www.industry-asia-pacific.com
11
'24
Written on Modified on
SUSTAINABILITY IN THE MANUFACTURING SECTOR
While the term "sustainability in manufacturing" may have gained popularity as a buzzword, its underlying principles and significance are substantial, writes K.A. Gerardino.
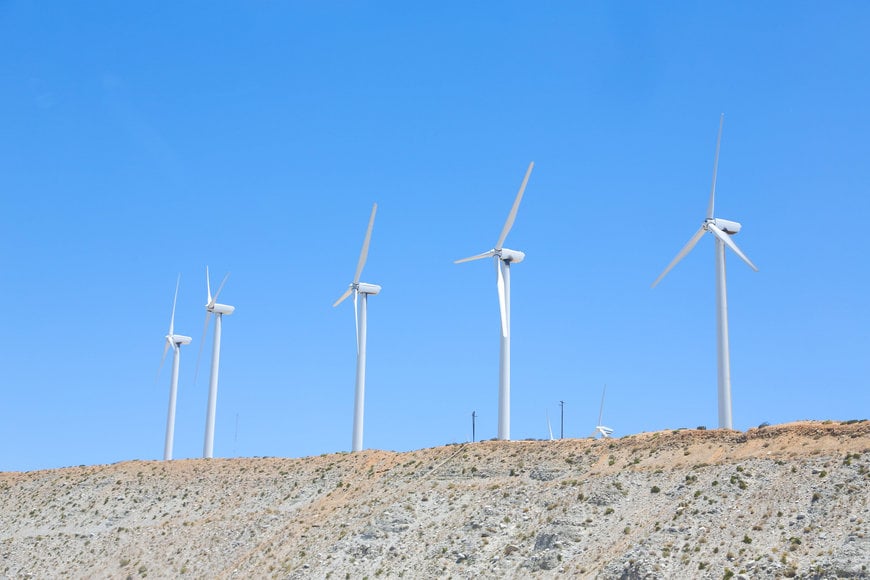
"Sustainability in manufacturing" refers to the practice of producing goods in a way that minimizes negative environmental impacts, conserves resources, and considers social and economic aspects. While some might perceive it as a trendy term, it embodies a crucial shift toward responsible production methods that are environmentally friendly, socially conscious, and economically viable.
In recent years, there has been a significant increase in the focus on sustainability in manufacturing, driven by a greater awareness of climate change, resource depletion, and the need for social responsibility. It is not just a fleeting trend, but a necessary response to the global challenges we face. Many companies and industries are now incorporating sustainable practices into their core operations, aiming to reduce their environmental impact and make positive contributions to society. While the term "sustainability in manufacturing" may have gained popularity as a buzzword, its underlying principles and significance are substantial. It reflects a growing commitment to conducting business in a responsible and sustainable manner.
Industry experts predict that in 2024, manufacturers will allocate a greater amount of time and resources towards sustainability initiatives. Additionally, they are expected to expedite the implementation of intelligent technologies, ranging from artificial intelligence to traceability tools. The rise of smart technology will also be influenced by partnerships and collaborative efforts within the industry.
Sustainability in the manufacturing sector in 2024 is likely to be influenced by several factors, such as:
- The expected mandate of ESG reporting by the US Security and Exchange Commission (SEC), which will require public companies to disclose their greenhouse gas emissions and other environmental, social, and governance metrics.
- The continued growth of renewable power capacity and electrification, which will reduce the operational carbon emissions of products and buildings, and increase the importance of addressing embodied carbon emissions in the production phase.
- The availability of incentives and subsidies for green products and technologies, such as electric vehicles, batteries, clean energy components, and semiconductors, which will spur investment and innovation in sustainable manufacturing.
- The demand for data-driven product decisions that optimize both cost and carbon, and enable manufacturers to assess the carbon impact of different design and manufacturing choices.
The need for a resilient and agile supply chain that can mitigate the risks of disruptions, tariffs, and regulations, and leverage digital technologies and innovation to achieve sustainability goals. These factors suggest that sustainability in the manufacturing sector in 2024 will be a key driver of competitiveness, profitability, and resilience for manufacturers.
Harnessing Digital Technology and Sustainable Energy Sources
At present, manufacturing operations consume approximately 33% of the global energy supply. Even in industries with lower energy requirements, such as chemicals, refining, and paper, energy expenses remain substantial. Moreover, with the continuous escalation of global energy prices, these costs are expected to further escalate. By integrating sustainable practices into their operations, manufacturers can address their primary sustainability challenge and simultaneously strive to reduce their environmental footprint and preserve valuable resources.
Manufacturers may already be at an advantage in their sustainability efforts thanks to the utilization of digital technology. Over the past few years, the adoption of digital capabilities in implementing lean processes has resulted in increased productivity, enhanced workplace safety, and decreased expenses. Additionally, this automation through digital technology offers manufacturers a valuable opportunity to gain deeper insights into their production processes, equipment deterioration, and most importantly, energy consumption. Equipped with this valuable data, organizations can optimize their production methods and enhance predictive maintenance practices to minimize energy usage, as well as decrease material and water wastage. These factors play a crucial role in establishing and promoting sustainability within the industry.
However, that might not suffice. Enhancing the sustainability of the factory floor should also entail a higher utilization of renewable energy, which is now becoming more cost-effective. There are several approaches to achieve this. Numerous manufacturers are capitalizing on power purchasing agreements, which enable them to secure fixed prices for a steady supply of renewable energy, often spanning over 15 or 20 years. Alternatively, manufacturers with extensive campuses are even venturing into on-site generation by employing solar panels, wind turbines, and geothermal pumps to power their facilities.
By implementing waste reduction strategies, optimizing water usage, managing energy loads, and harnessing renewable resources, the factories of tomorrow possess the capability to achieve tangible sustainability results while also cutting down on expenses. This becomes especially crucial as regulatory bodies are progressively enforcing energy efficiency enhancements during the commencement of manufacturing operations or during subsequent operational evaluations.
Adopting Sustainability Practices
The transition towards low-carbon manufacturing and industrial systems is expected to bring about changes across all sectors and stages of the value chain. Although this may seem daunting at first, manufacturers can implement measures within their organizations and factory floors to facilitate the shift towards sustainability. These actions can be undertaken while adhering to the conventional principles of change management.
It is crucial to begin by assessing the current carbon profile of your facilities in order to establish a foundation for your environmental impact. This assessment will help shape your strategy and allow you to establish specific goals and priorities. Given the unpredictable nature of decarbonization and the uncertainty surrounding the achievement of reduction targets, it is essential to incorporate robust scenario planning into your strategy. Furthermore, companies should be ready for their data to undergo audits, providing evidence to clients regarding their sustainability levels.
To implement sustainability initiatives, it may be necessary to establish new positions, such as a chief sustainability officer. These individuals can play a crucial role in identifying the sustainability metrics that the company must meet and deciding on investment priorities. Additionally, they can facilitate the development of any necessary new capabilities. Equally important, in order to effectively execute these priorities, manufacturers will likely need to collaborate with ecosystem partners, including industry associations, third-party providers, and regulators. This coordinated effort will require all participants to enhance their commitment to sustainability.
Reflecting on the matter, manufacturers possess the ability to go beyond mere measurement of their sustainability endeavours. In addition, they have the opportunity to leverage this progress in order to construct a compelling market narrative that highlights the positive effects they are generating. By doing so, they can effectively communicate their commitment to sustainability to both investors and consumers, while simultaneously enhancing transparency. It is crucial for manufacturers who prioritize sustainability to proactively disseminate this information, as those who fall behind in sustainable practices may face a shift in public opinion against them.
Challenges in Achieving Sustainable Manufacturing
Sustainable manufacturing, while critical for addressing environmental concerns, faces several challenges that companies and industries need to overcome:
Costs and Investments: Implementing sustainable practices often requires significant upfront investments in technology, equipment, and processes. While these investments can yield long-term savings, initial costs may deter some companies, especially smaller ones, from adopting sustainable manufacturing methods.
Complex Supply Chains: Global supply chains can be intricate and challenging to manage sustainably. Ensuring ethical sourcing, reducing transportation emissions, and maintaining sustainability standards across suppliers pose difficulties, especially when suppliers are located in various regions with different regulations and practices.
Balancing Profitability and Sustainability: There can sometimes be a perceived conflict between profitability and sustainability. Companies might struggle to balance the need for profit margins and meeting sustainability goals, leading to compromises in sustainable practices for short-term gains.
Technological Limitations and Infrastructure: In some cases, the technology required for sustainable manufacturing may still be in the developmental stage or not widely available. Additionally, regions lacking infrastructure, such as access to renewable energy sources or recycling facilities, can hinder sustainable manufacturing efforts.
Consumer Demand and Education: Lack of consumer awareness or demand for sustainable products can deter companies from investing in sustainable practices. Educating consumers about the importance of sustainability and changing purchasing behaviours is crucial for encouraging companies to prioritize eco-friendly manufacturing.
Regulatory Compliance and Standards: While regulations often drive sustainability efforts, navigating complex and evolving regulatory landscapes across different regions or countries can be challenging for businesses. Adhering to varying standards and ensuring compliance adds complexity to sustainable manufacturing practices.
Measuring and Reporting Impact: Accurately measuring the environmental impact and sustainability of manufacturing processes can be complex. Developing standardized metrics and reporting methods to quantify and communicate sustainability efforts effectively is an ongoing challenge.
Innovation and Research: Continuous innovation is essential for sustainable manufacturing. Research and development to find new, more sustainable materials, processes, and technologies require ongoing investment and commitment to stay ahead in sustainability efforts.
Addressing these challenges involves collaboration among businesses, governments, consumers, and other stakeholders to create a supportive ecosystem for sustainable manufacturing. Overcoming these obstacles will require concerted efforts, innovative solutions, and a collective commitment to prioritize sustainability in manufacturing practices.
Catalyzing Sustainable Manufacturing
Overcoming challenges in sustainable manufacturing requires a multi-faceted approach involving various stakeholders, innovative strategies, and concerted efforts. Here are some ways to address these challenges:
Invest in Research and Development: Encourage investment in R&D to develop and improve sustainable technologies, materials, and processes. This can lead to innovations that reduce costs, enhance efficiency, and minimize environmental impact.
Collaboration and Partnerships: Foster collaboration among industry players, governments, academia, and NGOs to share knowledge, best practices, and resources. Collaborative initiatives can drive advancements in sustainable manufacturing.
Education and Awareness: Increase awareness among consumers, businesses, and policymakers about the benefits of sustainable manufacturing. Education programs and campaigns can influence consumer behaviour and encourage demand for eco-friendly products.
Regulatory Support and Incentives: Governments can offer incentives, tax breaks, or subsidies to businesses adopting sustainable practices. Strengthening regulations and setting clear standards for sustainability can also drive industry-wide improvements.
Supply Chain Transparency and Engagement: Encourage transparency across the supply chain by working closely with suppliers to ensure ethical sourcing, reduced emissions, and adherence to sustainability standards. Engaging suppliers in sustainability initiatives can have a cascading effect on the entire manufacturing process.
Lifecycle Thinking and Design: Incorporate sustainability considerations from the product design phase itself. Develop products that are durable, recyclable, or biodegradable, and consider the entire lifecycle impact, including raw material extraction, manufacturing, distribution, use, and disposal.
Investment in Infrastructure: Build necessary infrastructure for sustainable practices, such as renewable energy sources, recycling facilities, and efficient transportation networks. Infrastructure development supports the adoption of eco-friendly manufacturing processes.
Standardization and Metrics: Develop standardized metrics and reporting frameworks to measure and communicate sustainability efforts effectively. This facilitates comparison, benchmarking, and better decision-making across industries.
Continuous Improvement and Adaptation: Embrace a culture of continuous improvement by regularly reviewing and updating sustainability strategies. Adapt to new technologies, market demands, and regulatory changes to stay ahead in sustainable manufacturing.
Consumer Engagement and Responsiveness: Engage with consumers through transparent communication about sustainability efforts. Respond to changing consumer preferences and behaviours by offering eco-friendly products and services.
By employing these strategies and promoting a holistic approach to sustainability, businesses can navigate challenges in sustainable manufacturing and make significant strides towards creating a more environmentally friendly and socially responsible industry.
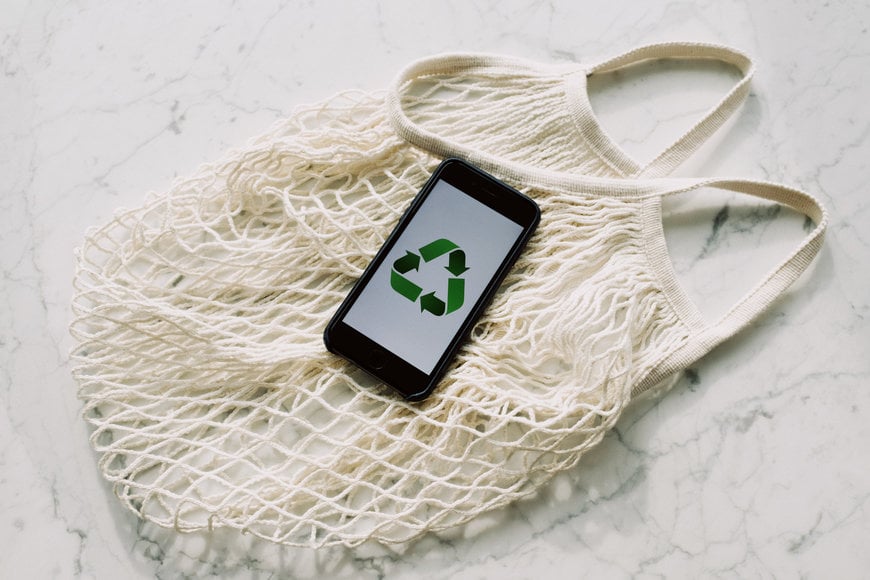
Leading Manufacturers Prioritizing Sustainability
Companies that practice sustainable manufacturing are those that prioritize reducing their environmental impact, while maintaining economic viability and social responsibility. Here is a compilation of companies that engage in sustainable manufacturing across various industries such as transportation, food and beverage, fashion, and more. These companies prioritize minimizing their environmental footprint while ensuring economic sustainability and social responsibility.
Unilever's focus on sustainability covers its products, supply chain, partners, and global governance – and, with a staggering 3.4 billion people globally using Unilever’s 400-plus brand names every day, the impact that such brand corporations can have is crucial. The company is pushing towards zero emissions in its operations by 2030, and net zero emissions across its value chain by 2039, alongside finding new low-carbon ingredients, expanding its plant-based product range and developing fossil-fuel-free cleaning and laundry products.
Vestas, a renowned Danish wind turbine manufacturer, is at the forefront of sustainable energy solutions worldwide. Recognized as the second most sustainable company globally according to The Corporate Knights Index, Vestas is committed to achieving carbon neutrality by 2030 without relying on carbon offsets. Additionally, the company aims to manufacture wind turbines that generate zero waste by 2040. Not only is Vestas a leader in sustainability, but it also pioneers global energy advancements. In a groundbreaking initiative, Vestas successfully saved 9.3 tonnes of emissions during the pilot program of the world's first hydrogen-powered offshore service vessel, surpassing traditional vessels in terms of environmental impact reduction.
Nestlé, the world's largest food and beverage company, firmly believes in the transformative power of food to improve the quality of life for all individuals, both in the present and for future generations. In pursuit of its objectives, Nestlé has set forth several ambitious goals, including:
Harnessing Digital Technology and Sustainable Energy Sources
At present, manufacturing operations consume approximately 33% of the global energy supply. Even in industries with lower energy requirements, such as chemicals, refining, and paper, energy expenses remain substantial. Moreover, with the continuous escalation of global energy prices, these costs are expected to further escalate. By integrating sustainable practices into their operations, manufacturers can address their primary sustainability challenge and simultaneously strive to reduce their environmental footprint and preserve valuable resources.
Manufacturers may already be at an advantage in their sustainability efforts thanks to the utilization of digital technology. Over the past few years, the adoption of digital capabilities in implementing lean processes has resulted in increased productivity, enhanced workplace safety, and decreased expenses. Additionally, this automation through digital technology offers manufacturers a valuable opportunity to gain deeper insights into their production processes, equipment deterioration, and most importantly, energy consumption. Equipped with this valuable data, organizations can optimize their production methods and enhance predictive maintenance practices to minimize energy usage, as well as decrease material and water wastage. These factors play a crucial role in establishing and promoting sustainability within the industry.
However, that might not suffice. Enhancing the sustainability of the factory floor should also entail a higher utilization of renewable energy, which is now becoming more cost-effective. There are several approaches to achieve this. Numerous manufacturers are capitalizing on power purchasing agreements, which enable them to secure fixed prices for a steady supply of renewable energy, often spanning over 15 or 20 years. Alternatively, manufacturers with extensive campuses are even venturing into on-site generation by employing solar panels, wind turbines, and geothermal pumps to power their facilities.
By implementing waste reduction strategies, optimizing water usage, managing energy loads, and harnessing renewable resources, the factories of tomorrow possess the capability to achieve tangible sustainability results while also cutting down on expenses. This becomes especially crucial as regulatory bodies are progressively enforcing energy efficiency enhancements during the commencement of manufacturing operations or during subsequent operational evaluations.
Adopting Sustainability Practices
The transition towards low-carbon manufacturing and industrial systems is expected to bring about changes across all sectors and stages of the value chain. Although this may seem daunting at first, manufacturers can implement measures within their organizations and factory floors to facilitate the shift towards sustainability. These actions can be undertaken while adhering to the conventional principles of change management.
It is crucial to begin by assessing the current carbon profile of your facilities in order to establish a foundation for your environmental impact. This assessment will help shape your strategy and allow you to establish specific goals and priorities. Given the unpredictable nature of decarbonization and the uncertainty surrounding the achievement of reduction targets, it is essential to incorporate robust scenario planning into your strategy. Furthermore, companies should be ready for their data to undergo audits, providing evidence to clients regarding their sustainability levels.
To implement sustainability initiatives, it may be necessary to establish new positions, such as a chief sustainability officer. These individuals can play a crucial role in identifying the sustainability metrics that the company must meet and deciding on investment priorities. Additionally, they can facilitate the development of any necessary new capabilities. Equally important, in order to effectively execute these priorities, manufacturers will likely need to collaborate with ecosystem partners, including industry associations, third-party providers, and regulators. This coordinated effort will require all participants to enhance their commitment to sustainability.
Reflecting on the matter, manufacturers possess the ability to go beyond mere measurement of their sustainability endeavours. In addition, they have the opportunity to leverage this progress in order to construct a compelling market narrative that highlights the positive effects they are generating. By doing so, they can effectively communicate their commitment to sustainability to both investors and consumers, while simultaneously enhancing transparency. It is crucial for manufacturers who prioritize sustainability to proactively disseminate this information, as those who fall behind in sustainable practices may face a shift in public opinion against them.
Challenges in Achieving Sustainable Manufacturing
Sustainable manufacturing, while critical for addressing environmental concerns, faces several challenges that companies and industries need to overcome:
Costs and Investments: Implementing sustainable practices often requires significant upfront investments in technology, equipment, and processes. While these investments can yield long-term savings, initial costs may deter some companies, especially smaller ones, from adopting sustainable manufacturing methods.
Complex Supply Chains: Global supply chains can be intricate and challenging to manage sustainably. Ensuring ethical sourcing, reducing transportation emissions, and maintaining sustainability standards across suppliers pose difficulties, especially when suppliers are located in various regions with different regulations and practices.
Balancing Profitability and Sustainability: There can sometimes be a perceived conflict between profitability and sustainability. Companies might struggle to balance the need for profit margins and meeting sustainability goals, leading to compromises in sustainable practices for short-term gains.
Technological Limitations and Infrastructure: In some cases, the technology required for sustainable manufacturing may still be in the developmental stage or not widely available. Additionally, regions lacking infrastructure, such as access to renewable energy sources or recycling facilities, can hinder sustainable manufacturing efforts.
Consumer Demand and Education: Lack of consumer awareness or demand for sustainable products can deter companies from investing in sustainable practices. Educating consumers about the importance of sustainability and changing purchasing behaviours is crucial for encouraging companies to prioritize eco-friendly manufacturing.
Regulatory Compliance and Standards: While regulations often drive sustainability efforts, navigating complex and evolving regulatory landscapes across different regions or countries can be challenging for businesses. Adhering to varying standards and ensuring compliance adds complexity to sustainable manufacturing practices.
Measuring and Reporting Impact: Accurately measuring the environmental impact and sustainability of manufacturing processes can be complex. Developing standardized metrics and reporting methods to quantify and communicate sustainability efforts effectively is an ongoing challenge.
Innovation and Research: Continuous innovation is essential for sustainable manufacturing. Research and development to find new, more sustainable materials, processes, and technologies require ongoing investment and commitment to stay ahead in sustainability efforts.
Addressing these challenges involves collaboration among businesses, governments, consumers, and other stakeholders to create a supportive ecosystem for sustainable manufacturing. Overcoming these obstacles will require concerted efforts, innovative solutions, and a collective commitment to prioritize sustainability in manufacturing practices.
Catalyzing Sustainable Manufacturing
Overcoming challenges in sustainable manufacturing requires a multi-faceted approach involving various stakeholders, innovative strategies, and concerted efforts. Here are some ways to address these challenges:
Invest in Research and Development: Encourage investment in R&D to develop and improve sustainable technologies, materials, and processes. This can lead to innovations that reduce costs, enhance efficiency, and minimize environmental impact.
Collaboration and Partnerships: Foster collaboration among industry players, governments, academia, and NGOs to share knowledge, best practices, and resources. Collaborative initiatives can drive advancements in sustainable manufacturing.
Education and Awareness: Increase awareness among consumers, businesses, and policymakers about the benefits of sustainable manufacturing. Education programs and campaigns can influence consumer behaviour and encourage demand for eco-friendly products.
Regulatory Support and Incentives: Governments can offer incentives, tax breaks, or subsidies to businesses adopting sustainable practices. Strengthening regulations and setting clear standards for sustainability can also drive industry-wide improvements.
Supply Chain Transparency and Engagement: Encourage transparency across the supply chain by working closely with suppliers to ensure ethical sourcing, reduced emissions, and adherence to sustainability standards. Engaging suppliers in sustainability initiatives can have a cascading effect on the entire manufacturing process.
Lifecycle Thinking and Design: Incorporate sustainability considerations from the product design phase itself. Develop products that are durable, recyclable, or biodegradable, and consider the entire lifecycle impact, including raw material extraction, manufacturing, distribution, use, and disposal.
Investment in Infrastructure: Build necessary infrastructure for sustainable practices, such as renewable energy sources, recycling facilities, and efficient transportation networks. Infrastructure development supports the adoption of eco-friendly manufacturing processes.
Standardization and Metrics: Develop standardized metrics and reporting frameworks to measure and communicate sustainability efforts effectively. This facilitates comparison, benchmarking, and better decision-making across industries.
Continuous Improvement and Adaptation: Embrace a culture of continuous improvement by regularly reviewing and updating sustainability strategies. Adapt to new technologies, market demands, and regulatory changes to stay ahead in sustainable manufacturing.
Consumer Engagement and Responsiveness: Engage with consumers through transparent communication about sustainability efforts. Respond to changing consumer preferences and behaviours by offering eco-friendly products and services.
By employing these strategies and promoting a holistic approach to sustainability, businesses can navigate challenges in sustainable manufacturing and make significant strides towards creating a more environmentally friendly and socially responsible industry.
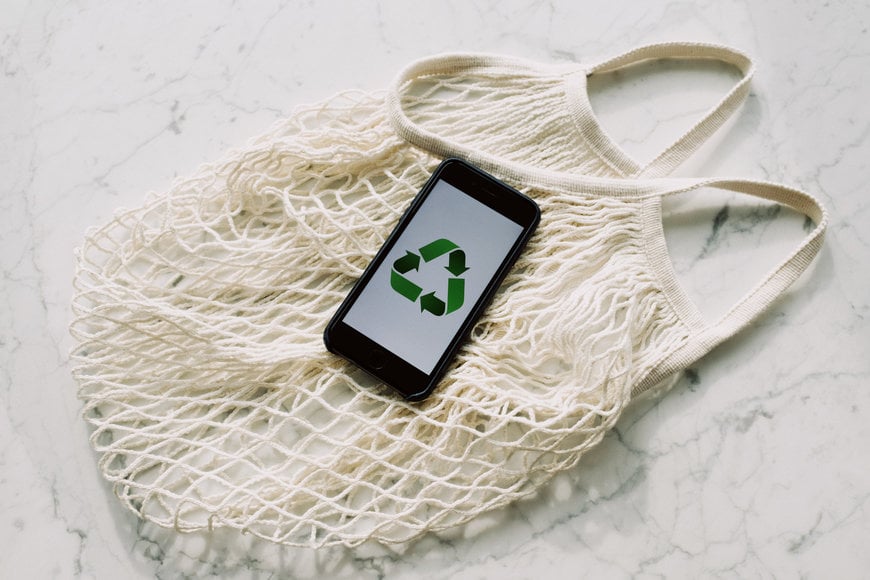
Leading Manufacturers Prioritizing Sustainability
Companies that practice sustainable manufacturing are those that prioritize reducing their environmental impact, while maintaining economic viability and social responsibility. Here is a compilation of companies that engage in sustainable manufacturing across various industries such as transportation, food and beverage, fashion, and more. These companies prioritize minimizing their environmental footprint while ensuring economic sustainability and social responsibility.
Unilever's focus on sustainability covers its products, supply chain, partners, and global governance – and, with a staggering 3.4 billion people globally using Unilever’s 400-plus brand names every day, the impact that such brand corporations can have is crucial. The company is pushing towards zero emissions in its operations by 2030, and net zero emissions across its value chain by 2039, alongside finding new low-carbon ingredients, expanding its plant-based product range and developing fossil-fuel-free cleaning and laundry products.
Vestas, a renowned Danish wind turbine manufacturer, is at the forefront of sustainable energy solutions worldwide. Recognized as the second most sustainable company globally according to The Corporate Knights Index, Vestas is committed to achieving carbon neutrality by 2030 without relying on carbon offsets. Additionally, the company aims to manufacture wind turbines that generate zero waste by 2040. Not only is Vestas a leader in sustainability, but it also pioneers global energy advancements. In a groundbreaking initiative, Vestas successfully saved 9.3 tonnes of emissions during the pilot program of the world's first hydrogen-powered offshore service vessel, surpassing traditional vessels in terms of environmental impact reduction.
Nestlé, the world's largest food and beverage company, firmly believes in the transformative power of food to improve the quality of life for all individuals, both in the present and for future generations. In pursuit of its objectives, Nestlé has set forth several ambitious goals, including:
- By the year 2030, Nestlé aims to reduce greenhouse gas emissions by 50%, and ultimately achieve net zero emissions by 2050.
- Nestlé is committed to ensuring that its primary supply chains for key ingredients are 100% deforestation-free by 2025.
- Between 2021 and 2023, Nestlé strives to decrease water usage in its factories by an impressive 6 million cubic meters.
- Nestlé plans to source 20% of its key ingredients through regenerative agriculture methods by 2025, with a further target of 50% by 2030.
- By 2025, Nestlé aims to design more than 95% of its plastic packaging for recycling, and continues to work diligently towards achieving 100% recyclability or reusability. Through these commitments, Nestlé demonstrates its unwavering dedication to sustainability and responsible practices, ensuring a brighter and more sustainable future for all.
Turkish electronics manufacturer Arçelik has had a sustainable focus since it was founded in 1955 with the mission: ‘Respects the Globe, Respected Globally’. The company is committed to reach net-zero emissions in the value chain by 2050.
Since 1985, Patagonia has been committed to preserving and restoring the natural environment by pledging 1% of sales and contributing over US$100 million in grants. Internally, Patagonia's Supply Chain Environmental Responsibility Program focuses on measuring, reducing, and eliminating environmental impacts in the manufacturing process. Notable achievements include: 98% of the line utilizing recycled materials, 86% of products being Fair Trade Certified, repairing over 100,000 garments in 2020, and recycling discarded fishing nets to prevent 935 tonnes of plastic waste from polluting the oceans.
BMW, the German automotive manufacturer, is at the forefront of sustainable vehicle development, paying meticulous attention to every aspect. The brand's commitment to sustainability and comfort is evident in their innovative practices, such as eliminating methane gas production, minimizing waste tannery water, and significantly reducing CO2 emissions. Furthermore, BMW sets a new standard by incorporating faux-leather seats made from recycled cactus, showcasing their dedication to both luxury and environmental responsibility.
Vehicle manufacturer Peugeot firmly uphold the belief that sustainability should be upheld throughout every stage of a product's lifecycle. During the production phase, Peugeot ensures that their vehicles consist of approximately 30% green materials on average. Furthermore, these vehicles are designed to be environmentally friendly and Peugeot consistently strives to develop clean technologies. Even after their useful life on the road, Peugeot's end-of-life recycling program aims to achieve an impressive 95% recovery rate for vehicles of all makes, with a minimum of 85% parts reuse and materials recycling.
Dassault Systèmes, a technology company with a strong focus on sustainability, offers collaborative virtual environments that foster the creation of sustainable innovations. The company has set a goal to achieve climate neutrality by 2040 and has been recognized by Corporate Knights as one of the top 100 most sustainable corporations in the world for 2021. Dassault Systèmes firmly believes that climate change presents not only significant risks but also immense opportunities for sustainable innovation, making it one of the most crucial challenges and prospects in history.
Stella McCartney, the renowned global fashion label, has gained recognition for its commitment to vegetarian options ever since its establishment in 2001. Notably, the brand actively avoids utilizing materials such as leather, feathers, and fur, instead opting for sustainable alternatives derived from grape waste and recycled industrial materials. In a remarkable display of dedication, Stella McCartney stood as the sole representative from the fashion industry at COP26 in 2021. Furthermore, in 2023, the brand introduced its inaugural garment specifically designed to be returned and transformed into new yarn during its end-of-life phase.
Schnitzer Steel, a renowned sustainability-focused company based in Portland, is making significant strides towards a greener future. In 2022 alone, it successfully recycled over 5 million metric tonnes of metals, resulting in the avoidance of approximately 5.5 million metric tonnes of CO2e emissions. Furthermore, the company has maintained a commendable record of utilizing 100% net carbon-free electricity across its operations. In line with its commitment to sustainability, Schnitzer Steel has recently introduced GRN Steel, a range of steel products that boast net-zero carbon emissions. The company's 2022 Sustainability Report reveals that it sold an impressive 465,000 short tonnes of finished steel products, all crafted from recycled ferrous metals. Schnitzer Steel's dedication to environmental responsibility is evident in its achievements and initiatives, positioning it as a leader in the industry.
Pushing Forward
In order to attain sustainable manufacturing, it is crucial to establish the appropriate leadership approach, secure support from all stakeholders, and thoroughly evaluate the implications of change management.
Significant change is underway in the realm of sustainable manufacturing, and it requires a shift in mindset, particularly on the factory floor. Manufacturers who are willing to embrace this change will uncover opportunities for innovation. Sustainability goals will serve as inspiration for creative green design and the implementation of new technologies. On the other hand, those who are unprepared may find themselves falling behind.
However, by focusing on long-term results, collaborating with industry stakeholders, and adopting a deliberate and coordinated approach, manufacturers have the ability to achieve substantial benefits in their journey towards sustainability. These benefits encompass enhanced competitiveness and efficiency, as well as reduced costs and risks. Nevertheless, the true indicators of success will extend far beyond the confines of the factory. By driving measurable sustainability outcomes, manufacturers also possess the ability to generate enduring social value.
Since 1985, Patagonia has been committed to preserving and restoring the natural environment by pledging 1% of sales and contributing over US$100 million in grants. Internally, Patagonia's Supply Chain Environmental Responsibility Program focuses on measuring, reducing, and eliminating environmental impacts in the manufacturing process. Notable achievements include: 98% of the line utilizing recycled materials, 86% of products being Fair Trade Certified, repairing over 100,000 garments in 2020, and recycling discarded fishing nets to prevent 935 tonnes of plastic waste from polluting the oceans.
BMW, the German automotive manufacturer, is at the forefront of sustainable vehicle development, paying meticulous attention to every aspect. The brand's commitment to sustainability and comfort is evident in their innovative practices, such as eliminating methane gas production, minimizing waste tannery water, and significantly reducing CO2 emissions. Furthermore, BMW sets a new standard by incorporating faux-leather seats made from recycled cactus, showcasing their dedication to both luxury and environmental responsibility.
Vehicle manufacturer Peugeot firmly uphold the belief that sustainability should be upheld throughout every stage of a product's lifecycle. During the production phase, Peugeot ensures that their vehicles consist of approximately 30% green materials on average. Furthermore, these vehicles are designed to be environmentally friendly and Peugeot consistently strives to develop clean technologies. Even after their useful life on the road, Peugeot's end-of-life recycling program aims to achieve an impressive 95% recovery rate for vehicles of all makes, with a minimum of 85% parts reuse and materials recycling.
Dassault Systèmes, a technology company with a strong focus on sustainability, offers collaborative virtual environments that foster the creation of sustainable innovations. The company has set a goal to achieve climate neutrality by 2040 and has been recognized by Corporate Knights as one of the top 100 most sustainable corporations in the world for 2021. Dassault Systèmes firmly believes that climate change presents not only significant risks but also immense opportunities for sustainable innovation, making it one of the most crucial challenges and prospects in history.
Stella McCartney, the renowned global fashion label, has gained recognition for its commitment to vegetarian options ever since its establishment in 2001. Notably, the brand actively avoids utilizing materials such as leather, feathers, and fur, instead opting for sustainable alternatives derived from grape waste and recycled industrial materials. In a remarkable display of dedication, Stella McCartney stood as the sole representative from the fashion industry at COP26 in 2021. Furthermore, in 2023, the brand introduced its inaugural garment specifically designed to be returned and transformed into new yarn during its end-of-life phase.
Schnitzer Steel, a renowned sustainability-focused company based in Portland, is making significant strides towards a greener future. In 2022 alone, it successfully recycled over 5 million metric tonnes of metals, resulting in the avoidance of approximately 5.5 million metric tonnes of CO2e emissions. Furthermore, the company has maintained a commendable record of utilizing 100% net carbon-free electricity across its operations. In line with its commitment to sustainability, Schnitzer Steel has recently introduced GRN Steel, a range of steel products that boast net-zero carbon emissions. The company's 2022 Sustainability Report reveals that it sold an impressive 465,000 short tonnes of finished steel products, all crafted from recycled ferrous metals. Schnitzer Steel's dedication to environmental responsibility is evident in its achievements and initiatives, positioning it as a leader in the industry.
Pushing Forward
In order to attain sustainable manufacturing, it is crucial to establish the appropriate leadership approach, secure support from all stakeholders, and thoroughly evaluate the implications of change management.
Significant change is underway in the realm of sustainable manufacturing, and it requires a shift in mindset, particularly on the factory floor. Manufacturers who are willing to embrace this change will uncover opportunities for innovation. Sustainability goals will serve as inspiration for creative green design and the implementation of new technologies. On the other hand, those who are unprepared may find themselves falling behind.
However, by focusing on long-term results, collaborating with industry stakeholders, and adopting a deliberate and coordinated approach, manufacturers have the ability to achieve substantial benefits in their journey towards sustainability. These benefits encompass enhanced competitiveness and efficiency, as well as reduced costs and risks. Nevertheless, the true indicators of success will extend far beyond the confines of the factory. By driving measurable sustainability outcomes, manufacturers also possess the ability to generate enduring social value.