Pressing Need for “Peak Shift” Cuts Down Electricity Bills, With Payback in Less Than One Year
Aida Engineering Malaysia SDN. BHD., a Malaysian subsidiary of Japan-based Aida Engineering Co., Ltd., develops, manufactures and sells press machines ranging from 80 to 300 tons. They selected Mitsubishi Electric's energy-saving data collection server “EcoWebServer III” to visualize and manage their electricity consumption, succeeding in cutting down their electricity cost by 15%.
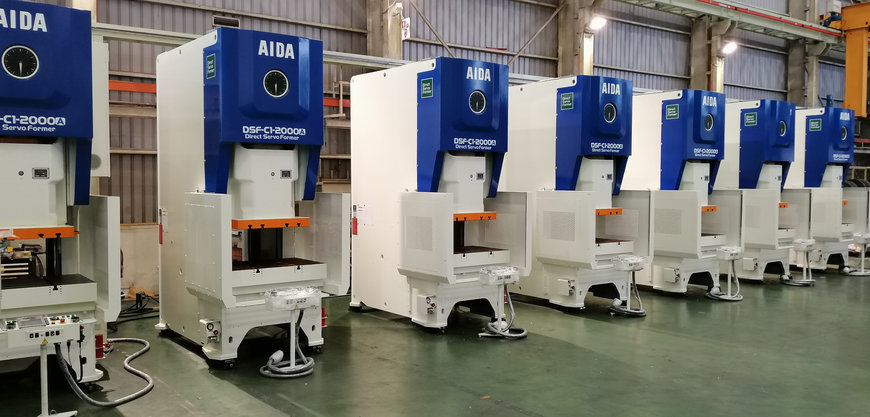
Aida Engineering Malaysia manufactures more than 500 press machines annually for markets worldwide.
Established in 1995, Aida Engineering Malaysia plays an important role as one of Aida Engineering’s five manufacturing bases outside Japan where it mainly manufactures press machines for markets worldwide with an annual production capacity of more than 500 units.
Their challenge began when the local power company came to them and pointed out that their six-month energy consumption exceeded 3 million kWh in total. They were obliged to hire a dedicated energy manager who would be responsible for checking monthly electricity consumption and reporting it to local authorities every six months.
The company's first response was to visualize their power consumption and tried to cut electricity bills by identifying peaks. There are two types of electricity rates in Malaysia depending on the time of day. Therefore, if the peak in the factory’s power consumption comes when the price is high, you may want to shift that demand to the time of day when electricity costs are lower - the so-called “peak shift”, which would then help you lower your electricity bills.
Thinking along similar lines, the energy manager at Aida Engineering Malaysia decided to go around the factory every month to manually check the power meters and write down the figures. But this way of recording the data didn’t help them identify the peak, since they could only see the monthly consumption. To get a clearer understanding of the peak levels they would need to continually measure the electricity consumption, perhaps every 30 minutes for 24 hours/ seven days a week.
To visualize their power consumption more effectively they turned to Mitsubishi Electric, who suggested to use an energy-saving data collection server called “EcoWebServer III.”
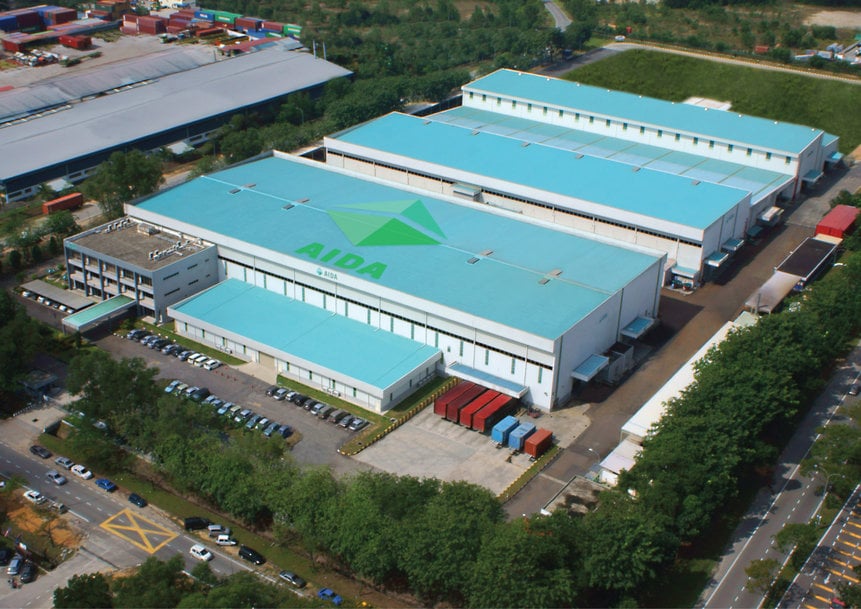
Aida Engineering Malaysia needed to measure the electricity consumption every 30 minutes for 24 hours/ seven days a week.
The pay-back period was shorter than one year
EcoWebServer III can be part of a demand management system, as it collects power consumption data from facilities and equipment via LAN and enables remote monitoring from the operators’ PC. It can also send out an email alert when consumption increases rapidly.
A key feature of EcoWebServer III is the capability to constantly measure real time power consumption data and visualize it as a graph to let you compare it with your target figures. By looking at the graph, it enables you to understand not only when the peak comes, but also helps determine if your improvement measures were effective.
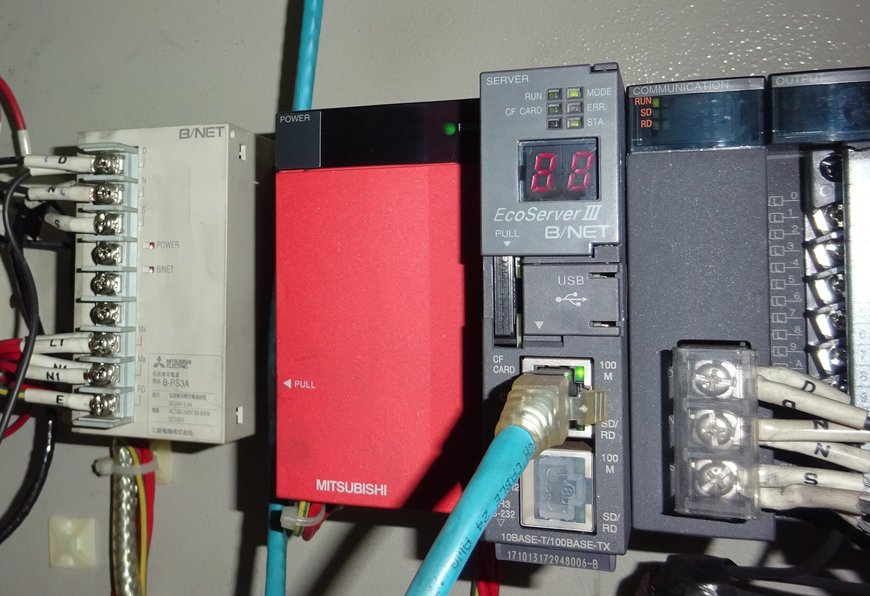
EcoWebServer III was introduced to visualize electricity consumption in the factories.
When Aida Engineering Malaysia introduced the EcoWebServer III to identify peak power consumption, they also installed Mitsubishi Electric’s “EcoMonitor Series” energy measurement units to measure the energy use of equipment and individual production machines. They compared and analyzed each data sets to promote peak-shift initiatives. For example, they turned off the air conditioning when using machines that consume a large amount of electricity while also trying to use such machines in evenings when air conditioning demand was low.
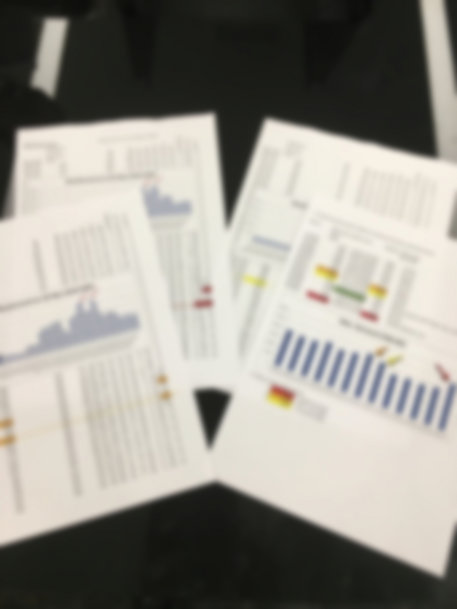
Data collected by the EcoWebServer lll was utilized for analysis to promote peak-shift initiatives.
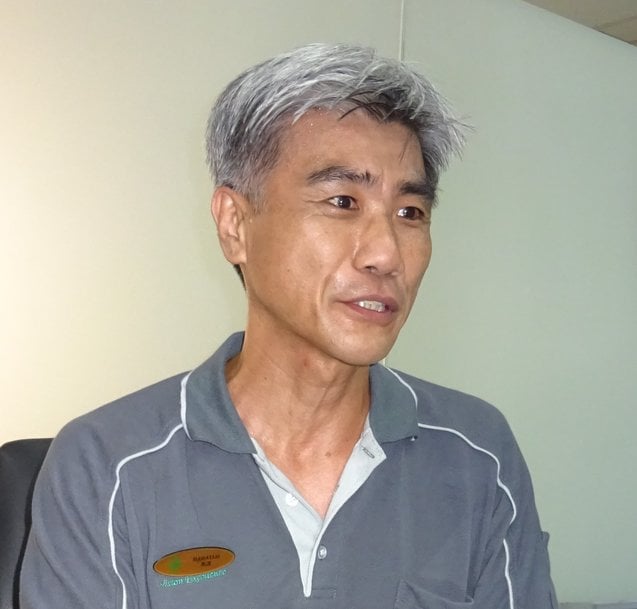
“We were able to reduce our electricity bills by 15%,” explained Hideki Mawatari, Maintenance Manager of Aida Engineering Malaysia.
“By shifting the peak demand to the time of day when the energy price is low, we were able to reduce our electricity bills by 15%,” explained Hideki Mawatari, Maintenance Manager of Aida Engineering Malaysia. “The effect was immense. We were able to collect the data we needed, and what’s more, the pay-back period was shorter than one year.”
“The EcoWebServer lll was very easy to install,” Hideki Mawatari added. “We considered other choices, but what attracted us about Mitsubishi Electric’s solution was the fact that the EcoWebServer lll can be easily connected with existing equipment. It is also scalable so we can add up as we go along.”
Promoting awareness of energy saving through “energy per unit” management
Having succeeded in shifting the peak energy demand, Aida Engineering Malaysia’s next challenge is to reduce the total amount of energy they consume.
Energy saving could be simply executed by turning off all your machines, but then you are unable to produce, leading to reduced income. Air conditioning was initially meant to maintain the quality of the products, so a long downtime could potentially impact production quality.
“Our focus now is to maintain product quality and reduce energy consumption at the same time,” said Mitsuru Hirasawa, Managing Director of Aida Engineering Malaysia. “We will increase the number of items we collect data from, and will utilize EcoWebServer III to determine the energy per unit produced (EPU). We also have plans to introduce preventive maintenance and integrated management of energy and production data, which we will eventually make accessible from the factory floor.”
EcoWebServer III can be connected to PLCs to collect production data in real time, making it easy to visualize power consumption on a per unit basis. By making the data accessible from the factory floor, it will encourage factory workers to promote energy-saving initiatives. As a result, power consumption should start decreasing on a per-unit basis, which will eventually lead to saving total energy demand.
“Our focus now is to maintain product quality and reduce energy consumption at the same time,” said Mitsuru Hirasawa, Managing Director of Aida Engineering Malaysia.
See details of AIDA ENGINEERING (M) SDN. BHD. at:
http://www.aida.com.sg/aida-engineering-malaysia
Learn more about Mitsubishi Electric’s power monitoring products:
https://www.mitsubishielectric.com/fa/products/pmng/ems/index.html