www.industry-asia-pacific.com
12
'18
Written on Modified on
faigle provides components made of highperformance plastic for shuttle systems. Very quiet running meets high load capacity
In many cases, high performance plastics meet the demands regarding resistance and fatigue properties for components better than metal. faigle applies its application expertise and wellengineered design to develop a new generation of wheels for shuttle systems.
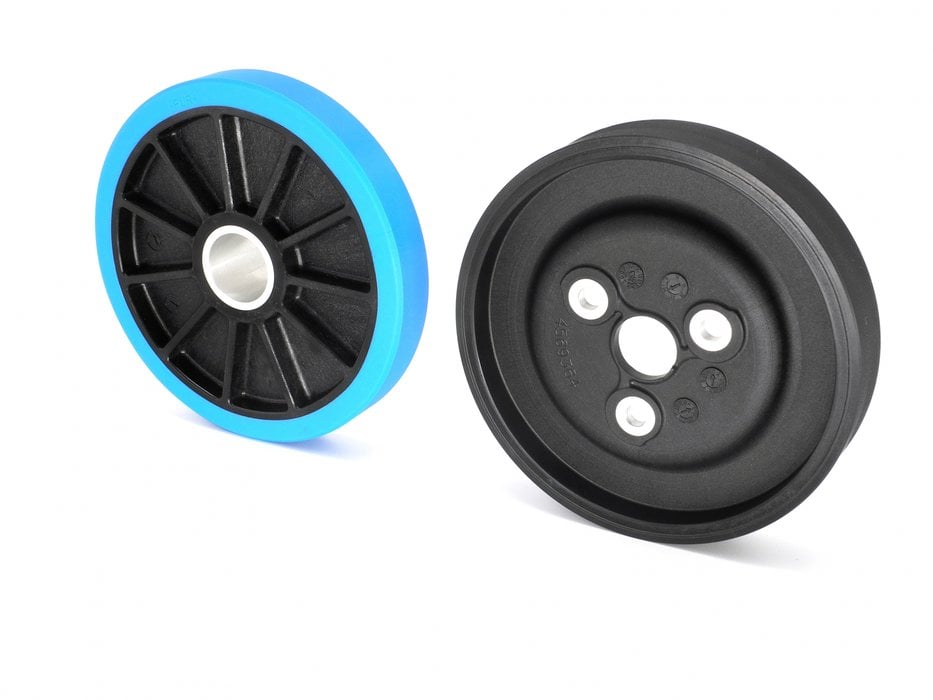
Vibrations in highbay warehouse aisles pose a challenge for the safe handling of goods in shuttle systems. These are caused by poor wheel concentricity or impacts in the rails. Goods in the bays may also slip to such an extent that the telescopic arms can no longer grab them. If this happens, the system needs to be switched off and the goods retrieved manually. Plastic wheels minimise this type of vibration.
Wheels from faigle: Plastic instead of metal
In the past, shuttle wheels were usually made of a metallic hub and a pressureless cast tyre made of polyurethane. faigle produces shuttle wheels completely of thermoplastic. They consist of a soft, thickwalled tyre and resilient hub. This provides them with excellent damping and very quiet running properties. They can even cope with the dynamic starts and abrupt stops which are typical of shuttle systems. This is the best way to avoid vibrations in highbay aisles.
faigle wheels are produced in an injectionmoulding process which provides excellent bonding between the tyre and the hub. There is no need for additives such as primers and this increases process reliability in production. Another benefit is that shuttle wheels pro-duced completely from plastic are much lighter than models with a metallic hub. The lower weight requires less drive force and reduces unsprung mass.
Low flattening and reliable bonding
If the shuttle system is at standstill for longer periods of time, such as at weekends, soft tyres tend to flatten. This is called flattening and causes considerable vibration when the system is re-started. faigle wheels have a soft tyre but nonetheless don’t flatten and ensure very quiet running. This is attributable to the use of special materials and reduced compression set which considerably reduce flattening.
Wheels need to reliably transfer drive and brake force to the rails. One condition here is good grip between the wheel and the rail. Despite this, wheels are prone to a certain amount of slippage which may lead to abrasion that is deposited on the rails, causing vibration. The thermoplastic material used by faigle is extremely resistant to wear and prevents deposits on the rails.
High production volumes, custommade products
Shuttle systems are becoming more widespread in companies which have high warehouse turnover, a large number of orders and low order volumes. The demand for wheels has risen considerably due to the trend in automatic storage and retrieval systems. Manufacturing wheels using the injection moulding process allows the rapid and economical production of high volumes.
faigle, the thermoplastics specialist, also implements custom solutions. For example, economical mould inserts in master moulds specially developed for shuttle wheels with diameters ranging from 80 to 150 mm. This minimises the initial costs for the customer for implementing an injectionmoulding solution.
Plastic for shuttle flaps
The use of high performance plastics is also ideal for other shuttle system components, such as the highly stressed shuttle flaps on telescopic arms. These are normally made of aluminium or steel, and are mounted in pivot bearings and fitted with a rotary drive coupling. As a result, shuttle flaps are complex milled parts.
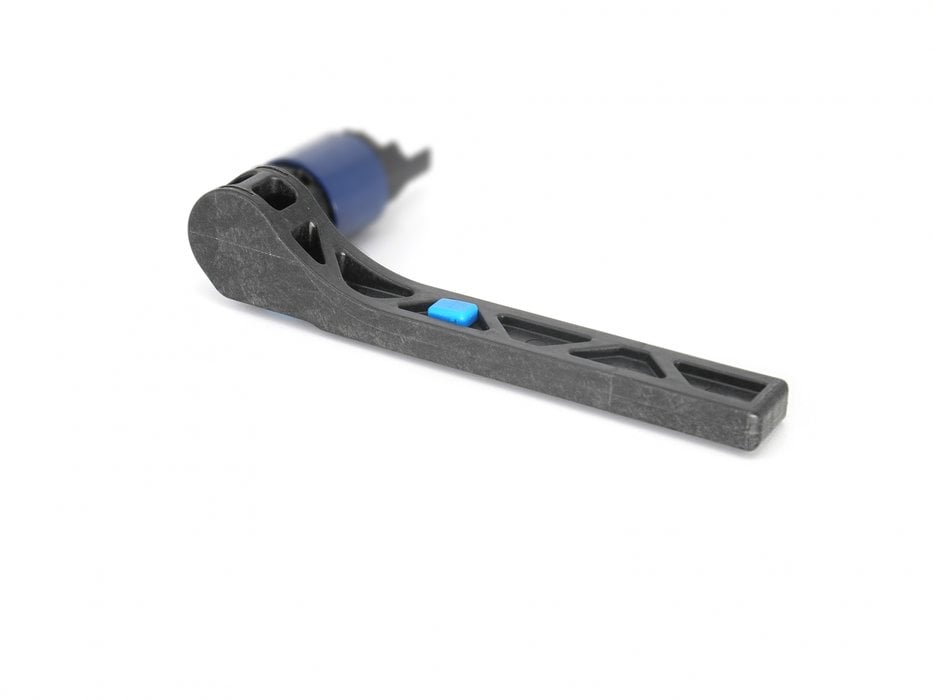
faigle uses fibrereinforced high performance plastics in the production of shuttle flaps, which are lightweight and can also be manufactured economically, even in complex geometries. This is possible since faigle is a plastics specialist with many years of experience and know-how in the design of geometries using FEM and injectionmoulding processes. At the same time, plastic flaps can meet the extremely high requirements regarding load capacity and durability much better than components made of metal.
Telescopic arms in shuttle systems must be linearly guided during advance and retraction operations. Sliding elements from faigle made of PAS-LXY have a low friction coefficient, which prevents the stickslip effect, allowing telescopic arms to slide without jerking. The sliding elements are maintenancefree and require no lubrication. In addition, the sliding elements and their mating components are extremely wearresistant.
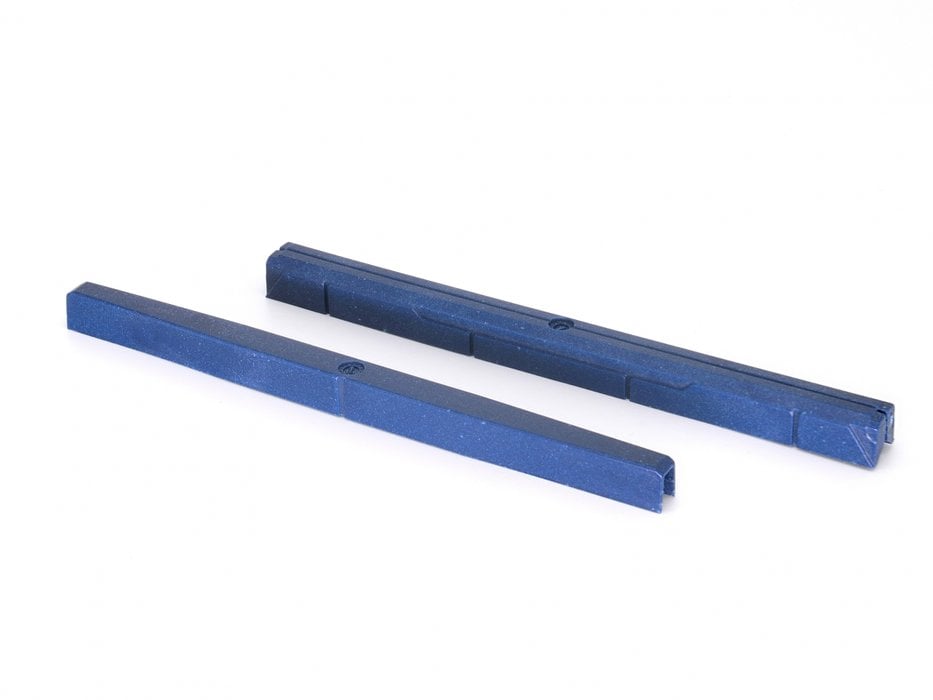
Image: Sliding elements for faigle shuttle telescope arms are made of PAS-LXY thermoplastic material. They are maintenancefree, require no lubrication and minimise wear, also on their mating components. (source: faigle Kunststoffe GmbH)
faigle Kunststoffe GmbH
Manuela Boss-Herburger
Landstr. 31
A-6971 Hard
Tel +43 (0) 5574/68 11-1605
Fax +43 (0) 5574/68 11-1809
This email address is being protected from spambots. You need JavaScript enabled to view it.
www.faigle.com