www.industry-asia-pacific.com
13
'19
Written on Modified on
Boggled by Toggle Clamps?
Although widely available and suitable for many applications, toggle clamps are often neglected and aren’t first to mind for design engineers. Paul Mulvey, Sales Manager at norelem UK, explains best practice uses for toggle clamps and how they benefit users.
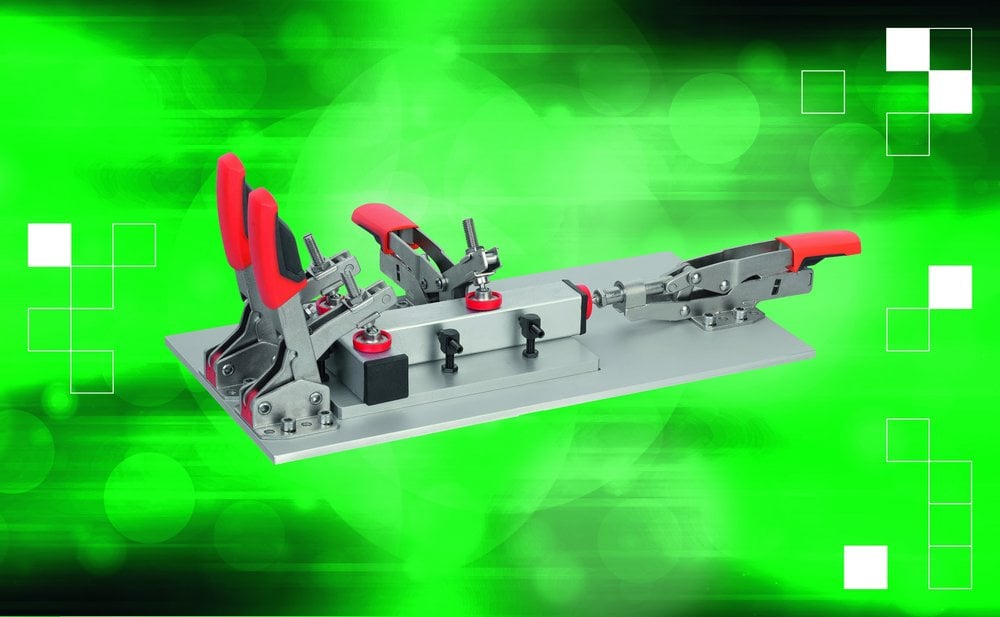
However, much like one size does not fit all, one clamp does not work for all applications. Yet, we can often fall into the trap of using clamps we know well and trust.
It’s only natural of course; after all, isn’t the saying that we are creatures of habit? However, by falling into this routine, efficiencies can be lost, the method of clamping may not be the most optimum choice, and hazards can be introduced.
For example, some clamps were found wanting in one of the biggest engineering projects of recent times across in Canada. Known as ‘The Big Lift’, the Angus Macdonald Bridge in Halifax had to be lifted, and road had to be replaced.
During the project, a near-miss accident happened. When workers went to remove a clamp, one sprang off and landed on the deck because it was load-bound. Although nobody was hurt, the whole project had to be stalled until an optimum safety solution was found.
This is of course a high-profile engineering project with many factors and complexities, but the notion remains – the wrong clamp choice can be harmful to work, and to life.
This is where toggle clamps come in. Although they come in many guises and forms that suit a variety of applications, they aren’t the most widely known or used clamps in the engineering industry. Here’s why you should give them due consideration.
High Clamping Force with Little Expenditure
Toggle clamps offer some of the highest clamping forces available. They work according to the knee-lever principle and can be operated with very little expenditure of force.
This principle works by pressing the ‘knee’ joint of the lever to secure the object in question. Once the three points of the joint are in a line (where the ‘knee’ is straightened and locked), it is no longer possible for the object to be pressed back by a counterforce.
Self-locking is guaranteed when the dead centre position (alignment of the three joints) is exceeded, while the clamping force can be adjusted by setting the thrust screw accordingly.
Toggle clamps are an optimal clamping solution in drilling, welding, grinding and inspection fixtures. For the timber industry, they have saved timber from extreme deformations when bonding or assembling fragile sheets, as the clamping force is controllable.
No Ambiguity
Toggle clamps operate in a set way. They are positioned before clamping, and then the toggle is pulled down to lock the object. The clamping force is already pre-set based on the thrust screw within the clamp. Therefore, the clamping force is guaranteed.
This contrasts greatly with other clamping methods, such as G-Clamps. G-Clamps work on compression and are tightened by hand like a vice.
Of course, these types of clamps introduce a human element, where it depends upon each person’s own perception of tightness as well as strength. What one person thinks is tight, may not be tight enough for someone else. It may even be too loose, which can cause potential accidents.
Compression-based clamps may also become difficult to loosen if overtightened, and thus introduces inefficiencies. Overtightening can also mark the workpiece.
Versatile, Ergonomical, Self-Adjusting
One of the key attributes of toggle clamps is their versatility. In norelem’s range, they can be supplied to lock vertically, horizontally, on angles, and in large and small. They can even come with push-pull operations for bracket mounting.
This all means that toggle clamps can be used for practically any day-to-day clamping application. What’s more, the handles can be supplied with ergonomic grips. This eases the potential of repetitive strain injuries on operators, particularly if they are working on high-volume parts and machining.
Another benefit of toggle clamps is that they can be self-adjusting, such as those in the norelem range. These toggle clamps adjust automatically to the height, width or depth of the workpiece, and have an infinite adjustable clamping position within 35mm, without having to reset the thrust screw. The clamping force can be adjusted up to 1,000 newtons using a set screw under the lever in the hinge, so the workpiece is still as secure as required.
Self-adjusting toggle clamps are recommended for use when operators are working on high-volume machining or milling, but the workpieces are of varying sizes. This saves on having to manually reset the clamp and adjust the thrust screw.
Toggling with Engineering Efficiencies
Two of the most basic principles of engineering is to solve problems, and to ‘keep it simple’. Toggle clamps achieve both when considered in the right way.
For design engineers, think about when toggle clamps could be a more effective, simpler clamping solution. Instead of using multiple g-clamps, can a single toggle clamp be used instead?
In this respect, not only can toggle clamps be a potentially better solution, but they can reduce costs too. Less capital expenditure on clamps, less injuries and strains, and a more efficient workforce mean better production and profit overall.
For more about norelem UK and toggle clamps, please visit www.norelem.co.uk.