www.industry-asia-pacific.com
13
'23
Written on Modified on
Technology Updates That Drive Machine Tool Innovation
K.A. Gerardino explains how Developments in machine tool technology and innovation-driven by high demand are driving the machine tool industry forward at a rapid pace. .
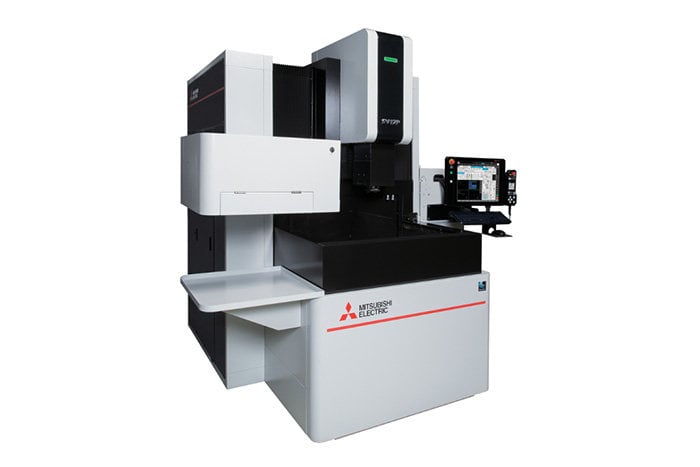
The machine tools industry has changed drastically over the last few years. They assist in the economical manufacture of standardized parts for use in everything from automobiles to aircraft.
In fact, the global machine tools industry is projected to grow by US$164.92 billion in 2028 at a CAGR of 5.5% during 2023-2028, according to Fortune Business Insights.
The impact of the Covid-19 pandemic has truly highlighted the power of digital technology and its potential in manufacturing like never before. And we expect this digital demand to rise. It is predicted that one in three companies will generate more than 15 percent of their revenue from digital products and services by 2023, compared to just one in six in 2020.
Machine tool makers clearly see that customers, partners, and distributors are ready for new ways of working that embrace the new trends in creating machine tools. Machine tools are becoming a vital part of smart systems; further giving rise to the trend of smart factories enabled with the cloud. Advancements in hardware and software are changing the machine tool industry. Industry trends in the coming years are likely to focus on these advancements, especially as they pertain to automation.
Machine tool trends
Today, machine tools offer advancements in: Artificial intelligence (AI), Cloud Computing, Green Manufacturing, Big Data & Analytics, Additive Manufacturing, Industrial Automation and CNC Software.
Artificial intelligence (AI): As the machine tool industry becomes automated to a greater degree, programs will need to be written and executed in real-time to manage those machines. That is where AI comes in. In the context of machine tools, AI can be used to monitor the programs the machine is using to cut parts, making sure they do not deviate from the specifications. If something goes wrong, AI could shut the machine off and run diagnostics, minimizing damage. AI can also assist in machine tool maintenance to minimize and address problems before they happen. For example, a program was recently written that can detect wear and tear in ball screw drives, something that had to be done manually before. AI programs like this can help keep a machine shop running more efficiently, keeping production smooth and uninterrupted.
MC Machinery’s latest EDM and precision milling technology includes wire and sinker EDMs, machining centers and automation. The company, a subsidiary of the Mitsubishi Corporation, is a supplier and servicer of fabrication and milling equipment, including Mitsubishi lasers, EDMs and automation systems. The new Sinker EDMs feature artificial intelligence (AI) adaptive control technology. The company says the Mitsubishi SV12P and SG12 sinker EDMs optimize performance, improve productivity, reduce electrical consumption, and take the guesswork out of estimating machining time. The AI technology is said to make logical use of condition-monitoring data. For example, these new machines can diagnose real-time problems within the burn and directly modify specific parameters for a stable and accurate output. This enables machine operators of all experience levels to produce quality results in complex cavities and shapes. Because the AI technology analyzes current sensor data to determine optimal conditions, it reduces overall electrode wear and costs. According to the company, by monitoring these parameters, the machine operates more efficiently and can more accurately predict machining times.
Cloud Computing: The data that IoT devices collect from production lines have great potential to transform manufacturing operations. In the traditional system, all the data handling and analysis activities take place through the in-house hardware and servers. This adds the cost of setting up and maintaining expensive IT infrastructure and restricts the accessibility of data to remote workforces. Cloud-based machine tools avoid the need for costly computer hardware and servers and allow the sharing of data across platforms. Cloud computing is an established trend in machine tools that enables on-premise users and remote workforces to collaborate in real-time. This approach improves manageability and reduces network maintenance.
Machine data also serves to detect quickly errors in production. To this end, c-Com GmbH of Aalen, a subsidiary of the precision tool specialist Mapal Group, is hosting on an open cloud platform collaborative data management for tools and other components in the production environment. This is to help companies gain a deep insight into their processes and find solutions faster to the problems they encounter. If production data is subjected to real-time monitoring, this immediately detects anomalies in the data streams. And analyzing the data in the context of the whole production process can provide precise details on which of the production factors, e.g., the tool, the machine, or the raw material, is deviating from the standard.
Predictive maintenance, or repairing a machine defect before it arises, is a solution provided by IoT software like Siemens MindSphere. This software saves operating data and renders it accessible via digital applications. Put oversimply, MindSphere can be likened to an operating system on a computer or cell phone. It processes the raw data captured by the production plant’s sensors and analyzes data patterns for signs of a machine defect, excessive power consumption, or imminent servicing on a critical part reaching the limit of progressive wear.
Green Manufacturing: The rise of global temperatures is directly related to each phase in the industrial revolution. The unchecked setup of manufacturing units and the wasteful use of resources in the growing phase of each industrial revolution has done irreversible damage to the planet. Thus, the fourth industrial revolution (Industry 4.0) of smart technologies does not have a free pass to utilize resources. This is why machine tool companies are shifting to sustainable materials, energy, and processes to reduce their impact on the environment. Due to this, green technologies are important among the machine tool trends. These sustainable solutions make the final product green, ensure a long lifetime, and promote circularity.
Okuma Corp. is set to offer a full line-up of "Green-Smart Machine" products defined as intelligent machine tools that contribute to resolving environmental issues by autonomously achieving both stable dimensional accuracy and reduced energy usage. The "Green-Smart Machine" eliminates operator intervention required to maintain high accuracy and reduce energy usage, and achieves Level 4 of the maturity models, "autonomous energy reduction with accuracy stability," where the machine autonomously controls the equipment. Carbon neutrality has already been achieved for the machines at the company's three domestic factories, which are the main production factories, ahead of schedule from October 2022. These automated and smart factories have been proven to reduce energy usage and produce products with high accuracy and high efficiency. An autonomous energy-saving function, "ECO suite plus," is incorporated as standard in Okuma's "OSP" series of NC units. It enables data analysis based on machine-operating information and equipment-specific operating information, supporting the recording of CO2 emissions for traceability. Including its predecessor "ECO suite," more than 42,000 units have been delivered since its launch in 2014, reducing factory energy usage worldwide.
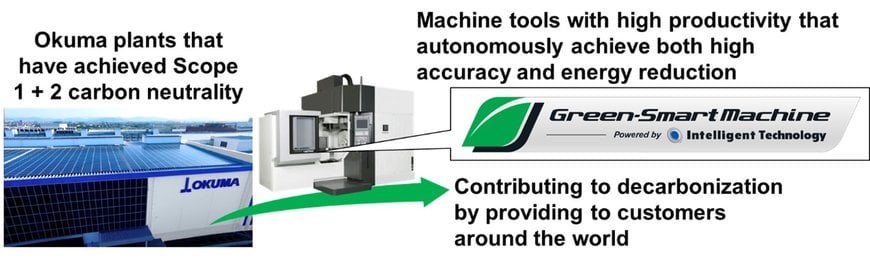
Image courtesy of Okuma
On the other hand, Ceratizit's sustainability formula is used to create high-performance tools using sustainable manufacturing techniques. The tool manufacturer has impressive characteristic values to back up its claims. The solid carbide milling cutter series from Ceratizit is particularly popular with customers and is used by many manufacturing companies. Now the tool manufacturer has produced a geometry of the cutter from a specially developed carbide grade with an extremely small carbon footprint. This ‘Green Carbide’ consists of over 99 percent high-quality secondary raw materials. In addition, the company ensures low-carbon manufacturing by using low-emission production processes and energy sources as well as consistently short transport routes throughout the process chain. At 2.6kg CO2/kg carbide, this allowed Ceratizit to achieve an unrivalled carbon footprint for a premium carbide grade. Producing the Green Carbide cutter generates only 4.4kg CO2/kg compared to 19.8kg CO2/kg for one of its conventional cutters. The tool manufacturer thus achieves a 78 percent reduction in CO2 and improves not only its own carbon footprint. Ceratizit customers will also enjoy the economic benefits in the future thanks to the small certified carbon footprint. Sustainability and performance are therefore not mutually exclusive at Ceratizit and are opening new opportunities in the machining industry.
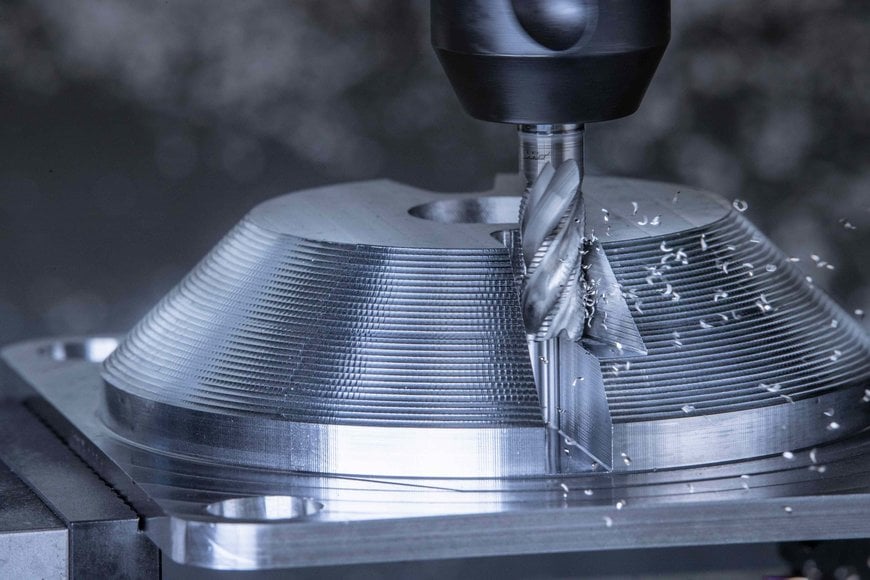
Ceratizit Silverline
Big Data & Analytics: From raw materials management to maintenance schedule planning, the process of capturing and storing data is critical to ensure agility in manufacturing systems. The data in a manufacturing company consists of information regarding assets, materials, processes, and customer feedback – all in different formats and protocols. For this myriad of data, the conventional methods of data handling are inefficient in performing predictive or advanced analytics. Moreover, big data analytics with machine learning (ML) algorithms find patterns in the data and provide real-time insights. The vast amount of data that these analytics platforms process improves worker safety and efficiency while also simplifying product innovation and reducing costs.
The machine tools and laser technology manufacturer Trumpf SE + Co. KG of Ditzingen is focusing on data-based innovations. This hi-tech firm has created a digital business model it has named Pay Per Part. Trumpf’s Pay Per Part allows customers to pay solely for their use of the fully automated laser systems from our TruLaser Center 7030 series. Although the installation itself is sited in the customer’s production plant, it is remote-monitored and controlled from the Trumpf Remote Control Center in Neukirch. Trumpf experts also offer their support in programming and configuring the machine. In the end the customer pays for the completed parts a price guaranteed in advance. This business model benefits customers in that they can leave the machine running in three-shift mode without having to recruit or deploy additional personnel.
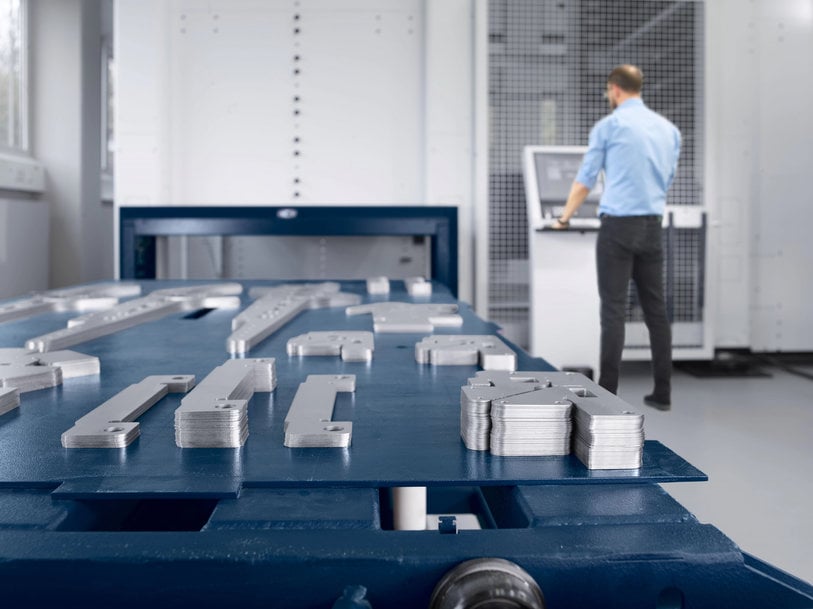
Tru Laser Center 7030 by Trumpf
Additive Manufacturing: Additive manufacturing (AM) provides an efficient and quick method for converting a concept into the final product. Computer-aided designing (CAD) has taken away the limitations in product design and additive manufacturing breaks the barriers of materializing unconventional designs. This enables intricate designs which otherwise incur a large production cost with standard manufacturing techniques. But the current methods of additive manufacturing do not support mass production. To tackle this, innovations in 3D printing reduce the cost of transition from traditional manufacturing processes. The implementation of this manufacturing trend also paves the way for mass customization, localized and distributed manufacturing, and on-demand production.
AM offers a whole range of benefits in terms of more cost- and resource-efficient production resulting from new opportunities for design, manufacturing, and business models. Of course, AM also offers room to improve its own carbon footprint. Italy-based 3D4MEC, a spin-off of the University of Genoa, is doing the math to produce a 3D-printed joint system that consists of just a few components: It takes about 44 hours to produce the innovative joint on its in-house 3D4STEEL printer. Production with AM results in a component with a total volume of 180 cm3 (1.8 kg) with a small amount of waste (about 110 g), which is less than 8 percent of the component material. If the component had been produced by a milling process, this would have resulted in a waste volume of about 35 kg. Production using additive manufacturing thus enables the manufacture of new complex geometries in conjunction with a 95 percent reduction in the amount of waste compared to conventional technologies.
The powder bed process uses powders with a particle size between 25 and 70 micrometers. The production process is generally associated with a waste of a few percent. It occurs in the contour of the object when it comes into contact with the laser and the powder melts. The printer for the production of the cardan joint has a cube-shaped workspace of edge length 110 mm. The 3D4STEEL printers also allow continuous recycling of the powder even during the printing process. Therefore, only a minimal volume of powder is used here that is required for the process, which also reduces the operator's interaction with the powder and its distribution in the environment. In the example, the system was loaded with 30 kg of metal powder for production in job 1 and then in jobs 2 and 3. At the end of the production of the three print jobs, 27 kg of powder was still available for the next production, which means that around 98 percent of the powder was not converted into the respective end product.
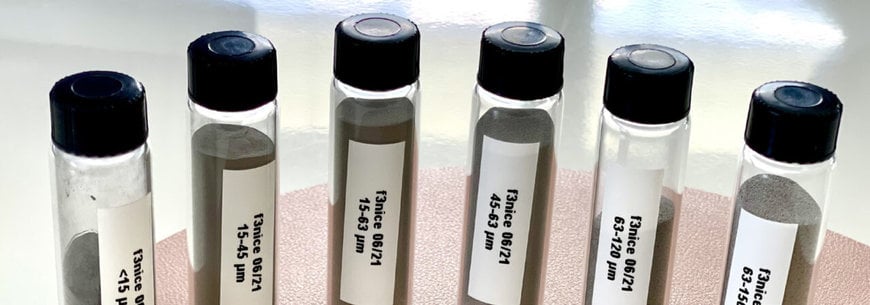
Different powders from recycled metals// @F3nice
Industrial Automation: Since the first industrial revolution, all process and equipment improvements aim to implement and improve manufacturing with automation. The reduction of human involvement in repetitive and hazardous tasks makes the production line safer and generates significant cost-saving for factories. But the capital and complexity of such automated equipment increase exponentially with the level of factory automation. However, recent innovations in control systems and robotics make its implementation easy and more cost-effective. This makes robotic automation the most important technology among all the manufacturing trends. Industrial automation simplifies a wide variety of processes in the production line including material handling, assembly, painting, and other machining and finishing processes.
Hurco has introduced a new line of shopfloor automation solutions under the brand name ProCobots. This initiative has started from our Hurco USA head office where customers have requested for an automation solution that is easy to use, flexible and can be efficiently operated by their existing machinist. The ProCobot provides easy to use one robot to one machine tending capability, without having to utilise a third-party software. This allows an existing Hurco user to utilise the automation manager to command the robot and schedule the CNC programs for various parts loaded onto the parts station. A standard integration package that includes an auto-door, pneumatic vise and an interface utility box makes this a quick "plug and play" solution for Hurco machines. The ProCobot can be installed on an existing Hurco machine, and up and running in less than a week. If you need to swap the ProCobot from a machining centre to a lathe to support a production run, it can be moved easily and set-up within a day. Hurco ProCobot caters to both batch production and high-mix low volume production.
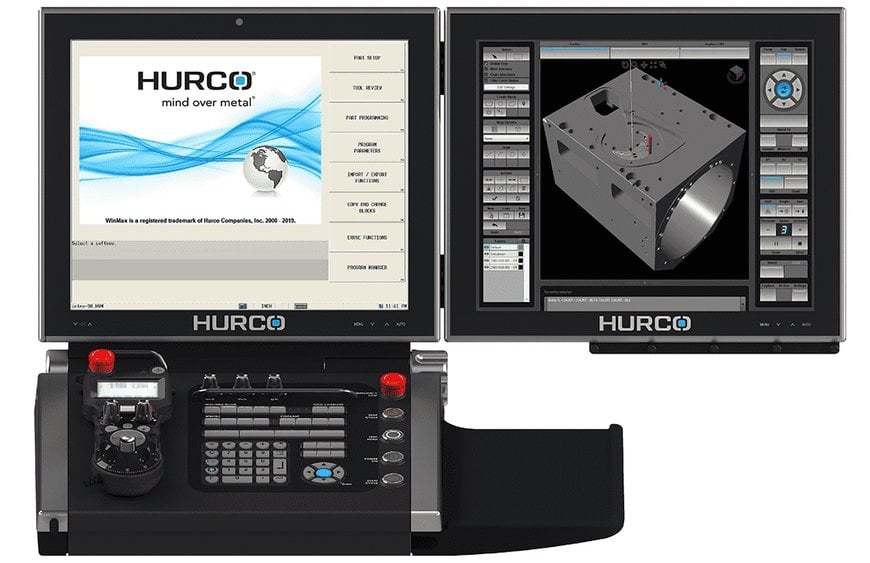
Hurco ProCobotCNC Software
CNC Software: Advancements in computer-aided manufacturing (CAM) software used in CNC machining allows for even further precision in manufacturing. CAM software now allows machinists to use digital twinning — the process of simulating a physical object or process in the digital world. Before a part is physically manufactured, digital simulations of the manufacturing process can be run. Different toolsets and methods can be tested to see what is likely to produce the optimal result. That reduces cost by saving material and man-hours that might have otherwise been used to refine the manufacturing process. Newer versions of machining software like CAD and CAM are also being used to train new workers, showing them 3D models of the parts, they are making and the machine they are working with to illustrate concepts. This software also facilitates faster processing speeds, meaning less lag time and quicker feedback for machine operators while they work. Multi-axis machine tools are more efficient, but they also come at a higher risk for collision as multiple parts work at once. Advanced software cuts down on this risk, in turn cutting downtime and lost materials.
Siemens Digital Industries has expanded the Sinumerik One “digital-native” CNC. This new control generation from Siemens is now offered with innovations in software and hardware, with the goal of enabling machine builders and end-users a full digital twin of the machine tool and machining sequences. With the new system software Sinumerik V6.20, there are new technology functions in Sinumerik One that are designed to simplify operation, reduce machine wear, and increase productivity. With these developments, Siemens is demonstrating how the Sinumerik One machine tool control system can be optimally used for digital transformation in a highly productive, flexible, and modular way. Sinumerik One’s hardware features include new keyboards and machine control panels (MCPs) available from 15" to 24" to match the design of the HMI panel, as well as the Simatic Industrial Thin Clients (ITCs) and industrial PCs with increased performance and a full HD resolution up to 1920 × 1080 pixels. The new CNCs are also integrated in the digital twin of Sinumerik One (Run MyVirtual Machine), so that the appearance and operation correspond to the real control in every respect. In addition, the digital twin has been equipped with new features that simplify engineering and work preparation. Examples of the many innovations include a 3D option that offers support for a second channel, often used for robotic integration.
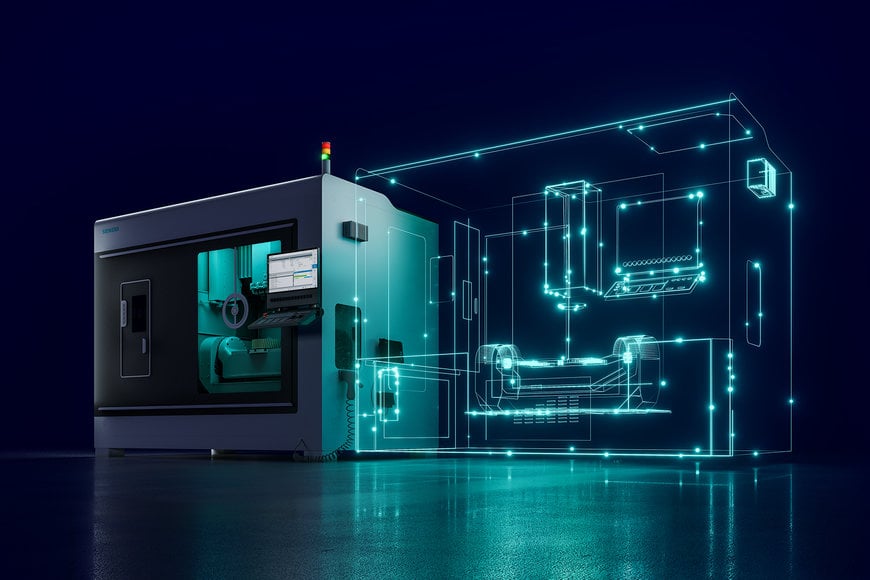
Photo Credit: Siemens Digital Industries
Conclusion
Challenging headwinds in the macroeconomic environment have given rise to new trends in the machine tool sector. In the face of disruption across global supply chains, companies have learnt the importance of staying prepared to ensure sustainable business development. It is technologies like this that will be key to enable manufacturers to pursue a digitised future, embrace the latest manufacturing industry trends and create revolutionised organisations. With exciting new machining advancements, digital solutions, monitoring capabilities, and material discoveries on the horizon, the future looks bright. This will lead to remarkable innovation and unprecedented productivity.