
Oliver had previously designed equipment using Mitsubishi Electric parts in both their bakery division as well as their sister meal packaging division. Well familiar with Mitsubishi Electric quality and value, they soon spec’d a Mitsubishi Electric human machine interface screen (HMI) and a PLC in their newly redesigned Varislicer 2005.
“The new machine is a total game changer for us – it offers a completely different level of usability than the old one,” said Matz.
Right off the bat, he explained, the Mitsubishi Electric PLC and HMI offer huge flexibility. With a big, easy-to-read screen and large, pressable buttons, machine operation is now almost self-explanatory, even for first time self-serve customers or new bakery employees. Even so, step-by-step instructions can be placed right on the clear, easy to read computer screen – a far cry, he noted, from the image quality of the scrolling dotted messages offered by the old model. Further, technicians are now getting detailed and convenient troubleshooting information right on-screen, so maintenance is much easier as well. And, adding a menu with English, Spanish and French language options was also a breeze – a big benefit for many potential retail customers both in Canada and the U.S.
But, Matz noted, he feels that perhaps Mitsubishi’s most dramatic contribution to the redesign came on the speed side.
“Compared to those offered by any other supplier we looked at, Mitsubishi Electric HMIs are very responsive to the touch and very fast,” he said. “Other HMIs we tried were so much slower that you would press a button and it would take so long to work you’d be ready to press again. With Mitsubishi, you’d already be cutting.”
RESULTS
Matz reports a number of benefits accruing to the company as a result of the redesign of the Varislicer 2005. One is the decrease in the cost of warranty service calls. Since Oliver utilizes a network of local repair contractors near to each retailer who charge them by the hour, time is, literally, money.
“Technicians used to have to do all those time consuming tests to get to the heart of any problem. Now the PLC gives them detailed indicators regarding the status of the sensors, the position of the knife arm, the door and more,” he explained. “They can get in and out of there faster – and that’s good for the retailer, and good for us.”
Also good for Oliver is the additional market opportunities that the redesigned Varislicer 2005 is creating for the company in the United States, where, Matz said, consumers tend to demand more modern, more convenient products than do their counterparts north of the border. In fact, Oliver has recently sold a number of the new Verislicer 2005 machines to a large American supermarket chain and several other customers who had not been very interested in the incumbent version.
“Mitsubishi Electric really helped us raise the bar on this model,” he said.