High-precision measurement on any material or surface
High-precision measurement on any material or surface |
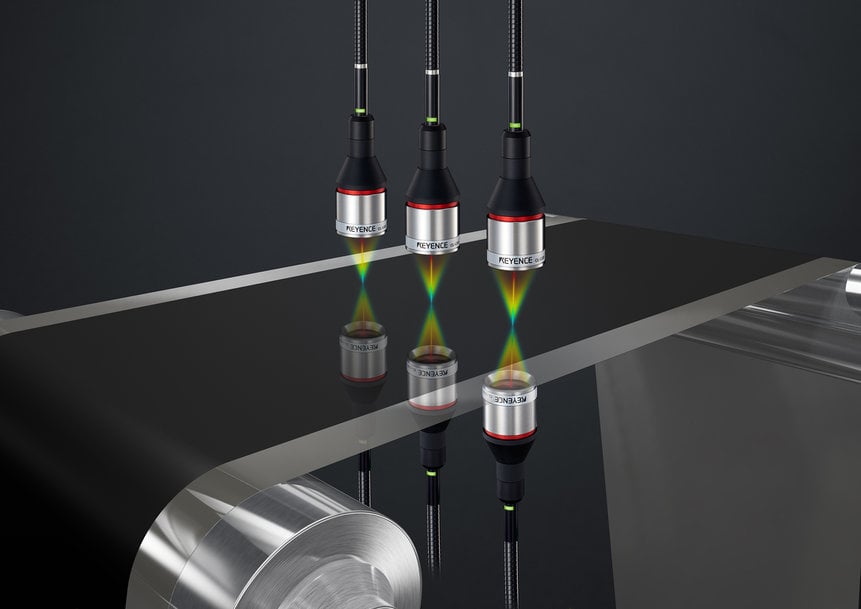
Keyence, a world-leading supplier of industrial inspection solutions, has unveiled its CL-3000 series confocal displacement sensor for high-precision measurement tasks on any material or surface. This ultra-compact coaxial laser displacement sensor addresses manufacturing challenges such as improving quality, preventing the shipment of defective parts and increasing production.
Typical applications for the CL-3000 include metal plate thickness measurement, plate runout measurements, wafer flatness measurement, and sealant and adhesive control, to mention a few. IP67 dust and water-resistance rating allows use in all manufacturing environments.
The multi-colour confocal method allows for performance levels not possible with conventional systems. Multi-coloured light is generated using a light source that emits red and green light simultaneously. The emitted light is more stable and of higher brightness over a wider range of wavelength bands compared with typical white LEDs. This capability ensures there are sufficient light levels at all points in the measurement range, allowing for higher accuracy.
High precision is assured with the CL-3000 (without needing specialized heads) on any material, including glass, wafer, PCB, sealant/adhesive, film/plastics and machined parts. Moreover, all types of surfaces can be measured, such as transparent, translucent, mirrored, curved, oblique, stepped, uneven or rough, with linearity from ±0.2µ. Unlike conventional laser sensors, detection is possible even at a high angle tilt from the target.
Indeed, the Keyence CL-3000 measures stably on targets that cast multiple reflections or absorb light. From rubber to reflective materials, the same set-up is able to measure the surface stably. Even under harsh condition such as oil mist or dust, the rigid design of the sensor and the reinforced robot-ready cable provide reliable results without the need of protective equipment.
The compact sensor heads, including the industry’s smallest at 8mm diameter, can be installed in tight and constrained spaces. Designed with only the lens inside the head, the sensor is reduced to 1/50th the size of conventional systems, thus meeting the growing need for miniaturization in manufacturing equipment.
CL-3000 units are also around 50% lighter than a conventional laser displacement sensor, allowing easy mounting at the end of a robot arm. The lighter weight also reduces residual vibration when the robot arm is brought to a stop.
A standard system increases its temperature by up to 8°C in about 10 minutes causing misalignment and mounting errors. The CL-3000 series on the other hand has no electronic components, just lenses, so measurement errors due to heat generation, electrical noise or optical axis deviations are eliminated.
Importantly, sensor head installation and program setting is simple with the Keyence CL-3000. The adjustable fixture for thickness measurement and the optical axis alignment function included within the PC software make accurate set-up quick and easy.
Five different models are available in the new series (including a compact unit, the size of an average pencil), to suit tasks from simple profile measurement to ultra-high accuracy applications.
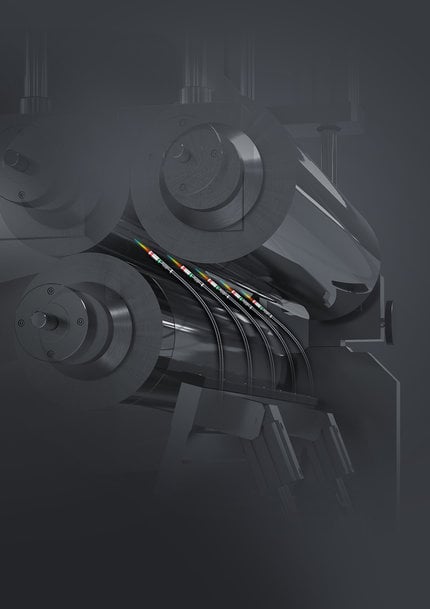
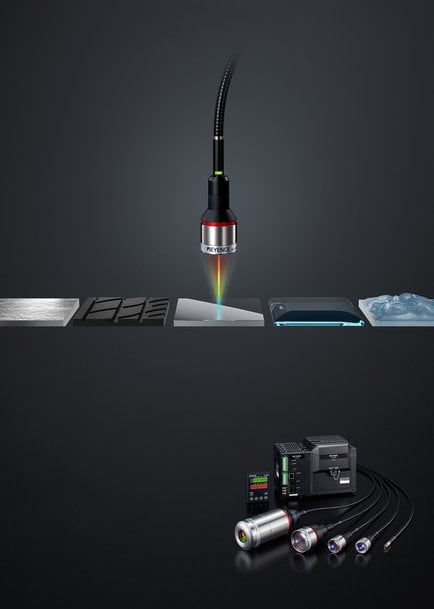