Fiber laser processing machine and automatic sorting system triple productivity and help improve worker safety
Yutaka Steel Industries Co., Ltd. which is headquartered in Sasaguri-machi, Kasuya-gun, Fukuoka in Japan, has improved the efficiency of its steel processing operations with the installation of a Mitsubishi Electric MELLASER fiber 2D laser processing machine (LPM).
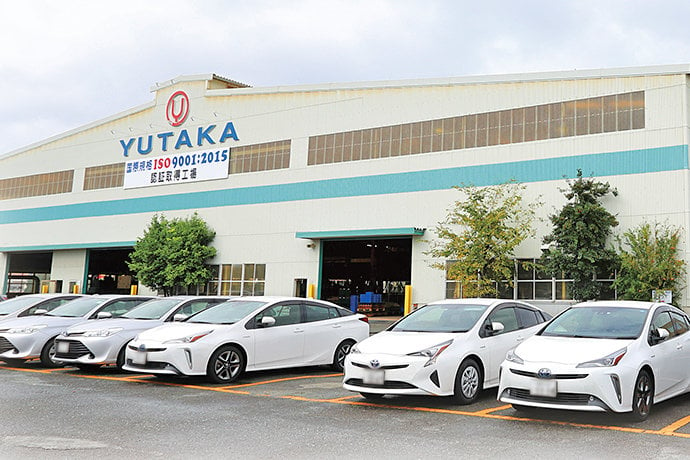
Yutaka Steel Industries Co., Ltd.
Key Points
1. Mitsubishi Electric MELLASER fiber 2D LPM reduced anomalies in processing quality caused by variations in feedstock.
2. The ASTES4 automatic sorting system reduced physical workload, as heavy raw materials no longer need to be loaded manually.
3. Remote services support energy saving efforts.
For over sixty years since it was founded in 1958, Yutaka Steel has expanded its steel processing business, mainly in the Kyushu area of Japan, establishing its position as a market leader in the region.
Steel fabricated by the company has been utilized in large-scale projects in the Tokyo metropolitan area, for example, its products have been used in the steel frame for the roof of the new Japan National Stadium.
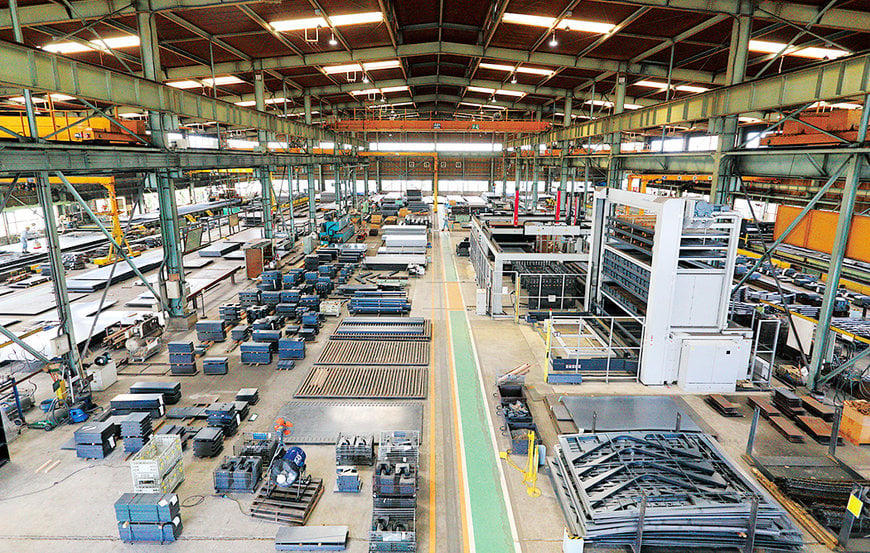
Inside of Yutaka Steel’s Fukuoka Plant, where steel sheets are cut using the GX-F60 fiber laser processing machine. This device and the ASTES4 automatic sorting system are installed on the right of the picture. The products processed using the GX-F60 and ASTES4 can be seen on the left of the picture.
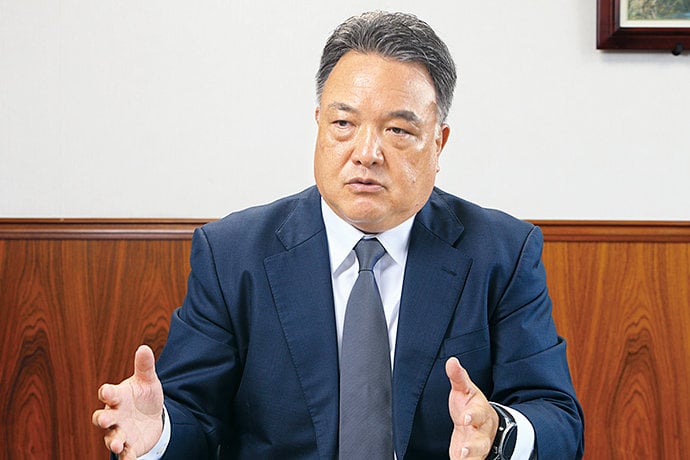
Hideki Makiuchi, President and CEO, Yutaka Steel Industries Co., Ltd.
Previously, Yutaka Steel only used CO2 laser processing machines for laser cutting. However, as Katsuya Komaya, Manager of the Fukuoka Plant, explains, “Now that fiber laser processing machines are much more widespread and the knowledgebase has grown, we decided that their reliability was sufficiently established for us to consider introducing them.” He adds, “In the past, sheets cut by our CO2 laser processing machine had to be sorted manually by the workers when they arrived each morning, which was time-consuming, meaning that our potential production capacity was not being fully realized. We were also concerned about the physical burden of moving heavy materials and products. That’s why we were looking for an automatic sorting system, as well as a fiber laser processing machine that could provide high-quality products.”

Katsuya Komaya, Manager of Fukuoka Plant
The Fukuoka Plant is mainly responsible for steel sheet cutting. 60 to 70% of the resulting products are used as building materials for the construction industry. The rest are used in construction machinery and require a higher cutting and surface quality, as well as consistency to meet accuracy requirements due to limited margins for variability. In addition to a machine to meet these requirements, Yutaka Steel also evaluated how automatic sorting could offer a solution to effectively enhance production. As a result, Mitsubishi Electric’s ML4020GX-F60 fiber 2D laser cutting machine (referred to as GX-F60 below) and ASTES4 automatic sorting system were added to the shop floor for the processing of materials for construction equipment.
Driving consistency in product quality
Since the company started operating the new equipment, the GX-F60 has resulted in greater consistency than the existing CO2 laser cutting machine – there is now less variation in processing quality, despite raw material variability. With the CO2 laser cutting machines, the operator needs to adjust the conditions each time, but the GX-F60 offers pre-set options. “This means every operator can cut with the same quality, which is a big benefit,” says Komaya.
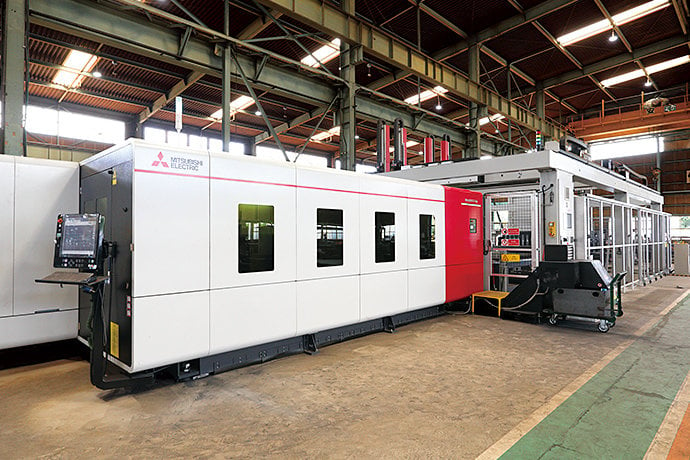
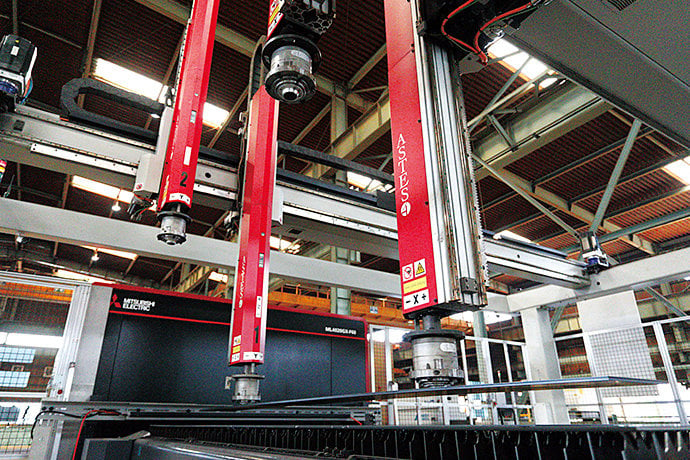
The automation of laser cutting operations through the combination of the GX-F60 and ASTES4 improved work efficiency and reduced the physical workload for operators.
There are also clear positive results in terms of efficiency, labor-saving, and reduced physical workload, which were all aims of introducing the GX-F60 in combination with the ASTES4. “We perform oxygen-assisted cutting, the same as with the existing CO2 laser processing machines, but with the GX-F60, we can double productivity. In combination with the ASTES4, this has been further improved and our throughput can be increased threefold compared to previous processes. We have also seen a reduction in running costs, including consumables, like nozzles, as well as power and oxygen consumption,” says Komaya.
There are other major benefits, besides improved productivity and cost savings. Now that operations have been automated with the ASTES4, heavy materials no longer need to be moved manually before and after processing. This has reduced potential operational risks, helping to improve employee safety. Manual handling could also damage the surface of the material, which is no longer a concern since introducing the new equipment.
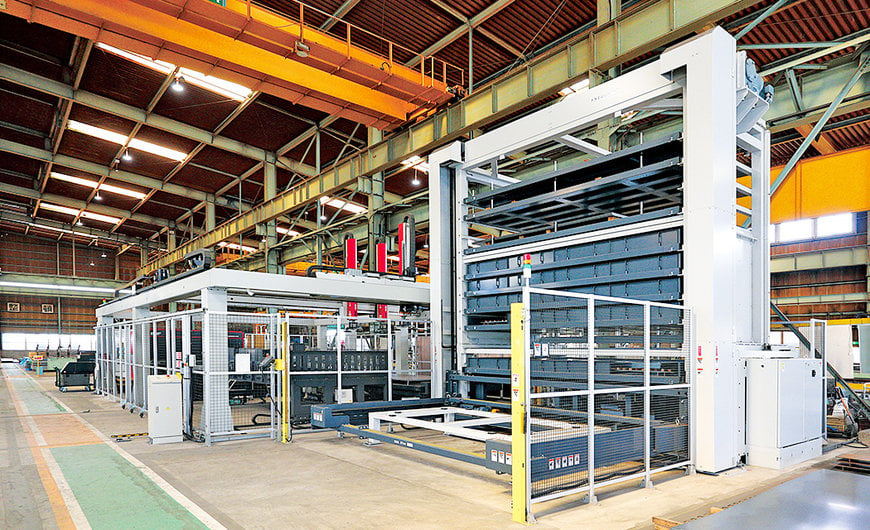
The introduction of the ASTES4 handling system means heavy steel sheets and processed products no longer need to be manually moved and stacked, reducing potential operational risks. “Increased safety is another major benefit,” says Komaya.
Operations can be checked remotely
Yutaka Steel is also using Mitsubishi Electric’s Industrial Internet of Things (IIoT) remote service, iQ Care Remote4U. This allows Katsuya Komaya to check the automated work schedule and status of the GX-F60 and ASTES4 from his office PC or smartphone. The plant operates 24 hours a day, running autonomously at night, so having up-to-date information on key activities is vital. Cameras are installed on the ASTES4 handling system as standard, so when an alarm goes off at night, it is possible to review the recorded images to support troubleshooting. Currently, remote monitoring is mainly used to check the status of the machines, but going forward, the company plans to analyze its electricity and gas consumption in more detail, to help optimize usage and costs.
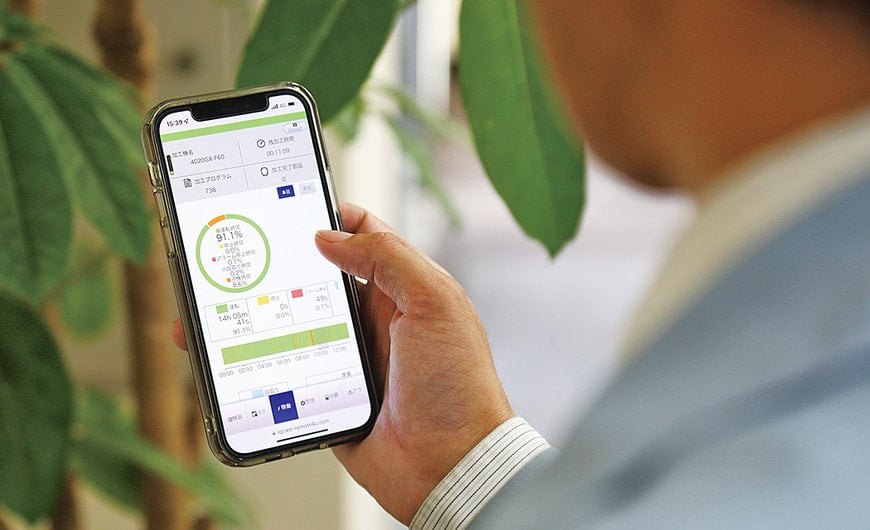
The automated processes and the status of the machines can be monitored remotely with iQ Care Remote4U. Katsuya Komaya usually accesses this information on his office PC, but he can also log in to the system on his smartphone when he’s away from the office.
Looking to the future, Komaya says, “We want to utilize Mitsubishi Electric’s equipment and services to further improve productivity and employee safety as we continue to respond to our customers’ requirements.”