Cold-rolled ball screws at work in the extraction of black gold
Oil is the black gold under the earth’s surface. To reach this precious resource, innovative and extraction technologies are required. Before the fossil fuel reaches us in the form of the familiar end products we use every day, it not only has a history stretching back over millions of years but also has travelled in a long journey. For the last five decades, Eichenberger Gewinde AG’s principal activity has been the design and manufacture of highly accurate and cleverly-designed screw drives. It uses this wealth of experience and technical know-how to support its partners in their process of innovation. Dynamic-mechanical functional elements are highly adaptable, and this means they can contribute significantly to the success of drive technology projects. The Swiss thread specialist is aware of this and makes use of this potential.
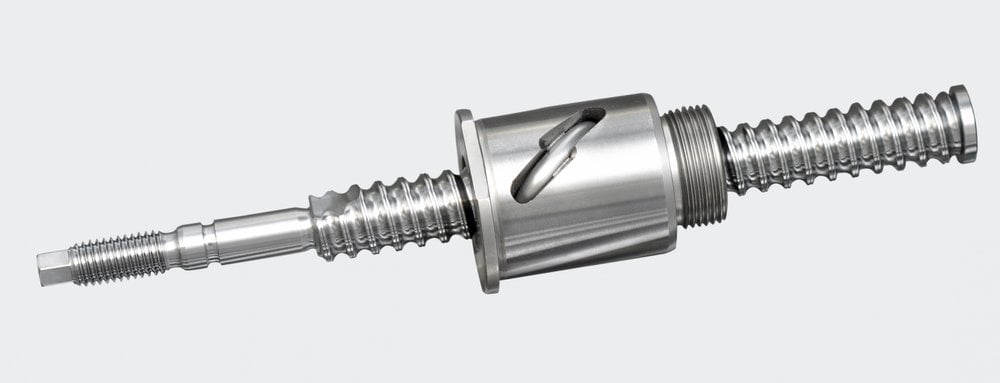
Offshore drilling
In the oil and gas production sector, offshore drilling means extraction from below the sea floor. Offshore drilling implies that sensitive extraction technology will be confronted with adverse climatic conditions. To drill a borehole, solid rock has to be broken up, powerfully, accurately and efficiently. Nowadays, highly intelligent drilling systems are used, which can independently drill down to or through the oil and gas deposits. What is remarkable is not just how the drilling machines operate but also the extreme conditions they work in. Deep under the earth’s surface, temperatures frequently get as hot as the oven we might use at home to bake a pizza. Added to this are static pressures of 500 to 1000 bar (car tyre pressure is usually only 2 bars), violent shocks and vibrations and the aggressive environment in the form of drilling fluids, jagged borehole cuttings, etc. Directional drilling technology allows drilling at different angles. By using extremely complex systems, it is possible to control the direction of the drilling and change it to go in any direction. For example, if an oil deposit is under a city or a nature reserve it is impossible erect a drilling rig directly above. In such cases, the rig has to be installed a few kilometres away and, working from there, drill horizontally and vertically to reach the target.
Robustness, high torque and slow rotation
The kinds of devices used in modern drilling technology exist nowhere else except perhaps in the aerospace industry. “Normal” boreholes are often several kilometres long. In spite of the extremely harsh conditions, the highly complex drilling shaft has to operate flawlessly. Not only does it have to drill quickly and efficiently but it also has to be extremely reliable. If a drilling assembly gets jammed, this results in enormous costs. As part of the steering system, the robust Carry-type ball screw drive (BSD) performs the demanding task of steering the high-tech drilling arms. A high torque is required at slow rotation. The BSD from Burg, Switzerland handles the daring vertical and horizontal drilling operations, working with speed and precision. Oil and gas extraction is very hard on mechanical components. Carry’s high mechanical load capacity, the high transmission ratios and highly efficient, low-dissipation energy transfer really come into play.
Carry packs plenty of power
The requirements specification for the drilling unit steering application placed extremely exacting demands in terms of the static and dynamic load ratings, rotation speed, torque, dimensions and the surrounding geometry. The challenge was to find the perfect ball screw and to adapt the shape of the nut to the specific requirements. Because of its efficiency ratio of over 0.9 and the associated energy efficiency, the Carry BSD provided the perfect solution. The tube-type ball return made of heat-resistant steel was one of the key features which influenced the decision in favour of using the Carry BSD in the application. A sophisticated process is used to bend and machine the ball return before it is integrated into the nut. The tube return reinforces the robustness and load capacity of the Carry BSD. The optimal solution for lubrication at high temperature levels and strong pressure was found by working together with a grease manufacturer.
The special lubricant has proven up to the job. Heat, cold, corrosion, dust, chemicals and salt water have no effect on it.
Cold forming lays down the ideal conditions
What makes the Carry BSD so resilient and the ideal component for its function in the application? The thread rolling generates very exact geometries and a high surface quality. The usual thread machining methods such as milling, turning or whirling, work by removing some of the solid material. These methods have the disadvantage that they cut through the longitudinal fibres of the steel. In contrast, thread rolling, which machines them without chipping away the metal, does not cut the fibres, it only deflects them. Depending on the material this results in an increase in rigidity of 30 to 50 %. The surface in the profile is also strengthened at the same time. This smoothly rolled surface offers few opportunities for contamination. This is crucial for obtaining a long service life. Furthermore, thread-rolling also produces very good roughness values (~ Rz 1.0) at the edges of the thread and in the base radius which lead to significantly reduced susceptibility to indentation.
A constant search for performance excellence
With years of experience of induction hardening in-house, Eichenberger, the thread rolling specialist, has also acquired considerable know-how in this field. Whereas hardening shops are dedicated exclusively to steel hardening, Eichenberger strives to obtain the best possible combination of hardness and accuracy. Although this may sound easy, it is only possible with a team working very closely together. Closeness to the customer and sensing the customers’ needs are basic requirements. Thanks to Eichenberger’s advanced machine park, the most modern production methods, and because development, manufacturing and quality assurance at Eichenberger are grouped under one roof, prototypes can be manufactured extremely quickly. The way is then clear for the next phase: production maturity. When the inventor of the product is also its most economic manufacturer, this can be a recipe for success.